よく聞く「サプライチェーン」って何?
マネジメントの業務内容も解説
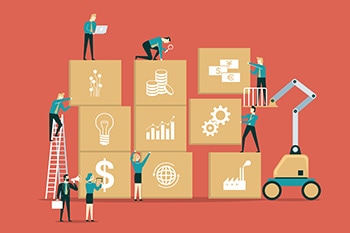
自動車や電子部品、食品など、今や多くの業界でサプライチェーンが構成されています。しかし、サプライチェーンを取り巻く環境は複雑化の一途をたどっており、マネジメント手法を見直す取り組みも始まっています。
今回はよく聞くサプライチェーンの意味や問題点、サプライチェーンマネジメントの業務の流れ、課題解決に取り組んでいる事例などを紹介します。
- この記事でわかること
サプライチェーンとは
サプライチェーンとは、原材料の調達から生産、流通、販売によりエンドユーザーにモノやサービスが届けられる仕組みのことです。日本語で「供給連鎖」と言われるとおり、サプライチェーンは複数の企業から成り立っているもので、それぞれの企業の供給活動がエンドユーザーに向かって連鎖していきます。
たとえば家具は、原材料の調達→木材のカット・組立→配送→販売といった流れでエンドユーザーに届くのが一般的です。この時、それぞれ異なる企業が川下へ向かって製品を供給することでサプライチェーンが成り立ちます。
また、最終製品だけでなく、部品単位でもサプライチェーンは存在しています。つまり、サプライチェーンは重層的に構成されており、製品に関わっている製造業は、どこかのサプライチェーンに属していることになります。
川下へ製品を供給する企業は「サプライヤー」と呼ばれており、自動車産業の場合、サプライヤーの数は数万社にも及びます。個々の企業が専業化すれば生産効率が高まるのがサプライチェーンを構成するメリットです。
サプライチェーンが抱える2つの問題点
前述のとおり、製造に関わる企業は重層的に存在する、どこかのサプライチェーンに属しています。各企業が円滑に事業を進めるために、サプライチェーンはなくてはならないものです。その一方で、サプライチェーンの構造に起因する問題も存在します。
自然災害やパンデミックによる供給遮断
近年、自然災害やパンデミックの影響で工場の操業停止を余儀なくされたり、急激な需要変動が起きたりしたために、企業が減産せざるを得ないケースが起きています。
経済産業省が出した『自動車サプライチェーンの強靱化に向けた取組』では、自動車メーカーの国内生産は、2020年前半のコロナウイルス拡大により大幅に減少したと指摘しています。
中でも半導体不足は世界的な規模で広がりました。
自動車需要が下がると予測した一部の完成車メーカーは、生産台数を縮小させたため、半導体需要が減少しました。ところがその後、自動車需要が急回復したことで半導体の供給が追いつかなくなり、半導体不足が深刻化したのです。ある自動車メーカーは半導体不足により、2022年の生産台数を計画より10万台削減すると発表しました。
横断的な情報開示不足
サプライチェーンを構成する各企業は、本来、自社の利益を追求するものであるため、企業間で情報開示が不十分になりやすいと言えます。
在庫状況や今後の生産計画などが十分に開示されないと、サプライヤーは「どのぐらい供給してもらえるか」「どのぐらいの需要があるか」といった見通しが立ちません。したがってサプライチェーンの問題点として、川下から川上にいくほど需要変動が大きくなるブルウィップ効果が起きやすいことがよく指摘されます。
東日本大震災が起きた際にその問題点は顕著に現れました。地震発生直後に食品の買い占めが起きたことで小売業者が普段の何倍もの発注をかけます。それにあわせて卸業者も大量に発注し、メーカーもこれに応じて増産しましたが、商品が小売店に行き渡るころには買い占めが落ち着き、過剰在庫になったのです。
このような問題を防ぐために、これまで部門ごと、企業ごとに行っていたマネジメント業務をサプライチェーン全体にまで広げるサプライチェーンマネジメント(SCM)が重要視されています。
サプライチェーンマネジメント(SCM)とは
サプライチェーンを語る上で避けては通れないのが「サプライチェーンマネジメント(SCM)」です。
SCMとは、原材料のサプライヤーから消費者にいたるまでのサプライチェーン全体をマネジメントすることです。各企業が連携して、個別最適ではなく全体最適を図る手法です。
SCMはサプライチェーン全体を対象としているものであり、個々の企業を見ていくとそのマネジメントはPDCAに分かれています。PDCAは「計画」「実行」「監視」「制御」です。「計画」段階では需要をもとに生産計画を立案、「実行」段階では計画をもとに実際に製造します。
製造の実績を収集して計画とのギャップを「監視」し、そのギャップを是正するのが「制御」となります。
なぜ、サプライチェーンマネジメント(SCM)が必要か?
SCMの効果としては在庫削減やリードタイム短縮、納期遵守率の向上などがよく挙げられます。しかし、これらの効果は企業によって異なるものであり、すべての企業に当てはまるものではありません。
より普遍的な視点からSCMの必要性を考えると、それは「調達、生産、販売活動を通じて最大限の利益を生み出す」ことだと言えるでしょう。企業は利益を効率よく生み出すために、適切な投資をし、無駄のない調達や生産が求められます。
そのためにSCMが必要であり、さらに言えば前述の供給遮断リスクを抑えるという役割もあります。
サプライチェーンマネジメントの事例
SCMを具体的にイメージしてもらえるよう、ここでは実際の事例について紹介します。前段でお伝えした通り、サプライチェーンは重層的に存在しています。中小企業が取り組んだ事例、最終製品メーカーが先導してSCM改革を実施した事例、業界全体で実施した事例です。
中小企業が取り組んだSCM
中小企業の中には、「調達リードタイムが長い」「需要変動が大きい」などの理由により、親企業の内示に十分な対応ができないケースもあるでしょう。
天然素材の自動車部品を扱うある中小企業も、調達の不安定さに課題を抱えていました。そこで、在庫をある程度許容することで生産を止めないという対策を行います。部品サプライヤーには親企業の内示をそのまま流すのではなく、常に均一な数量を調達することで、川上のサプライヤーに対して安定した生産を約束しています。
また、かんばん方式で部品を供給する企業では、日次の生産計画の変更が頻繫にあり、計画立案に時間がかかるという課題がありました。その企業は、自動的に計画を作成する生産スケジューラを導入し、毎日の計画立案にかかる負荷を軽減しています。
大手衣料品メーカーがSCM改革に取り組む
大手衣料品メーカーは、「無駄なものをつくらない、無駄なものを運ばない、無駄なものを売らない」とサプライチェーンの目標を具体的に表し、SCMの改革に取り組んでいます。
同社は、これまでのサプライチェーンでは無駄なものをつくり、運び、売るものになっていたと指摘します。たとえば生産においては、大量生産の影響でリードタイムが長くなるため、顧客の要望にあわせてタイムリーに販売できないという課題がありました。
しかし、化学メーカーなどのサプライヤーと連携を密にすることでリードタイム短縮を実現しています。また生産段階からRFIDタグを全商品に付与し、在庫情報などのサプライチェーンの情報を可視化するという体制も実現させています。
データ共有のプラットフォーム「Catena-X」
ドイツの自動車業界では、サプライチェーンにおけるデータを共有するプラットフォーム「Catena-X」が立ち上がりました。
先述のとおり、自動車業界ではコロナウイルスの拡大により世界的な半導体不足に悩まされ、生産が停止しました。さらにガソリン車からEVに舵を切り、脱炭素化を進めるという大きな転換点でもあります。
そのような状況の中でオープンかつセキュアなデータ連携基盤を確立し、サプライチェーンに参加する企業がコミュニケーションと情報共有を密にするために「Catena-X」が誕生しました。
「Catena-X」ではシステム構築において標準化をしており、企業間でのデータ共有を行いやすくしています。
このようにSCMは規模がさまざまですし、取り扱う活動も戦略や販売活動、ロジスティクスなど多岐にわたりますが、ここからは特に重要な「計画業務」の流れについて紐解いていきます。
サプライチェーンマネジメント(SCM)の計画業務の流れ
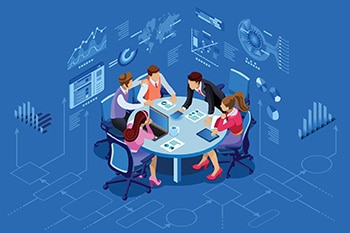
SCMの計画業務は以下のような流れで行います。
- 需要計画
- PSI計画
- 基準日程生産計画
- MRPと仕入
- 工程管理
1. 需要計画
設備や人員の補充、原材料の調達といった活動は準備に時間がかかるものです。したがって計画業務は先々の需要を見通す、需要計画から始めるのが一般的です。需要計画は長期・中期・短期に分かれており、長期需要計画は事業計画の中で作成します。
中期は1年〜2年ほど、短期は3か月ごとを対象として行います。需要計画を作成するためには、需要予測が必要になり、経験や知見をベースに予測する場合と、定量的情報を用いて予測する場合とがあります。
2. PSI計画
PSI計画は生産、販売、在庫の計画を立てたもので、「生販在計画」とも呼ばれます。需要計画で販売数を予測したのち、手持ちの在庫から「どの製品をいくつ生産するか」を決めていきます。
作成自体は、下の図のようになります。基本的には在庫がマイナスにならないように生産数をコントロールする必要があり、現場が持っている生産能力を超えないよう注意が必要です。
第1週 | 第2週 | 第3週 | 第4週 | |
販売 | 5個 | 8個 | 7個 | 10個 |
在庫 期初在庫10 | 10個 | 12個 | 15個 | 10個 |
生産 | 5個 | 10個 | 10個 | 5個 |
3. 基準日程生産計画
MPSと呼ばれる基準日程生産計画は、PSI計画で作成した生産数をもとに、「何を、いつまでに、いくつ作るか」を計画するものです。一般的に製品別、週や日ごとに計算されます。
基準日程生産計画は次のMRPを算出するために必要ですが、在庫の引き当てをするのも基準日程生産計画がもとになります。
4. MRPと仕入
基準日程生産計画をもとに作られる計画がMRPで、資材所要計画とも呼ばれます。MRPは製品を構成する部品の必要量を計算したものであり、具体的には「どの部品が、いくつ、いつまでに必要か」を算出します。
MRPは基幹システムで自動的に計算されるもので、この結果をもとにして調達部門が資材や部品の発注をかけます。
5. 工程管理
工程管理では、これまでに行った基準日程生産計画やMRPをもとに作成された製造オーダーを実行に移します。基準日程生産計画では週や日ごとにしか計画していませんでしたが、この段階ではさらに詳細な計画を作成していきます。
納期を遵守するために工程管理は欠かせないもので、生産効率を高く維持することを目的にヒト・モノ・資源を有効活用できるように最適な生産計画を立案することが大切です。
サプライチェーン強靭化への取り組みで必要なもの
サプライチェーンを強靭化するために、一企業ができることは何でしょうか。
経済産業省の『自動車サプライチェーンの強靱化に向けた取組』では、計画業務から改善するアプローチを示しています。
その中ではサプライヤーに最低でも6か月先の生産計画を提示し毎月更新する、生産計画の粒度は品番レベルなどの詳細なものにする、といった生産計画の提示方法を改善する取り組みで一定の効果を挙げたとしています。
また、サプライヤーからの情報開示が不十分なことがサプライチェーンの課題でもあるため、「Catena-X」のような横断的なデータ連携基盤が必要になるでしょう。
サプライチェーンを理解してSCM最適化を図ろう
現代のモノづくりにおいてサプライチェーンは欠かせないものであり、今や世界規模で広がっています。
サプライチェーンは構造的な問題を抱えているため、分断のリスクを防ぎ、最適化を図るための手法がSCMです。特に計画業務が重要な位置を占めており、サプライヤーや取引先と情報共有を進めながらサプライチェーンを強化するのが大切です。