あなたはいくつ当てはまる?
ミスが多い人のあるある行動と対処法
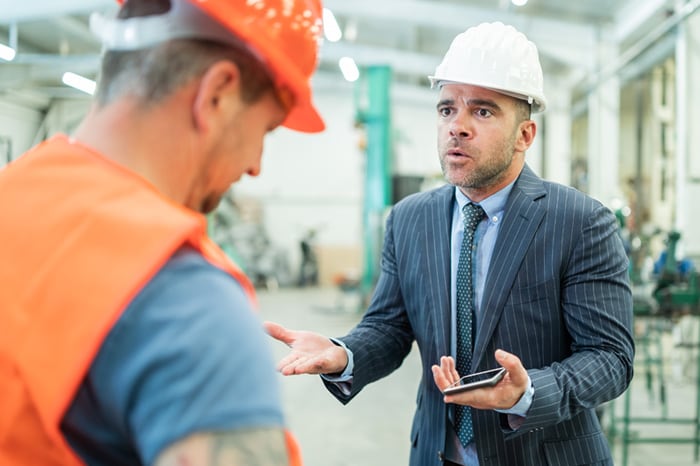
「気をつけているつもりなのに、なぜかミスをしてしまう」
誰しも一度は、このような悩みを抱えたことがあるのではないでしょうか?
ヒューマンエラーは自身の行動によって引き起こされる性質上、ミスをしたときに自分を責めてしまいがちです。もちろん反省は必要ですが、過度に自分を責める必要はありません。
重要なのはミスの原因を正しく把握し対策することです。
この記事では、ミスが多い人のあるある行動や対策を紹介します。
また、組織で取り組むヒューマンエラー対策や他社の取り組み事例もあわせて紹介します。
- この記事でわかること
製造業の労災発生数は業種別で最多、8割はヒューマンエラーに起因
製造業は他業種と比較して労働災害が多い業界です。大型機械や危険物を扱うため物理的な危険が常に存在するからです。
実際、厚生労働省が発表している「令和3年労働災害発生状況分析等」の資料では、以下の表のようなデータが発表されています。
<令和3年の業種別死傷者数>
業種 | 死傷者数 |
---|---|
全産業 | 149,918 |
製造業 | 28,605 |
建設業 | 16,079 |
陸上貨物運送事業 | 16,732 |
小売業 | 16,860 |
社会福祉施設 | 18,421 |
飲食店 | 5,095 |
全産業の労働災害による死傷者数の149,918件のうち28,605件が製造業で発生しており、上記6つの業種の中で最も多い数字です。2位の建設業と比較すると12,526件も多くなっています。
また、厚生労働省の「職場のあんぜんサイト」によれば、労働災害の8割にヒューマンファクター(人的要因)が含まれているといわれています。
製造業においてヒューマンエラーの影響は甚大です。自分や同僚の身を守るためにも、組織や個人で対策をする必要があります。
ヒューマンエラーの4つの原因
ヒューマンエラーは主に以下の4つの要因に分類できます。
- 計画・環境・手順の不備
- 知識不足
- スキル不足
- モラル不足
- (参考文献:中京大学 経営システム工学 中城武志教授 1999年『作業管理システムが作業ミスの発生に与える影響』)
以下で、それぞれの原因について詳しく説明していきます。
計画・環境・手順の不備によるヒューマンエラーは組織で防ぐ
【計画・環境・手順の不備の例】
計画不備 |
|
---|---|
環境不備 |
|
手順不備 |
|
計画・環境・手順の不備によりヒューマンエラーが発生している場合、組織で発生防止対策に取り組む必要があります。業務の仕組み全体に関わるため、個人レベルでは対策ができないからです。以下でそれぞれの具体的な解決策を紹介します。
計画不備の解決策
計画不備の具体的なシーンには以下の状況が考えられます。
- 必要な作業工程が抜け落ちている
- 作業時間の見積もりが甘く、作業者に無理な負担がかかっている
このような状況下では、作業者に過剰な負担がかかってしまい、ミスの原因となるでしょう。この場合、作業手順書を見直し、現在定めている標準が適切か検討する必要があります。
新たな標準作業の作成には、現場のベテラン作業者に参加してもらうなど、現場との連携を密にすることがポイントです。これにより実践的な標準を作成し、作業者の標準に対する意識向上や責任感の向上にもつながります。
環境不備の解決策
環境不備の具体例は以下のとおりです。
- 作業スペースが狭く、整理整頓が行き届いていない
- 必要な工具や材料が適切な場所に配置されていない
- 照明が暗く、作業内容が見づらい
- 室温や湿度が適切に管理されておらず、作業に集中しにくい
このような環境下では、作業者の仕事のパフォーマンスが低減します。作業環境としてのあるべき状態(モノの配置やエアコンの温度など)を定め、チェックリストで日常的に点検しましょう。
手順不備の解決策
手順不備とは、具体的に以下のような状態です。
- 標準作業手順書の内容が複雑で分かりにくい
- 作業手順が曖昧で、作業者によって解釈が異なる可能性がある
- 標準作業手順書が存在するものの、最新版に更新されておらず、古い情報に基づいて作業を行ってしまう
手順の不備が生じている場合も作業手順書の見直しが必要です。複雑な作業については手順をシンプルにできないか考えたり、解釈が異なる手順は写真や図を用いたりして解説するなど改善を行いましょう。
知識不足・スキル不足・モラル不足によるヒューマンエラーは個人と組織の双方で防ぐ
【知識不足・スキル不足・モラル不足の状態】
知識不足 | 業務内容や手順などを知らない状態 |
---|---|
スキル不足 | 業務や手順は知っているが経験が浅く業務に慣れていない状態 |
モラル不足 | 作業手順やルールを知っているが守れていない状態 |
知識不足・スキル不足・モラル不足はいずれも人の能力に関係する原因です。これらが原因のヒューマンエラーは組織的な仕組み改善とあわせて、個人の努力による対策が必要です。
とはいえ「個人の努力」と言われても、具体的に自分が何に取り組むべきかがわからないと、対策が難しいです。次の章では、個人レベルで対策ができるように、チェックリスト形式でヒューマンエラーが多い人の特徴と対策を紹介します。
【チェックリスト】ヒューマンエラーが多い人のあるある行動6つ
ここからはヒューマンエラーが多い人の特徴と対策を解説します。
下記チェックリスト内で心当たりのある行動があれば、それはヒューマンエラーの原因となり得ます。ミスを未然に防ぐために、チェックリストで当てはまった項目の対策方法を読んでみてください。
- 【ヒューマンエラーが多い人のあるある行動チェックリスト】
-
- 作業手順書や仕様書を確認・理解せずに作業を始める
- 分からないことがあっても質問を躊躇する
- 作業中に焦ってしまう
- 他のメンバーより作業スピードが遅く、他の人より疲れているように感じる
- 自己流の手順で作業をしてしまう
- ルール守る必要性を感じられない
【①②に当てはまった方】知識不足に起因するヒューマンエラーに注意!
作業手順があいまいなまま仕事をすることはミスの原因です。例えば、部品検査の業務でうろ覚えの手順で検査をしたことで、不良品を出してしまうなどがあります。これは会社に大きな損害を与える可能性があります。
具体的な対策方法としては、以下のものがあります。
- 【知識不足によるヒューマンエラーの対策】
-
- 作業手順書・仕様書を作業中に必ず目に入るところに置いておく
- 作業手順書・仕様書を見ながら必ず指差し確認をする
- 些細な内容でも良いので1日1回は質問するようルール化して実践する
【③④に当てはまった方】スキル不足に起因するヒューマンエラーに注意!
仕事中、やるべきことが多すぎていつも慌ててしまう方は、作業に慣れていない状況だと考えられます。また、他のメンバーより作業スピードが遅かったり、疲れ度合いが高かったりする人も、目の前の作業に慣れておらずいっぱいいっぱいになっている状況なのではないでしょうか。
余裕がない状態で仕事をするとケアレスミスが増え、リコールを発生させてしまったり、労働災害になったりなどの問題を起こしかねません。
これらを防ぐ対策としては、以下のようなものがあります。
- 【スキル不足によるヒューマンエラーの対策】
-
- 各作業に対して上手くできたこと・できなかったことを振り返り改善策をノートにまとめ、反復練習をする
- 作業工程を細かなステップに区切ってシンプルにする
- 何度やっても上手くできないときは先輩にコツをきく
- 1日のうちに休息の時間をとる
【⑤⑥に当てはまった方】モラル不足によるヒューマンエラーに注意!
自己流の作業は事故や不良品発生のもとです。手順書に書かれた手順は、作業者が安全に作業できるように設計されています。自分と周囲の人の身を守るためにも、作業手順は軽視せず守りましょう。
また、ルールが形骸化しているように感じているなら業務改善のチャンスです。守る必要性がないと思ったときは、自分だけルールを破るのではなく、意味のあるルールに変える意識が大事です。
- 【モラル不足によるヒューマンエラーの対策】
-
- なぜそのルールを守る必要があるのか考え、わからない場合は上司に質問する
- 守る必要性を感じないルールがあれば変更や撤廃の提案をする
組織で取り組むヒューマンエラー対策
ここからは組織で取り組むヒューマンエラー対策を紹介します。
知識不足によるヒューマンエラーを組織で防ぐ
若手比率が高いチームなどは知識不足によるヒューマンエラーのリスクが高まります。このような現場では、組織として以下のような対策が有効です。
- 【組織でできる対策】
-
- 作業手順書・仕様書の確認をルール化し、確認完了の報告を義務付ける
- 作業手順書・仕様書の内容がわかりにくくないか見直す
- リーダー層に対して、新人に積極的に声掛けをする仕組みにする
まず、基礎知識の定着のために手順書と仕様書の確認を指示し、確認完了の報告を義務付けるなど、個人に対してルールを設ける対策があります。ただし、ルール化するだけでは解決にはつながらないことが多いです。
メンバーが作業手順書や仕様書を読まなくなる理由として、読んでも内容がわからず確認の意欲が下がっている可能性もあります。この場合、組織としては手順書や仕様書の内容を見直すことも重要です。
また、メンバー同士が質問をしやすい環境を作ることも間接的なヒューマンエラー対策です。年次の近いリーダーポジションの社員が新入社員に積極的に声をかける決まりにするなど、風通しの良い職場環境づくりに努めましょう。
スキル不足によるヒューマンエラーを組織で防ぐ
新しく編成されたチームなど、まだスキルが不足しているメンバーが多い現場では以下のような対策が有効です。
- 【組織としてできる対策】
-
- OJT形式で簡単な業務から徐々に慣れていける教育体制をとる
- デモ環境で作業トレーニングができる機会を多く設ける
同じタイミングで同じ業務を割り当てられた社員であっても、人によって習得スピードは異なります。OJT形式で実際に業務を見学できるようにし、個人の能力に合わせてできる範囲の作業から慣れていくよう教育体制を整えましょう。
人が物事を理解する特性には「視覚優位」と「聴覚優位」の2パターンがあります。人によって、目からの情報と耳からの情報のいずれが理解しやすいかが異なるのです。視覚優位・聴覚優位のいずれの人にも分かりやすいように、手順を図解したマニュアルと動画の両方を用意すると良いでしょう。
また、いくら座学で知識をつけても、作業スキルは数をこなさない限り向上しません。メンバーができるだけたくさん練習ができるように環境を整えることも大切です。
モラル不足によるヒューマンエラーを組織で防ぐ
なかなかルールが浸透しないと感じている現場では、以下のようなことを見直してみましょう。
- 【組織でできる対策】
-
- 日頃からルールを破ったときの危険性を具体的に伝え、実際に事故がおきるシーンを想像できるようにする
- ルールを守らなければ作業ができない仕組みにする
対策のひとつは日頃からKY活動(危険予知活動)を行い、事故の危険性を伝えることです。日常業務に慣れてしまうと、ついルールが軽視されてしまいます。ただし、記事前半でも述べたとおり製造業は労災の多い業界です。各個人の危機感が持続するよう、定期的に研修の機会を設けましょう。
また、従業員へのルール周知を徹底するアプローチがある一方で、そもそもルールを守らざるを得ない環境を作るアプローチがあります。仕組みルールの徹底を周知するとともに、仕組み改善も行いましょう。
例えば、機械のボタンを押すとき、ボタンを押している手の反対の手が機械に巻き込まれる事故が起きている場合、ボタンを両手で押さなければ作動しない装置に変更するなどです。
【新視点】組織で取り組む!仕組みでミスを防ぐアイデア2選
ここからは、組織で取り組むヒューマンエラー防止活動のうち、変わり種アイデアを2つご紹介します。
対策1. 逆転の発想でヒューマンエラーをあえて活用する
「ミスは悪いもの」「エラーは隠すべきもの」という考えが根強く残っている職場に心当たりはありませんか?
この状態では、ミスから学ぶ機会を逃し同じミスを繰り返しかねません。以下はヒューマンエラーをあえて活用したミス防止活動の例です。
- 【ヒューマンエラーをあえて活用するアイデア】
-
- ヒューマンエラーを意図的に起こす訓練を実施する
- 「エラー歓迎週間」を設け、エラーを発見した社員に報奨を与える
- エラー事例を共有し、対策を全員で考えるワークショップを定例開催する
対策2. 「感情工学」の視点からエラーを防ぐ
「感情工学」とは、言語化が難しい人の感情を科学的に分析し、技術に応用する分野です。
製造現場においても感情工学を活用したヒューマンエラー対策が可能です。
従来の製造現場では、作業者の感情や心理状態が考慮されずに業務が設計されているケースがあります。この状態では、ストレスや疲労によるエラーが見過ごされ、重大な事故につながる可能性があります。
ソリューションとしては、下記のような活動に取り組むのがおすすめです。
- 【感情工学活用アイデア】
-
- 作業者の表情認識AIを用いてストレスや疲労度に応じた作業調整を行う
- 香りや音楽を活用し、集中力と注意力を高める感覚刺激型の作業環境をデザインする
- 感情トラッキングアプリを導入し、従業員のメンタルヘルスケアに活用する
【他社はこう解決!】ヒューマンエラー削減の成功事例
最後に、製造業が実践しているヒューマンエラー削減の成功事例をご紹介します。組織としてどのような取り組みができるのか参考にしてみてください。
技術者の勘をデータ化して作業ミスを削減した金属加工メーカーの事例
ある金属加工メーカーでは、これまで経験豊富な技術者の勘に頼った作業を行っていました。そのため新入社員など経験の浅い社員に正確な技術が引き継がれず、習得に時間がかかったり、ヒューマンエラーをはじめとするミスが後を絶ちませんでした。
この問題の解決策として、同社は技術者の勘の見える化に取り組みました。
技術者の勘をデータ化するために、工場の至る所にモニターを設置し、技術者がいつ、どこで、どんな作業をしているかを記録しました。また、加工のコツや作業工程、図面などもデジタル化しました。データ化された技術者のノウハウをいつでも、だれでも確認できるように、各現場にタッチパネルの設置も行いました。
これにより、経験の浅い社員の金属加工ミスが減り、さらに作業時間の短縮にもつながりました。
RPAを導入し事務系ヒューマンエラーを削減した鉄鋼企業の事例
ある鉄鋼企業では、伝票処理のような工場でどうしても発生する「誰でもできるけど、絶対に省けないし、ミスもできない繰り返し作業」の業務に課題を抱えていました。このような業務はストレスがかかるうえ、手作業ではどうしてもミスが発生してしまいます。
そこで同社はRPAの導入により、手作業だった繰り返し作業を自動化しました。これによりミスがなくなり、そのうえ担当者が単純作業から解放されたことで、深く考えたり工夫が必要な業務に注力できるようになりました。
この事例のように、RPAの導入によるヒューマンエラーをなくす取り組みは多くの企業のソリューションになり得ます。しかし、従来のRPAシステムは導入や運用が複雑で、多くの企業にとってハードルが高いものでした。
最近では、より使いやすいRPAが登場しています。これらは直感的な操作が可能で、専門知識がなくても導入できるのが特徴です。こうしたツールの登場により、より多くの企業がRPAのメリットを享受できるようになっています。
ヒューマンエラーを減らすには対策が欠かせない
今回は、製造業でのヒューマンエラーの原因と具体的な対策法をご紹介しました。どれだけ注意しても、ヒューマンエラーを0にすることは難しいものです。
だからこそ、ヒューマンエラーの原因を把握したうえで、個人レベル・組織レベルの双方で対策を実践していくことが重要です。今回ご紹介したミスの特徴と対策を参考にしながら、ヒューマンエラーを未然に防げる組織づくりをしていきましょう。