タービンブレードの寸法測定

タービンの動作精度はエネルギーの変換効率に直結します。タービンには動力源によって水力タービン・蒸気タービン・ガスタービン・風力タービンなどがあり、このうちガスタービンは発電機や航空機のジェットエンジンに使用されており、エネルギー変換の高効率化が求められています。
ここではガスタービンの重要部品であるタービンブレードの寸法や形状測定について、その必要性と重要な測定ポイント、測定を効率化する方法について説明します。
タービンブレードとは

ガスタービンのタービンブレードは、燃料の燃焼によって得られた高温高圧流体の流れを受け止め、回転する動翼列として機能します。
発電機の場合は、流体を整流する静翼列であるステータで流体の流れを整えながら、軸方向に高温高圧流体をタービンブレードに吹き付けてローターを回し、回転の動力を取り出しています。エネルギー変換効率が高く、ガスタービンを利用した「ガスタービン・コンバインドサイクル(GTCC)」は、CO2やNOxなどの排出量が石炭火力などに比べて約50%も少なく、燃料に石油を使わず発電効率も高い方式で新規火力発電設備の主流となっています。
一方、航空機のジェットエンジンではローターを回さず、ノズルから噴射するエネルギーをそのまま推力として使います。この原理で動作するエンジンを「ターボジェットエンジン」といい、ターボジェットエンジンのエネルギー変換効率をさらに高めたエンジンを「ターボファンエンジン」といいます。
タービンブレードの寸法測定の必要性
高温高圧下で高速回転するタービンブレードの耐久性は、材質はもちろん形状・寸法精度に大きく依存します。中でも寸法精度はローターの回転精度に影響し、寸法誤差は軸受やそのほかの部品に大きなダメージを与える偏心回転の原因になります。
タービンブレードには、鍛造加工と切削加工で製造する鍛造翼と、角材を切削加工して製造する角材削り出し翼の2種類があります。このうち、直径が3mを超えるような大型のタービンブレードは鍛造と切削加工の両方を用いて製造します。このとき、鍛造では冷却時の体積収縮や湯流れ不良による形状不良が発生し、切削加工では切削面のむしれやバリといった欠陥が発生します。
また、メンテナンス時にタービンブレードを交換した場合、組み付け精度が低いと重大な事故の原因になります。このため、加工時・メンテナンス時には、以下の点に注意し寸法や形状を測定する必要があります。
加工時
タービンブレードの翼振動を低減させるために装着しているレーシングワイヤーを通す孔の径や高さが設計公差を逸脱していると、レーシングワイヤーが傾きます。レーシングワイヤーが傾いていると、植込部の応力が増大し、タービンブレードに亀裂が発生する原因になります。また、タービンブレードの植込部の寸法精度に問題があると、運転による遠心力でタービンブレードが破裂・飛散する恐れがあります。特に植込部がファーツリー構造である場合、寸法形状は強度に直結します。
メンテナンス時
タービンブレードを交換時にレーシングワイヤーの取り付け状態や止端部形状に異常があったり、植込部を変形させて面当たりの状態が変わると、タービンブレードに亀裂が発生することがあります。また、タービンブレードを再利用する場合、各部の腐食により取り付け精度が低下すると、シャフトが偏心してベアリング(軸受)が破損する可能性があります。特に植込部は、運転に伴う熱・排気圧力および遠心力による応力を受けるため、塑性変形が発生する可能性が高いので寸法測定による検査は欠かせません。
タービンブレードの検査や試験の方法はJIS・ISO・ANSI・ASMEなどの規格で厳格に定められており、各規格において各部の寸法測定も欠かせない項目とされています。航空機のジェットエンジンは、国連機関であるICAO(国際民間航空機関)が定める認証制度に合格しなければ製品化することはもちろん、現存する航空機でも飛行運用が許可されないという国際制度になっており、航空機用のガスタービンもこれに含まれています。一方、発電用ガスタービンには、ジェットエンジンのように広範な国際標準制度はありませんが、試験法や性能評価法を定めた規格があります。
タービンブレードの寸法測定
タービンブレードの形状や芯だしは、最適なブレード位置と空力動作を保証するために厳しい公差が適用されます。一般にタービンブレードは自由曲面で構成されており、高度な測定技術が求められます。
寸法測定のポイント
タービンブレードは三次元形状であるため測定ポイントも数多く、そのすべてが重要です。その中でも最も重要とされるタービンブレードの直径とブレードの形状・組み付け精度・ブレード・芯だしの肉厚の4点に絞って説明します。
タービンブレードの直径とブレードの形状
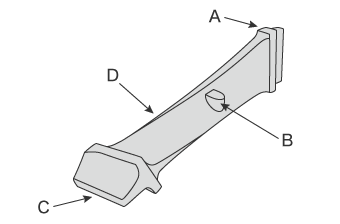
- A
- シュラウド
- B
- スタブ
- C
- 植込部
- D
- 翼面
タービンブレードの直径とブレード、レーシングワイヤーを通す孔の径や高さを測定します。1枚のブレードは、シュラウド・スタブ・植込部で構成されています。このすべての位置や寸法が公差内であることの確認は必要です。特にシュラウドはブレードの先端にあり、回転中のタービンの振動に影響するため寸法を厳しく測定する必要があります。また、シュラウドから植込部に向ってねじれた形状になっており、かつ翼断面が三次元曲面です。このため、面全体の形状を把握するには多くの点を測定しなければならず時間を要するため、高精度かつ効率的な測定が求められます。
組み付け精度
1台のタービンブレードに取り付けられるブレードは、火力発電機の場合、1000枚を超えます。これが正確に回転するには、1枚のブレードの寸法精度だけでなく、ブレードとブレードの間隔や植込部の状態、レーシングワイヤーの取り付け状態や止端部形状などの組み付け精度も重要な測定ポイントです。特にタービンブレードとそれを格納する翼環のクリアランスは、直径が数メートルのタービンブレードでも数ミリと狭いため厳しい寸法測定が必要です。通常、クリアランスの測定にはシックネスゲージを用いることが多く、各測定箇所において、すきま幅が寸法公差に収まっているかを、該当サイズのシックネスゲージを通すことによって確認していくことが求められます。
ブレードの肉厚
動作中のタービンブレードはきわめて高い温度になるため、一部のブレードでは内部を冷却材が循環できるよう中空状になっています。この構造のタービンブレードを「中空タービンブレード」といいます。中空タービンブレードのブレードの肉厚に寸法誤差があると、冷却材の循環が不足し冷却効果が低下するため、異常過熱など不測の事態を引き起こす原因になります。このため、ブレードの肉厚測定は最適強度や冷却のバランスを確保するための重要なポイントといえます。また、肉厚はブレード全体を測定しなければ正確な値を得られないため、正確な三次元測定が必要です。さらに3D CADによる設計データとの照合なども欠かせない作業となります。
芯だし(シャフトアライメント)
回転機整備時には、タービンの芯だし(シャフトアライメント)を行います。このとき、シャフトを固定する治具が重力でたわんだり、治具の遊びが測定結果に影響を与える場合があります。また、カップリング表面の荒れや軸のスラスト方向の動きがある場合は、その誤差を考慮した測定が必要です。正しい芯出しの値を得るには、これらの影響を測定者が修正しなければならず、熟練した測定者による緻密な測定が必要とされます。
タービンブレードの寸法測定の課題と解決法
タービンブレードは、完成品はもちろんブレードの組み付け状態など製造中の測定も重要です。また、高温・高圧力で動作するタービンブレードは、反り・うねり・亀裂などのさまざまな欠陥が発生します。このため、使用年月を経たタービンブレードには定期的な分解検査が必要です。しかし、大型のタービンブレードは測定室に運ぶことが困難であるため、加工機の機上測定機能で測定しなければなりません。また、定期的な点検やブレードの交換時の測定はコンベックスやノギスなどで測定します。しかし、高い精度を得るためには同じ箇所を複数回測定するなどの作業が必要で、稼働率への影響を考慮すると効率化が大きな課題とされています。
タービンブレードの外径や細部の測定
通常、直径3mを超す大型のタービンブレードは、2人以上で測定するケースが一般的です。測定箇所が多いことから、作業は長時間におよびます。また、形状が複雑であるため、測定が不可能な箇所もあり、測定可能な箇所の値からの算出値を測定値としています。
たとえば、
- コンベックスではブレードが邪魔で測定できない。
- 旋盤など機械に載せなければ測れない。
- シックネスゲージでは測定値の記録が残らない、個人差がでる。
などといった課題があります。
このようなワークでも、キーエンスの「WMシリーズ」を使って測定した場合は、1人で測定できます。手持ちのワイヤレスプローブを測定したいポイントに当てていくだけの直感的な操作なので、ワークの奥まった部分の測定も容易に行えます。タービンブレードの直径はもちろん、シュラウド・スタブ・植込部などブレード各部の寸法も測定でき、穴ピッチ・位置度・同軸度・平面度などの三次元測定が可能です。また、長尺ノギス・コンベックスなどの測定器具に比べて、測定者によって測定結果がバラつくことなく、定量的な測定が可能です。
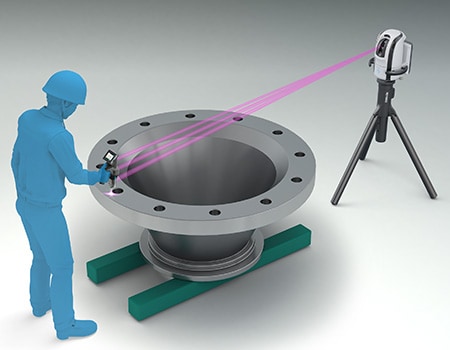
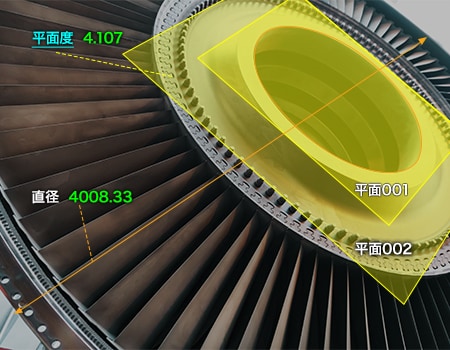
ブレードの組み付け精度の測定
タービンのメンテナンス時の検査では、ブレードなどの各部品をタービンに組み付けた状態で測定する必要があります。さらに、組み付け後のタービンはサイズが大型になり、形状が複雑になる場合が多いことから、コンベックスや長尺ノギスを用いた測定も困難になり、三次元的な寸法が測れる測定機の活用を検討する必要が出てきます。
タービン組み付け後の寸法測定には、現場ですぐに使える利便性と、複雑な三次元形状にも対応可能な汎用性を備えた測定機が必要です。
レーザートラッカーの活用

- A
- 投影部・受光部
- B
- リフレクタ
- C
- 三脚
以上のことから、組み付け後のタービンの寸法測定にはレーザートラッカーが用いられるケースがあります。
レーザートラッカーは、測定対象物に接触させたリフレクタにレーザー光を照射し、リフレクタから反射したレーザー光を発光源に戻すことでターゲットの三次元位置を決定する光学式測定機です。一般的な門型の三次元測定機に比べて、大きな対象物(数m~数十m)を測定することができます。
タービンや飛行機のような大きな測定対象物や大型設備の部品、大型の加工設備で加工された切削品など、巨大な対象物を測定したい場面で活躍します。
ワイドエリア三次元測定機の活用
キーエンスのワイドエリア三次元測定機「WMシリーズ」も、組み付け後のタービンのような大型製品の三次元測定に適した測定機です。まず、「WMシリーズ」は、持ち運びが可能なポータブルタイプなので、測定場所を選びません。また、動作環境温度0~40℃、動作環境湿度20~80%に対応。温度管理された測定室は不要です。これにより、タービンブレードを測定室に持ち込むことなく、現場で高精度な三次元測定が可能です。定期的検査における各部の測定も現場でできるため、タービンの停止時間を短縮することができ稼働率の向上に貢献します。
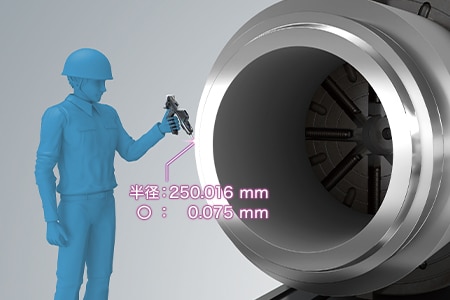

自由曲面の測定
「WMシリーズ」は、複雑な曲面でできているブレードの3D形状を測定することができます。コンベックスや長尺ノギスでは測定が困難な反りやうねりもCADデータと照合し、カラーマップでわかりやすく表示することができます。
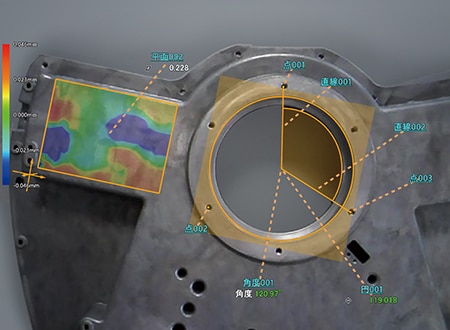
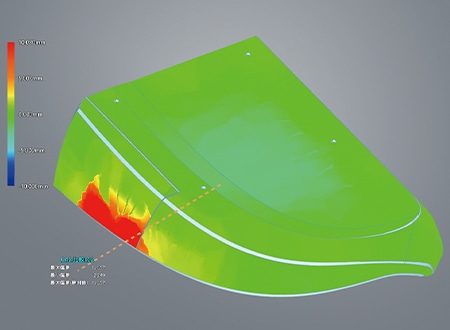
幾何公差や座標位置の測定
幾何公差や座標の測定は、三次元測定機でなければ正確に測定することはできません。
「WMシリーズ」は、円や距離などの基本測定のみならず、中点などの仮想点や平面度などの幾何公差、XYZの座標測定もできます。熟練が必要とされる、ワークを固定する治具の位置座標も簡単に測定することができます。


タービンブレードの寸法測定の効率化
「WMシリーズ」なら、プローブを当てるだけの簡単な操作でタービンブレードの形状を正確に三次元測定可能です。さらに、以下のように多くのメリットがあります。
- 最大25mを高精度に測定可能
- 最大25mの広範囲をワイヤレスプローブで高精度に測定が可能。門型やアーム型の三次元測定機や、長尺ノギスなどのようなハンドツールでは届かないような大型ワークも簡単に測定できます。
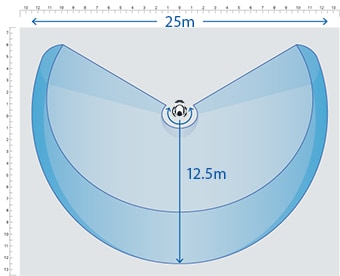
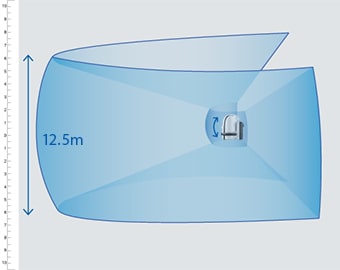

- 大型品の測定が1人で完結する
- 測定したいポイントに、手持ちのワイヤレスプローブを当てるだけの簡単操作なので、大型品の測定も1人でこなすことが可能です。検査コストの大幅な削減を実現します。
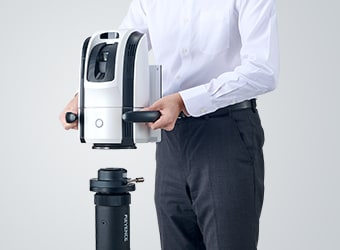
- ポータブルで現場置きが可能
- 本体を台車に入れて、自由に持ち運べるポータブル仕様。測定対象物を動かさなくても、対象物のある場所に持ち込んで測定することが可能です。
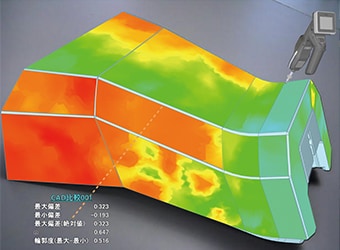
- 3D CADデータと照合ができる
- 3D CADファイルから読み込んだ形状と、測定対象物の形状を比較測定できます。また3D CADデータとの差分をカラーマップ表示することができ、自由曲面・輪郭度の測定にも対応しています。
「WMシリーズ」は、タービンブレード各部の形状測定や組み付け中のブレード位置の測定はもちろん、データ解析や検査レポートの作成までを強力にサポート。タービンブレードの製造から定期点検に欠かせない業務の飛躍的な効率化を実現します。