ダイカストの鋳巣など鋳造不良の原因と測定・評価
自動車部品に多用されるダイカストの採用範囲は、近年さらなる広がりを見せています。そこで鋳物製造の現場で求められるのが、スピーディな計測や定量評価による不良やその原因特定による品質と歩留まり率の向上です。
ここでは、鋳造不良の原因や対策、そして最新の4Kデジタルマイクロスコープを用いたダイカストの最新検査事例を紹介します。
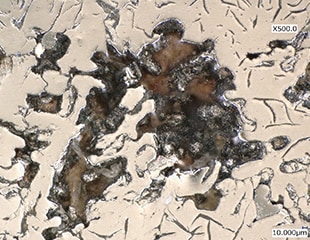
自動車業界での適用範囲が広がるダイカスト
アルミニウム合金・亜鉛合金・マグネシウム合金・銅合金などの溶融金属を精密な金型に圧入する鋳造方式、または鋳造品「ダイカスト」。優れた寸法精度と美麗で滑らかな鋳肌、高い生産性が得られることから、さまざまな製品に用いられています。
ダイカスト製品の生産量全体において、自動車部品が大多数を占めるといわれます。
なかでもアルミニウム合金ダイカストは、亜鉛合金ダイカストよりも軽量で強度も高く、電気・熱伝導性・耐食性・加工性に優れ、低コストでリサイクル性の高い製品が実現することから、自動車部品に多く採用されています。
自動車用途としては、シリンダーブロック・トランスミッションケース・ロッカーカバーなどのケース・カバー類が挙げられます。これまでのダイカスト製品はガスを含有することが多く、熱処理・溶接が難しいため、自動車の足回り部品やボディ部品などへの適用が難しいといわれてきました。しかし、近年は層流ダイカストや高真空ダイカストなど特殊ダイカスト法により、難易度の高い製品への適用も進んでいます。それに伴い、鋳物の機能性と品質の要求レベルも高度化しています。
鋳造不良の原因と対策
自動車部品のダイカスト工程における注意点として、溶融金属や金型の温度、金型充填時の圧力、金属に内包したガスや空気などによる鋳造不良が挙げられます。鋳造不良は、強度低下を招くため、自動車の安全品質に大きく関わります。
鋳物の鋳巣・鋳肌など内部や表面に発生する代表的な欠陥・不良と、その原因や対策を下記の表に示します。
鋳造不良 | 原因・状態 | 対策 |
---|---|---|
鋳巣(いす) | 溶融金属内の空気やガスの混入による穴(巻き込み巣・ブローホール)。溶融金属の供給不足によりできた空洞(引け巣) | 鋳造圧力の調整、ガス抜き穴の変更、離型剤の塗布量の調整、湯口の位置と大きさの変更 |
ヒケ | 金型の部分的な過熱により冷却が遅れ、くぼむ | 金型温度の調整、金型の設計変更 |
充てん不足(湯回り不足) | 湯口部に近いエリアが早く冷却し、キャビティ全体に溶融金属が行き渡らない状態 | 金型温度、溶融金属温度の調整、湯口の位置と大きさの変更 |
コールドシャット(湯境) | 金型温度が低く注入圧力が低い場合、溶融金属が金型内に行き渡る前に凝固し、合流地点で繋ぎ目となった状態 | 金型温度、溶融金属温度およびプランジャー速度を上げる。湯口の位置と大きさの変更 |
割れ・歪み | 抜け勾配不足、不均一な収縮、不適切な押し出しなどによって発生。凝固中の割れは高温割れ、冷却過程や時間経過後は低温割れ | 形状設計や押し出し位置の変更 |
破断チル層 | スリーブ内で発生した凝固層がキャビティ内に注入され、ダイカストに取り込まれた状態 | 溶融金属温度およびプランジャー速度の調整 |
湯じわ | 金型の温度が低い場合や、離型剤の量が多い場合に発生 | 金型の温度を上げ、離型剤の量を減少させる |
かじり | ダイカスト取り出し時に、型に溶着したり、抜け勾配が不適切な場合に傷が発生 | 金型表面を十分に研磨し、適切な抜け勾配を設ける |
焼付き | 金型の部分的な過熱により、金型と溶融金属が溶着した状態 | 離型剤の種類や塗布方法の変更、金型の設計変更 |
ふくれ | 表面近くの圧縮されたガスが膨張し、表面にふくらみが現れた状態 | 鋳巣と同様の対策および金型の冷却時間を長くする |
変色 | 離型剤の成分がダイカスト表面を変色させた状態 | 離型剤の変更 |
肌荒れ | 金型表面の面粗さが、そのままダイカスト表面(鋳肌)に転写されることで発生 | 金型の清掃および研磨 |
ハードスポット | 溶解金属内に硬い異物が混入することで発生。後工程で研削ツールなどの破損原因となる | 溶解金属のフィルタ処理 |
上記の他にも、さまざまな原因による鋳造不良があります。ダイカストにおいて、品質保証に重要となるのが品質検査です。微小な穴や空洞、表面の粗さ不良などは品質に関わるため、精度の高い解析や計測、評価が要求されます。
ダイカスト製品検査の最新事例
鋳巣や鋳肌の評価・不良解析に欠かせない項目の1つが顕微鏡での拡大観察です。しかし、ダイカスト製品は立体的であるため、ピント合わせの手間や観察・解析の難易度、不良評価のバラツキなどが課題となっていました。
そこでデジタルマイクロスコープによる拡大観察が増加しています。最先端の技術を集約した、キーエンスの超高精細4Kデジタルマイクロスコープ「VHXシリーズ」は、ダイカストの鋳巣や鋳肌を鮮明に捉え、評価を定量化すると同時に、作業効率を大幅に向上することに成功しました。
倍率を上げても常時フルフォーカスのズーム撮影
従来の顕微鏡の場合、対象物の大きさや解析箇所により、レンズ交換で倍率を変え、ピント合わせする手間と時間がかかりました。
4Kデジタルマイクロスコープ「VHXシリーズ」なら、高分解能「HRレンズ」と「電動レボルバ」により、レンズ交換なしで20~6000倍まで自動で対応する「シームレスズーム」を実現。手元のマウスやコンソールでの直感的操作で、深度合成による全体にフルフォーカスした高解像度画像による観察のほか、自動面積計測や3D形状・プロファイル測定による定量評価まで、一連の作業が1台でスピーディに完結します。
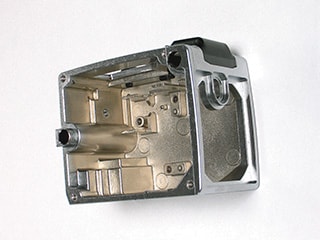
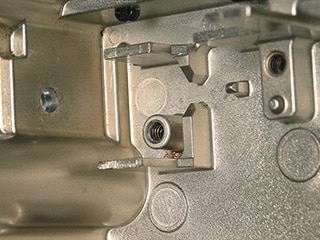
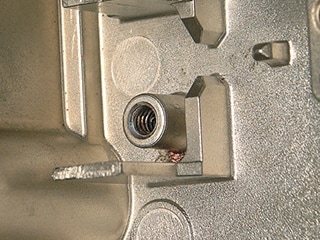
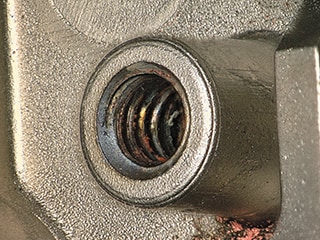
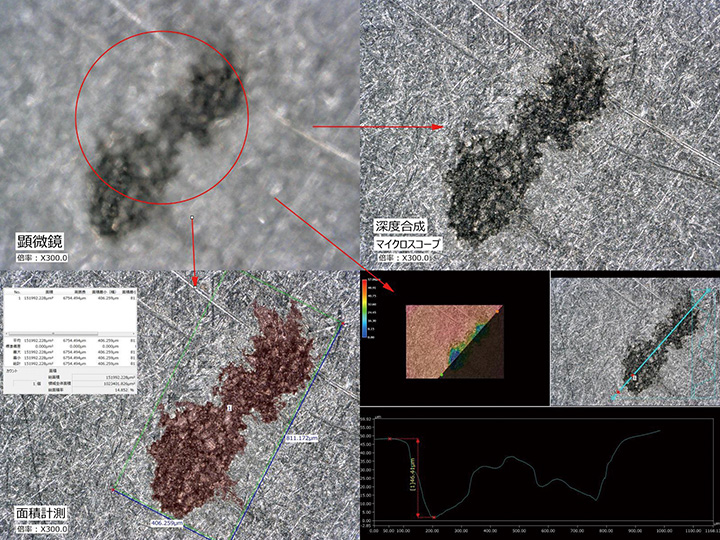
自動面積計測(左下)や3D形状・プロファイル測定(右下)が簡単な操作で実現。
鋳巣の3D形状・プロファイル測定
4Kデジタルマイクロスコープ「VHXシリーズ」は、従来の顕微鏡では取得不可能だった高さ情報による3D形状や、プロファイル(2次元断面形状)の測定が可能です。凹凸のあるダイカスト表面も全体にフルフォーカスした3D表示により、鋳巣・ブローホールなど表面形状の微細な変化も見逃しません。
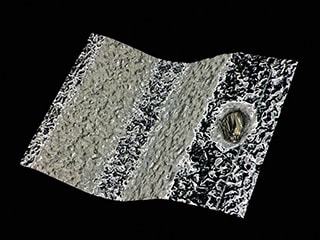
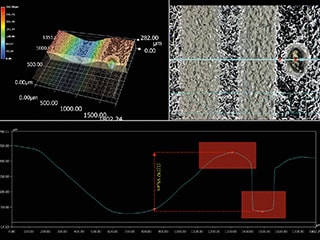
微細な鋳巣の高倍率画像
これまで鋳巣の観察に使用されていた顕微鏡は、倍率・解像度が足りない、ピントが合わないなどの課題がありました。
4Kデジタルマイクロスコープ「VHXシリーズ」であれば、微細な鋳巣も鮮明かつ高倍率で撮影できます。
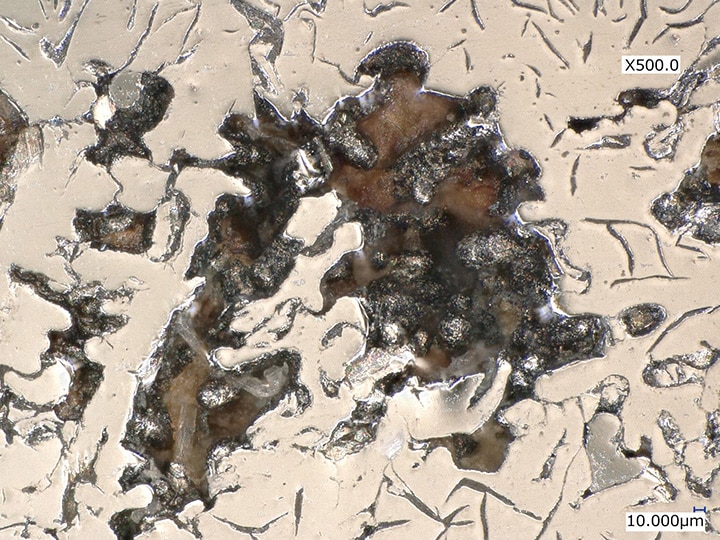
ダイカスト金型の手持ち観察
鋳造不良は、溶融金属の温度や圧力のみならず、金型の状態が原因となることも少なくありません。特に鋳肌表面の荒れなどの不良は、金型内部の微細な外観不良が原因となることが多く、金型の検査も欠かせません。
しかし、自動車部品の鋳物金型は大型である場合が多く、切り出して顕微鏡で観察・解析するわけにはいきません。また、従来の手持ちマイクロスコープによる非破壊検査では、微細なクラックに対して解像度不足が課題でした。
4Kデジタルマイクロスコープ「VHXシリーズ」なら、手持ち用レンズ使用時でも4K画像により金型の微細なクラックなど不良箇所の拡大観察が可能です。
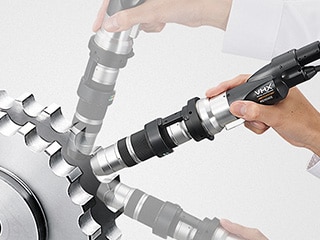
ダイカスト金型クラックの3D形状・プロファイル測定
4Kデジタルマイクロスコープ「VHXシリーズ」は、従来の顕微鏡では不可能だった3D形状・プロファイル測定が実現します。高倍率画像からそのまま効率的かつ定量的な検査が実現すると同時に、使用するレンズによって金型から小さな試料まで多くの解析・検査用途に対応します。
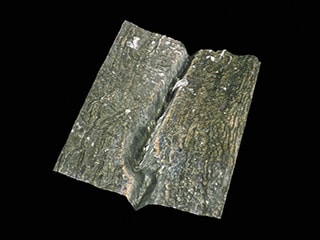
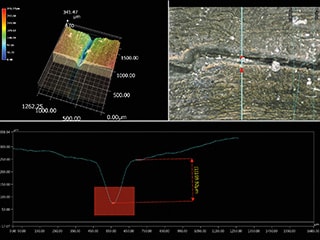
鋳肌表面の自動面積計測と定量評価
4Kデジタルマイクロスコープ「VHXシリーズ」は、立体的な鋳肌表面の2次元検査においても強力なツールとなります。自動面積計測・カウント機能により、簡単な操作で、鋳肌表面の不良箇所を定量評価することができます。
これにより肌荒れなどの不良を見逃すことなく定量評価できるほか、レポート機能を利用することで画像と数値データを用いたレポートを瞬時に作成することができます。一連の作業を1台で完結できるほか、大幅な時短化が実現します。
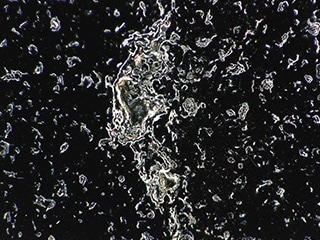
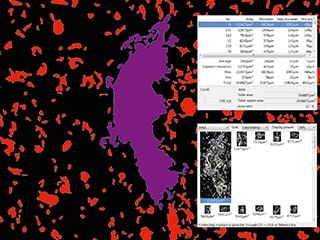
ダイカストの現場を変える1台
高精細4Kデジタルマイクロスコープ「VHXシリーズ」は、高解像度4K画像による鮮明な拡大観察はもちろん、従来の顕微鏡では不可能だった自動計測や2D・3D測定にも1台で対応可能なため、定量評価をスピーディに行うことができます。
「VHXシリーズ」は、ダイカストの現場で課題となる鋳巣や鋳肌荒れなどの詳細な画像と数値が迅速に得られるため、素早い不良原因の特定と不良再発防止に役立てることができます。これにより、ダイカスト製品の用途拡大と機能要求が高まるなか、品質と歩留まり率の向上に欠かせない1台となります。
「VHXシリーズ」に関する詳細は、以下のボタンよりカタログをダウンロード、または、お気軽にご相談・お問い合わせください。