自動車・航空関連業界
焼結部品のデジタルマイクロスコープでの観察・測定
焼結部品は、粉末状の金属やセラミックの粉を金型で成形し、融点より低い温度で焼き固めたものです。金属を溶かす必要がないため、省エネで材料ロスも少なく、二次加工の手間もかからないメリットがあります。ここでは、焼結加工の概要と、焼結部品のデジタルマイクロスコープでの観察・測定事例を紹介します。

焼結加工のメリット・デメリット
焼結加工は材料を溶かす必要がないため、さまざまな部品の製造に活用されています。
- 焼結加工のメリット
-
- 粉末にできれば、ほとんどの材料が利用可能
- 二次加工の必要性が低い
- 材料のロスが少ない
- 複雑な形状に成形可能
- 材料の配合が自由
- 気孔を含むため、軽量化が可能
- 高融点の材料も加工可能
- 焼結加工のデメリット
-
- 粉末に加工するため、材料費が高い
- 焼結の際に収縮が発生する
- 鋳造やプレスに比較し、強度などの機械的性質が劣る
焼結加工の原理
固体粉末の表面は、原子・分子・イオンが結合していないため不安定な状態です。固体粉末を加熱すると、ネックと呼ばれる結合部が形成されます。粉末粒子の表面から原子・分子・イオンがネックへ移動拡散してネックが大きくなり、表面積が減少します。焼結の初期、中期、終期とネックが大きくなり、密度が上昇し焼結品が完成します。


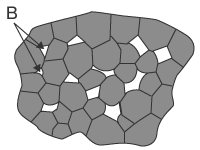

- A:ネック
- B:開気孔
- C:閉気孔
外気と接続している気孔を開気孔、物体内部に孤立している気孔を閉気孔と呼びます。
焼結加工の流れ
- 原料粉の配合を決め、混合機で均一になるよう混ぜ合わせます。
- 混合した原料粉を金型に入れ、プレス機で成形します。
- 成形品を焼結炉で数時間加熱します。
融点より低い温度で焼き固めるため、原料粉が溶けることはありません。長時間加熱することで、原料粉が強く結合し、焼結品が完成します。
焼結炉はガスで満たされているため、焼結品の酸化が防止できます。
焼結品は、必要に応じて、精度を高めるための研削・研磨、硬度を高めるための熱処理を行う場合もあります。
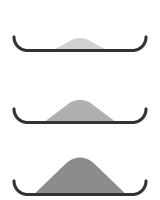
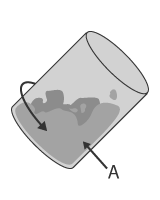
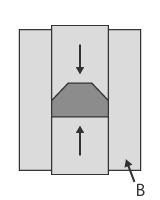
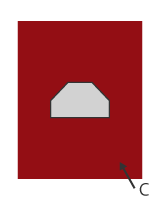

- A:混合機
- B:プレス機
- C:焼結炉
デジタルマイクロスコープによる焼結部品の観察・測定事例
キーエンスの4Kデジタルマイクロスコープ「VHXシリーズ」を用いた焼結部品の観察・測定の最新事例を紹介します。
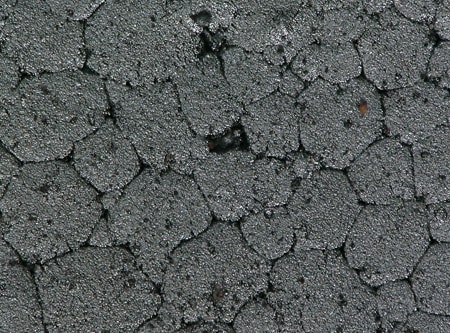
粒界密度小(強度が弱い)

粒界密度大(強度が強い)

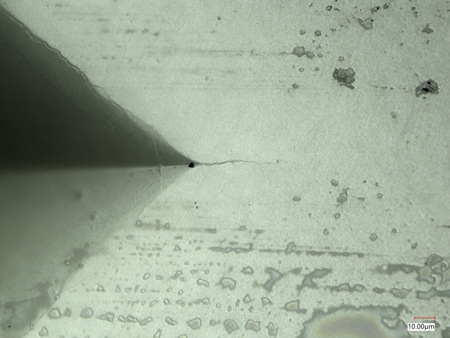

左:アタッチメント有リ 右:アタッチメント無し
可変照明アタッチメントを使用することで、気孔が明瞭に観察できます。

従来は、SEMで結晶粒度を目視カウントしていましたが、自動面積計測機能を使用することで、自動カウントが実現できました。
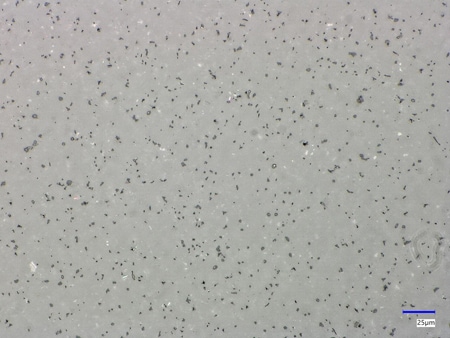
計測前

自動面積計測画像
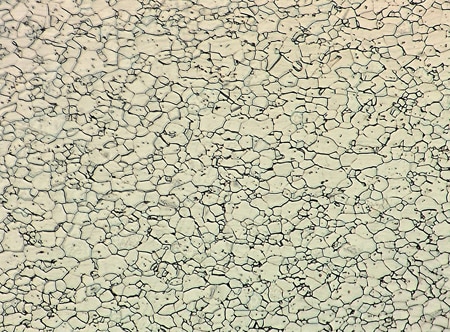
計測前

自動面積計測(結晶粒度解析)画像
自動面積計測機能で粒度解析することで、解析が正確になり大幅な工数削減が実現します。