溶接部の溶け込み不良と測定・検査の効率化
自動車・航空機などの金属接合工程で多用される「溶接」。製品の安全性に関わる溶接部は、溶け込みの寸法が適正かを断面試料で測定し、溶け込み不足・融合不良などを検査することで、品質を保証することができます。
最新の4Kデジタルマイクロスコープは、低コントラストな溶接部断面も、金属組織の境界や不良箇所を鮮明に表現します。また、2次元・3次元寸法測定を素早く実行し、測定結果(画像や数値など)を自動でレポート化可能なため作業を飛躍的に効率化します。
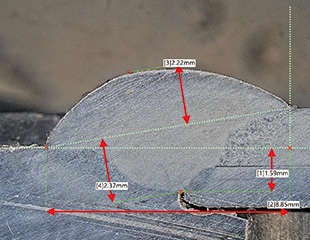
溶接の溶け込み検査の重要性
自動車や航空機、鉄道車両、船舶などの金属製構成部品の接合には、溶接が多用されています。自動車であれば、ボディーやフレームをはじめ、エンジンやトランスミッション、シャシなどの構成部品、つまり、走行により応力が伴う箇所には、主に各種アーク溶接や抵抗スポット溶接、レーザー溶接などによる接合が多く採用されています。そこで重要となるのが、溶接部の強度設計と、断面の寸法測定による溶接品質の検査です。
溶接部の機械的特性と破壊
母材はもちろん、それを接合する溶接部(溶接ビード・溶け込み)も、溶加材(溶接棒・溶接ワイヤーなど)が溶融・凝固した金属材料です。
代表的なアーク溶接などにおいて、溶接金属はもちろん、溶接熱の影響を受けた母材の熱影響部でも金属組織は連続的に変化します。それに伴い金属材料の機械的特性も連続的に変化します。一方で、溶接ビード表面に形成される「余盛り」は、不連続性を持っています。不連続性が集中した場合、機械的特性にも偏りが生じるため、応力集中による破壊の原因となります。
強度設計と溶接品質
一般に、金属製品の強度設計では、製品に加わる荷重を想定し、各金属部材に作用する荷重を求め、材料を選定します。また、各部材の溶接部に作用する荷重からも強度設計が求められ、それに準じた溶接品質を実現する必要があります。
そのため、溶接後の溶接ビード断面の大きさ「のど厚(のど断面)」や「脚長」、「溶け込み深さ」などを測定することで、強度設計に基づく溶接品質を検査することが重要です。溶接部の品質は、溶接後の断面をマクロ的に測定することで評価することができます。
溶け込みによる溶接品質
溶け込み深さと溶け込み不良
溶け込み深さは、接合強度と大きく関係しています。溶接部に溶け込みの深さや母材との関係などが適切ではない「溶け込み不良」がある場合、溶接の品質と強度を大きく損ねてしまいます。突合せ溶接を例に、代表的な「溶け込み不良」を下記に挙げます。
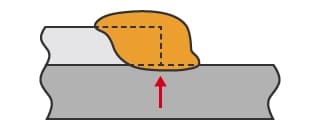
- 溶け込み不足
- 溶融金属への入熱不足などによって、必要な溶け込み深さに対し、溶け込み量が不足する不良です。重ね隅肉溶接の例を図に示します。突合せ溶接では開先下部で発生しやすいほか、薄板のT(水平隅肉)継手の場合、一般に溶け込み深さが薄板側の20%以下であると溶け込み不足といわれます。
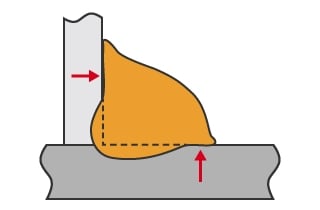
- 融合不良
- 部分的に溶融金属が母材に溶け込んでいない不良です。薄板のT(水平隅肉)継手の例を図に示します。原因として溶融金属への入熱不足や、溶融金属の先流れ、また円周溶接では、先行ビードと後行ビードが十分に溶け込まないままラップ溶接に移行した場合などに発生します。
完全溶け込み溶接・部分溶け込み溶接と強度
開先の違いにより、溶け込みの様式も変わり、同時に溶接部の強度も異なります。
- 完全溶け込み溶接
-
完全溶け込み溶接とは、突合せ溶接のように接合する母材の開先を溶融した接合材(溶加棒・溶接ワイヤー)で一体化し、埋め込む溶接方法です。
完全溶け込み溶接部は、母材と同じ耐力となるため、強度設計における溶接部の信頼性が高いといえます。一方で、高い溶接品質が求められます。特に溶接部の端部はアンダーカットなどの不良発生に注意が必要です。また、余盛りを過剰に設けた場合、そこに応力が集中し、割れなどの原因となるため、余盛りの管理・調整も重要となります。
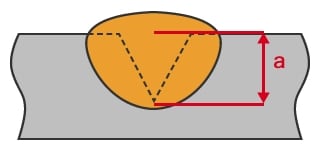
- 部分溶け込み溶接
- 部分溶け込み溶接とは、母材上に開先を部分的に設けて溶接する方法です。完全溶け込み溶接は母材の板厚全面を溶接する一方、母材を部分的にしか溶接しません。完全溶け込み溶接が一般的ですが、部材の設計・製作上、接合部が交錯する場合などは、部分溶け込み溶接が必要となります。
ただし、曲げモーメントや引張力が作用する箇所への部分溶け込み溶接は強度が不足しやすいため注意が必要です。溶接部の強度設計、そして、実際の溶接部の溶け込みが設計に準じ、「のど厚」などの寸法が条件を満たしているかの測定・検査が特に重要となります。
溶接部の測定・検査を効率化するマイクロスコープの最新事例
溶接部の断面は、溶け込みと母材のコントラストが低い場合が多く、従来の顕微鏡では、測定が困難なうえ人によるバラつきの原因でした。また、実体顕微鏡では、目視でスケールを確認し、測定値を手入力する必要がありました。
しかし近年は、デジタルマイクロスコープの技術進歩により、従来の顕微鏡の諸課題を解決し、溶接の溶け込みの鮮明さや寸法測定の効率を大きく変えました。キーエンスの超高精細4Kデジタルマイクロスコープ「VHXシリーズ」は、最先端の高解像度HRレンズ・4K CMOS・照明・画像処理技術による鮮明な画像と寸法測定で、溶接の溶け込み検査の効率化を実現しました。
溶け込みと母材の境界を鮮明に捉える4K高解像度画像
溶接部の断面では、溶け込み・母材ともに溶接部の境界のコントラストが低く、従来の顕微鏡では境界がはっきりと観えないことで、判断や測定が困難な場合がありました。
4Kデジタルマイクロスコープ「VHXシリーズ」は、高解像度な4K画像によりエッジを鮮明に捉えるこができます。溶接金属と母材の境界が区別しにくい重ね隅肉溶接の断面であっても、境界の鮮明なエッジや金属組織の違い、不良箇所をすぐに区別して観ることが可能になりました。
これにより、従来の溶け込み寸法測定時の迷いを解消し、作業工数を削減すると同時に検査の正確性を向上させることができます。

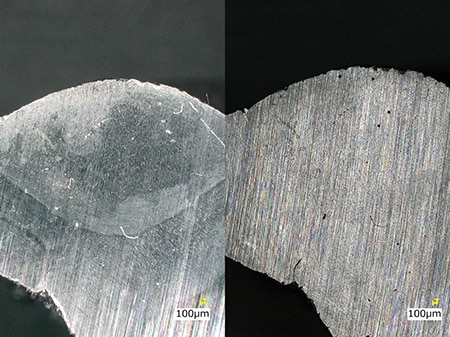
溶接部の寸法測定の効率化
溶接部断面の寸法測定は、強度と品質に関わる重要な検査です。しかし、従来の実体顕微鏡では、母材とビードのコントラストが低く測定箇所の判断が困難でした。また、目視でメモリと照合し、その数値を手入力する必要があったため、人による誤差や作業の煩雑化が課題でした。
4Kデジタルマイクロスコープ「VHXシリーズ」は、溶接部の境界も鮮明に表現する4K高解像度画像をモニターで見ながら、測定箇所をクリックするだけの簡単操作で、脚長・のど厚・溶け込み深さなどの「2次元寸法測定」が可能です。サブミクロンオーダーの高精度な測定であっても、簡単かつ短時間で完了するため、作業工数を大幅に削減できます。
また、最新の「自動エッジ抽出機能」により、人による測定箇所のバラツキを防ぐことができます。さらに、測定・保存したデータをアルバムから選ぶことで、再び寸法測定することも可能なため、多様な検査要望に対応します。
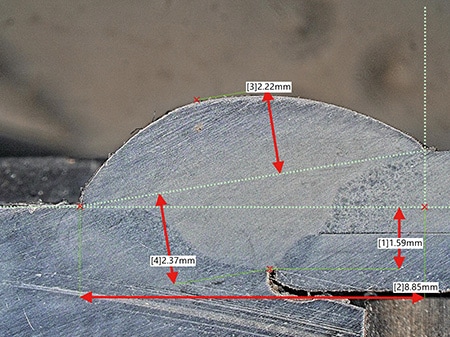
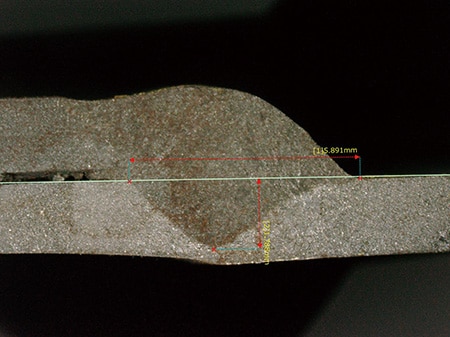
溶接の溶け込み測定
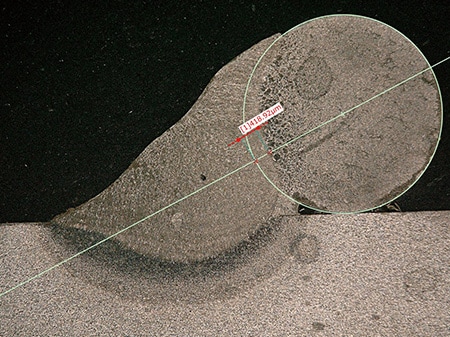
溶接ビードの3次元寸法測定・3D形状
溶接ビードは連続的な凹凸形状を持っています。ビード表面に余盛り不足・オーバーラップ・アンダーカット・ピット・割れなどの不良(非連続性)がある場合、目的とする機械的特性が得られず、破損原因となり得ます。しかし、従来の顕微鏡ではビードの凹凸の一部にしかピントが合わないうえ、余盛りなどの評価に必要な高さ情報が得られませんでした。
4Kデジタルマイクロスコープ「VHXシリーズ」は、簡単な操作で、複数のピント位置を瞬時に合成し、凹凸のある対象物へのフルフォーカスと「3次元寸法測定」を可能にしました。また、溶接ビードの3D形状を表示することで、ビード表面の形状をさまざまな角度から自由に検査できるほか、任意の断面のプロファイル測定も可能です。さらに、形状解析や粗さ解析も可能なため、溶接ビード周辺の母材表面のスパッタや割れなどの検査も可能です。
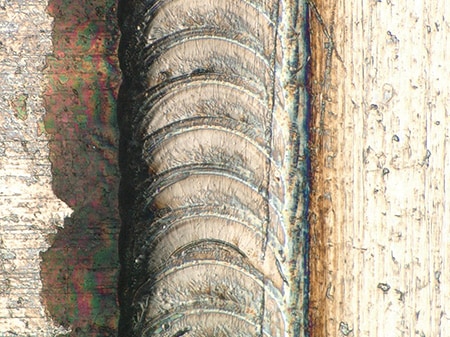
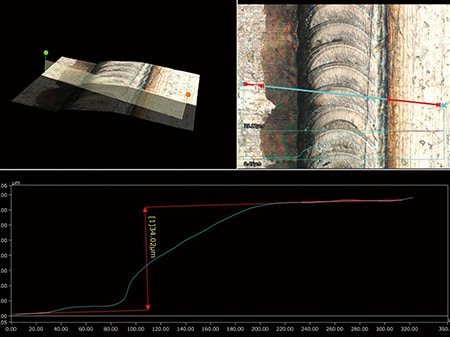
測定・検査レポートを瞬時に作成
従来は、測定・検査の煩雑さに加え、レポート作成も大きな作業負担となっていました。
4Kデジタルマイクロスコープ「VHXシリーズ」は、「レポート機能」を搭載。パソコンと同様にExcelのインストールが可能で、定型フォームを事前設定することで、寸法表記付きの拡大画像はもちろん、測定値やOK/NG判定を瞬時に入力します。これにより、レポート作成の手間と工数を飛躍的に削減できます。
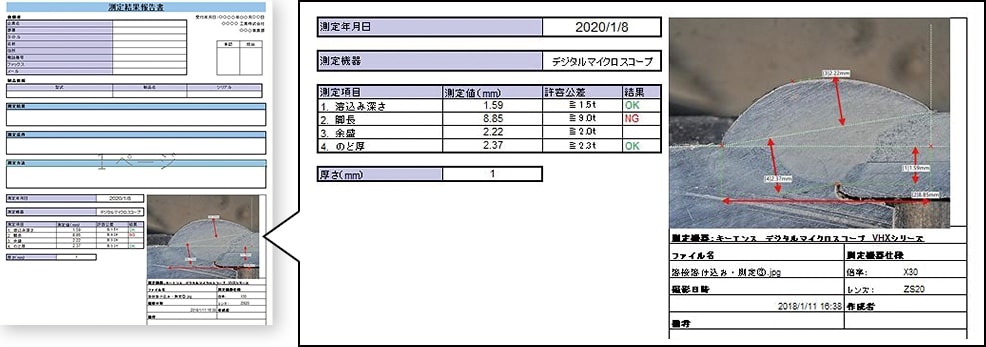
溶接部の測定・検査を変える4Kマイクロスコープ
「VHXシリーズ」は、4K高解像度画像でしか得られない鮮明さ、高精度な測定による数値データの取得、そしてデータの保存・活用において、従来の測定・検査の課題を解決し、作業効率を高める強力なツールです。他にも従来は不可能だった機能を数多く搭載しています。レンズ交換なく20~6000倍まで簡単操作で自動で倍率を変更する「シームレスズーム」や、微小な凹凸も鮮明に表現する「Opt-SEM」・「マルチライティング」、保存したデータの選択による各種設定の自動再現など、現場に求められるスピードや精度に応える機能を数多く搭載しています。
「VHXシリーズ」に関する詳細は、以下のボタンよりカタログをダウンロード、または、お気軽にご相談・お問い合わせください。