チーズの穴は事故のもと!?
トラブルは「スイスチーズモデル」で防ぐ

スイスチーズといえば、大小さまざまな穴があいていることが特徴です。穴の発生原因は、発酵時に出てくるガス、もしくは、原材料である牛の乳に含まれた干し草の微粒子など諸説ありますが、チーズの穴は目にたとえられ「チーズアイ」と呼ばれます。
このスイスチーズを安全対策、チーズの穴を脆弱な部分にたとえた考え方があります。ヒューマンエラーがすべての穴を通り抜けると、それは事故・トラブルへと発展してしまいます。現場の安全対策をじっくり見直してみると、貫通していて向こう側まで見えるようなチーズアイ(穴)が潜んでいるかもしれません。今回は、事故・トラブル対策を強化するために有効な「スイスチーズモデル」の考え方や、製造業の現場における例を紹介。また、穴を見つけるために活用できる方法論などについても解説します。
- この記事でわかること
スイスチーズモデルとは
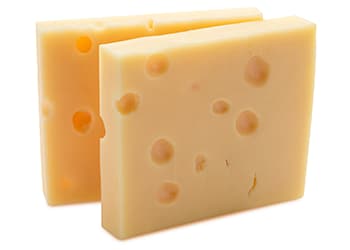
スイスチーズモデルとは、イギリスの心理学者ジェームズ・リーズンが提唱した、ヒューマンエラーから事故・トラブルに至るモデルのことです。事故は単独で発生するわけではなく、複数の事象が連鎖して発生するという考え方です。
事故やトラブルが想定される事象に対して、いくつかの「防護壁(エラーを防ぐ要素)」を設けます。通常、この防護壁を何枚も重ねて立てることによって事故を防止します。しかし、これらの防護壁の脆弱な部分や連鎖的なエラーといった「穴」を次々に通過してしまうと、事故・トラブルに至ります。
このように防護壁に穴があいていることをスライスしたスイスチーズの姿にたとえ、「スイスチーズモデル(Swiss cheese model)」として提唱されました。
製造業の現場におけるスイスチーズモデルの考え方
スイスチーズモデルは、工場はもちろん、医療現場や建設現場などエラーの回避と安全性が求められる場において、広く用いられている考え方です。
製造現場におけるスイスチーズモデルとは
製造業の現場においてスイスチーズモデルを考えるとき、一片のチーズにあたる防護壁は、ヒューマンエラーや事故・トラブルの発生を防止するための物理的な設備や手順の取り決めなど、あらゆる安全対策に相当します。たとえば、安全柵や安全対策機器、装置・設備側への配慮(機械安全)、作業環境などを使った物理的な対策はもちろん、人や作業手順での対策、また、安全に関する組織的な取り組みも防護壁といえます。

- A
- ヒューマンエラー
- B
- 防御壁(エラーを防ぐ要素)=スイスチーズ
- C
- 事故・トラブル
製造現場におけるスイスチーズの穴・エラーの例
加工装置での事故を防止するためのスイスチーズモデルの例を挙げます。
ここでは、防御壁(チーズ)とエラーが通過する可能性(穴)を仮定し、さらに、その穴を補うための2枚目のチーズまでを想定します。実際には、2枚目のチーズの穴を防ぐために次のチーズを設け、エラーを可能な限り防ぐことができるよう、これを繰り返します。
- ・基本的な安全対策として設けた1枚目のチーズ
- 【チーズ】加工装置やその周囲に安全対策装置を取り付けた
- ↓
- 【穴】メンテナンス時に制御装置の設定を変えたままだった / 段取り替え時に不適切な配置になってしまった / 電源を入れ忘れた / 配線を誤って抜き、間違えて接続した
- ・1枚目のチーズを通過したエラーを食い止めるための2枚目のチーズ
- 【チーズ】安全装置が正しく作動するようチェックシートを作成した。
- ↓
- 【穴】新規チェックシートの存在を知らない人がいた / 緊急の段取り替えにチェックを省略してしまった / チェック項目に漏れがあった / チェックシートに誤った、または誤解を与える記載があった
このように、スイスチーズモデルにおいて重要なことは、チーズ(防御壁)が完璧であると過信することなく、考えうる限りの穴(エラーの可能性)に目を向けることです。さらに、それらの穴を補うためのチーズを重ねていくことが大切です。
次は、どのようにしてチーズの穴を見極めるかについて考察してみましょう。
現場のスイスチーズの穴を見極める方法
スイスチーズの抜け穴を見極めるには、まず、さまざまな視点や条件を当てはめることが重要となります。事故・トラブルに繋がる要素を整理したり見極めたりする際に役立つ考え方や切り口の例を以下に挙げます。
4M・5M・5M+1E・6Mなどの切り口
工場であれば、4M(Man:人 / Machine:機械 / Material:材料 / Method:方法)やMeasurement(検査・測定)を付加した5M、さらに、Environment(環境)を加えた5M+1E、または、Management(マネジメント・管理)を付加した6Mなど多角的な観点から検討することが大切です。
ヒヤリハットの想定や、事故・トラブル事例からの逆算
これまでのポカミスやヒヤリハットの記録があれば、類似したパターンを当てはめることもできます。たとえば、1件の重大事故の背景に29件の軽微な事故、さらにその背後には300件ものヒヤリハットが隠れているという「ハインリッヒの法則」の考え方をベースにすることも有効です。さまざまなヒヤリハットがどのように事故・トラブルに発展するか、また、事故を起源として起こり得るヒューマンエラーを逆算し、それらへの対策を積み上げていくことも、スイスチーズの穴への気づきに役立ちます。
ロジカルシンキングの手法を活用する
製造業の現場、工程、装置はそれぞれ複雑な要素からできています。各事象に関する重要項目を重複や漏れがないよう、論理的思考でピックアップする「MECE」の考え方を活用し、ロジカルに検討項目を整理することも効率的です。
このように、さまざまな手法や考え方を掛け合わせることによって、安全対策の脆弱性を洗いだし、質の高いチーズ(エラー対策)を組み合わせていくことで、現場の安全性をより一層強化していくことができます。
- 関連ページ