プレス品の不良(バリ・打痕など)の原因と不良箇所や切断面(破断面など)の観察
さまざまな製品の大量生産に広く用いられるプレス加工。特に近年は、自動車の電子制御化が進み、車体や摺動部品のみならず、小型化・高密度化する電装部品や電子機器用の金属部品にもより高い精度や耐久性、信頼性が要求されるようになりました。
ここではプレス加工における代表的な不良とその原因・対策を解説。また、研究開発での試験や設計・試作、品質保証での調査などで重要となる、不良箇所や破断面などの切断面の観察を高度化・効率化する4Kデジタルマイクロスコープの活用事例を紹介します。

プレスで発生する不良や不具合の原因と対策
プレス加工の種類
プレス加工では一般にダイやパンチと呼ばれる金型を用いて材料にさまざまな方法で圧力を加えて、目的の形状に成形します。プレス加工で行われる代表的な加工の種類を以下に挙げます。
- せん断:材料の破壊限界を超えた力を加えることにより加工(切断)します。
- 曲げ:材料の一方に引張力、もう一方に圧縮力を加えることで材料を曲げる加工です。
- 絞り:引張応力によって材料を加工します。
- 圧縮:材料に圧縮力を加えて加工します。
プレス加工での代表的な不良・不具合の原因と対策
プレスでの各種加工で生じる代表的な不良とその原因・対策について解説します。材料の性質や設計、加工原理上、完全に不良や不具合を継続的にゼロにすることが困難なこともありますが、さまざまな対策によって不良が発生する頻度を低減し、可能な限り歩留まり率を向上させることが重要です。
- バリ
-
原因:せん断加工において、パンチとダイの隙間(クリアランス)が大きすぎるなどの理由で発生します。
対策:板厚において1/2~1/3がせん断面となるよう、また、その状態が均一になるようにします。
各クリアランス条件における、せん断加工後の材料断面の構成イメージを下図に示し、各部の名称や特徴などについて解説します。

- ダレ:材料表面が引っ張られることにより、滑らかになった面です。
- せん断面:縦に筋状の模様があり光沢を持つ面。せん断時にパンチの傷や溶着金属と材料の摩擦により細かい傷があります。
- 破断面:せん断面に比べてむしり取られたような粗い表面で、激しい凹凸があります。
- バリ:材料から飛び出した突起で、ギザギザの形状です。このバリが大きいと、部品接合時などのはめあい精度が不足したり、鋭利なバリ先端で怪我をしたりなど安全面の問題が生じ、製品不良につながります。
- 板厚
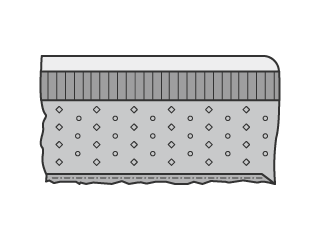
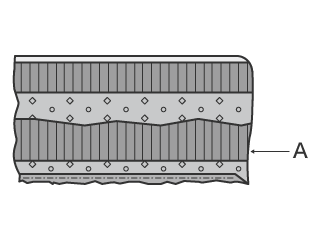
クリアランスが適正より大きければ大きいほどバリが大きくなります。また、抜き圧力による反り(抜きゾリ)が生じるなど、形状・寸法の精度が低下します。一方、クリアランスが過小であった場合、破断面を挟んで2次せん断面(右図中A)ができ、ヒゲ状のバリが生じます。
バリは金属材料のプレス加工においてカエリとも呼ばれ、そのサイズは、カエリの根元厚み(図中A)やカエリの高さ(図中B)で表されます。
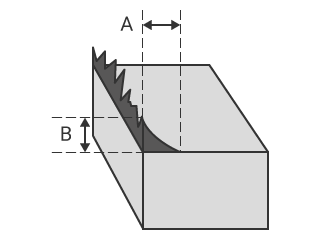
- スプリングバック
-
原因:曲げ加工の後、材料内部に残留した圧縮応力と引張応力で材料が反発して、加工部の曲げ角度が開きます。
対策:目的の角度よりも深い角度で曲げるオーバーベントを施すほか、パンチにストライキングを設けたり、ノッチ状の溝を打っておいたりすることにより防止します。
- シワ
-
原因:絞り加工において、フランジ部分に圧縮力が加わることによって生じます。
対策:絞り条件により「しわ押さえ」を利用し、材料にかかる負荷を均一にします。しわ押さえには固定式のほか、スプリングやダイクッションの力を利用する可動式もあります。
- 割れ
-
原因:絞り加工において引張力が破壊限界を超えた際、材料に割れが発生します。
また、曲げ加工においても材料の圧延方向や曲げ幅寸法によって、曲げ部分にクラック(ひび割れ)や割れ目・裂け目が生じます。
対策:絞り加工では、しわ押さえの圧力を低くしたり、ダイのR形状を滑らかにして変形抵抗を小さくしたりなどの対策があります。曲げ加工では、曲げ線と材料の圧延方向が直角になるよう配置したり、曲げ幅を板厚の8倍以上設けたりなどの対策があります。
- カス上がり(打痕・傷などの原因)
-
原因:抜き加工後、本来は離型すべきスクラップ(抜きカス)が、真空圧や油膜、磁気などによってパンチに付着してしまう現象です。カス上がりは、材料の表面に打痕や傷などの不良が生じる原因となります。同時に、金型がダメージを受けてしまうケースもあります。
対策:パンチに「キックピン(キッカーピン)」を搭載し、スクラップとパンチの間に物理的な隙間を設けるという対策があります。他に、パンチの先端からエアを放出したり、パンチに溝を切ってそこにエアを入れたり、また、下方からスクラップを吸引したりといった方法もあります。ほかに、使用する油の粘度を下げたり、パンチに溝を設けて油の接触面積を減らしたりすることにより、スクラップの吸着を低減することができます。
プレス品の切断面や不良箇所の観察事例
生産現場での努力だけでは、プレス加工における不良を回避することが困難な場合があります。研究開発や材料選定、製品および金型の設計など、可能な限り初期の段階で試験や試作を繰り返し、改善しておく必要があります。また、品質保証においてもプレスで生産された金属部品の故障原因の究明と改善は重要です。
そのため、これらの段階で欠かすことができないのが、顕微鏡による不良箇所の詳しい観察です。
たとえば、せん断加工では切断面から加工条件が適切かどうか、バリの発生原因になっていないかなども詳しく調べることができます。一方で、金属加工品は立体的であるため全体にピントを合わせたり、視野内で表面の粗さや反射率が異なるなど、観察の難易度が高いことが課題でした。
ここでは、4Kデジタルマイクロスコープ「VHXシリーズ」を使ったプレス品の断面からダレやせん断面、破断面などの表面の微妙な違いやバリ・打痕などの不良箇所の外観を高精細に観察する事例をメリットとともに紹介します。
プレス品断面(ダレ・せん断面・破断面)の高精細観察
せん断加工したプレス品の断面では、板厚に対するせん断面の割合によって、パンチとダイのクリアランスが適正かどうかなど加工品質やバリの発生要因などを評価することができます。断面に表れるダレやせん断面、破断面はそれぞれ凹凸や粗さ、模様など表面状態が異なります。さらに各部が同色で低コントラストでありながら、光の反射率が異なるため、ある部分にハレーションが生じるなど、全体の表面状態を観察することが困難でした。
4Kデジタルマイクロスコープ「VHXシリーズ」は、高分解能と深い被写界深度を両立したテレセントリックHRレンズや4K CMOSなどを搭載し、クラス最高の分解能と解像度を実現しました。それにより、さまざまな表面状態が同居する断面全体にピントが合った鮮明な画像を取得することができます。
また、専用設計の光学系や4K CMOS、照明を組み合わせた新しい観察方法「Opt-SEM(Optical Shadow Effect
Mode)」では、多方向からの照明で撮影した変位(コントラスト)を解析します。それにより、微小な凹凸などの表面状態を高いコントラストで鮮明に観察することができます。さらに、Opt-SEM画像にカラー情報を合成して凹凸(深さ・高さ)情報を色分け表示して可視化が可能です。
「VHXシリーズ」は、このような先進的な観察方法を簡単な操作で実現できるため、従来は条件出しに多くの時間を要した断面の観察・評価のスピードを飛躍的に向上します。

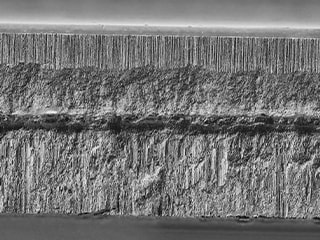
左:リング照明(×100)/右:リング照明+Opt-SEM(×100)
微細なバリのフルフォーカス観察
プレス品に生じたバリは、微小であっても硬質で鋭利であれば、製品の安全面を損ねる原因となります。また、部品の組み付け時にバリが引っ掛かるなど、生産の歩留まりにも影響しかねない不良です。
しかし、一般的な顕微鏡で立体的かつ微細なバリを観察する場合、一部にしかピントが合わず、発生原因の究明において重要な情報となるバリの根元と先端を全体像で同時かつ鮮明に観察することが困難でした。
4Kデジタルマイクロスコープ「VHXシリーズ」は、最先端の光学技術と独自の観察システムにより、立体的な対象物も全体にフルフォーカスした画像を簡単に取得して観察することができます。
高解像度かつ深い被写界深度を実現したレンズや4K
CMOS、リング照明を活用することにより、ヒゲ状にのびたバリであっても根元から先端まで全体にピントが合った、4K高精細画像で観察可能です。
不良箇所の全体像を高精細に捉えた画像で一望できるため、観察による原因究明のワークフローを大幅に効率化することができます。
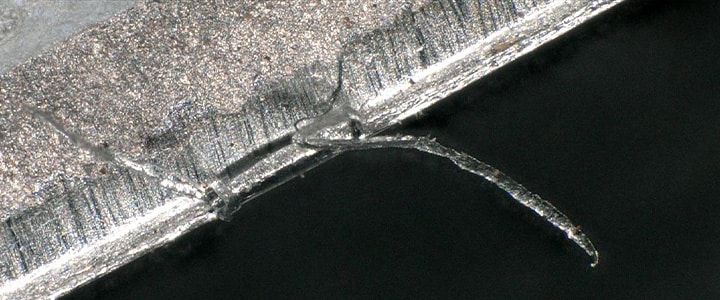
打痕など微細な不良箇所の高コントラスト観察
カス上がりなどによって生じる緩やかな打痕や微細な傷などは、金属材料表面において背景とのコントラストが低いため、条件出しの難易度が高く、時間をかけて調節してもうまく観察できないケースがあります。
4Kデジタルマイクロスコープ「VHXシリーズ」は、手動での条件出しが不要です。ボタンを押すだけで、全方位の照明データを自動取得する「マルチライティング機能」により、観察目的に最適な画像を選択することができます。画像を選択した後でも、他の照明条件の画像も自動保存されているため、サンプルを再びセットすることなく、異なる条件で観察することも可能です。
また、SEM(走査電子顕微鏡)に迫る画像を、真空引きなどの手間なく容易に取得することができる新しい観察方法「Opt-SEM(Optical Shadow Effect Mode)」を活用することにより、微細な打痕も高いコントラストで鮮明に観察することが可能となります。
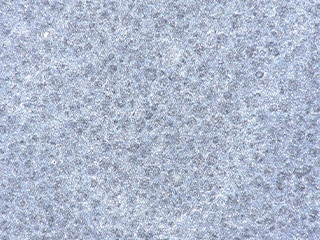

左:リング照明(×150)/右:リング照明+Opt-SEM(×50)
プレス品の研究開発や設計、品質保証を大幅に効率化する4Kマイクロスコープ
4Kデジタルマイクロスコープ「VHXシリーズ」なら、従来はプレス品が持つ金属材料特有の光沢などにより、難易度が高く熟練者であっても条件出しに多くの時間と手間を要した、断面や微細な不良箇所の観察を容易な操作でスピーディに実行することができます。
多彩な機能を用いた4K高精細画像により、研究開発や製品・金型の設計や改善、製品故障時の品質保証に欠かせない観察の高度化・効率化を実現します。
「VHXシリーズ」に関する詳細は、以下のボタンよりカタログをダウンロード、または、お気軽にご相談・お問い合わせください。