化学・材料・素材業界
コーティングのデジタルマイクロスコープでの観察・測定
フィルムやシート、鋼板、ガラスなどの比較的薄い基材(ワーク)に対して、新たな機能を付与する加工は、「コンバーティング」とも呼ばれます。一般的に、塗布(塗工)・蒸着・スパッタリングなどの手法でそれを実行することを「コーティング」と呼びます。スマートフォンやタブレット端末で需要の高いタッチパネルの電極や、液晶のガラスやフィルムの薄膜コーティング、電子基板への精密なパターン塗布など幅広い分野で活用されています。ここでは、コーティングのデジタルマイクロスコープでの観察・測定事例を紹介します。

メッキとコーティングの違い
- メッキ
- 素材を金属で被覆することで、金属を導電性表面に被膜する電気メッキが一般的です。化学反応を利用する化学メッキ、溶融金属中に浸して被膜を作る溶融メッキ、金属の蒸気を吹き付けて被膜を作る蒸着メッキなどもあります。
- コーティング
- 素材を別の材質で被覆することで、導電性表面と非導電性表面の両方で被膜を作ることができます。コーティングの中には、メッキも含まれると考えることができます。
コーティングの目的
- 機能付与
- 基材(ワーク)に対して、接着性、濡れ性、撥水性、耐食性、耐熱性、耐摩耗性などの機能を付与することができます。
- 表面処理
- 薬剤の塗布によって基材の表面を最適化するための「表面処理」を施すケースもあります。たとえば、半導体のウェハにレジストを塗布する前の薬剤塗布による疎水加工などが挙げられます。
- 装飾性(意匠性)
- 外観(意匠性)を向上させる効果があります。
コーティングの種類
- ドライコーティング(乾式法)
- 機能付与するための物質を「固体」のまま基材にコーティングする技術は、「ドライコーティング(乾式法)」と総称されます。代表的なコーティング方法として、真空蒸着やイオンプレーティング、スパッタリングなどが挙げられます。金属材料などのコーティングに用いられ、乾燥工程が不要で高品質な成膜が可能ですが、装置の大型化や連続生産数の制限、高コストといったデメリットもあります。
- ウェットコーティング(湿式法)
- 幅広い工業分野において一般的であり、「塗布(塗工)」が大きく関与するのが「ウェットコーティング」です。機能付与するための物質を溶媒に対して、溶解または分散といった処理により「液体化」します。その液剤を基材に対して均一に塗布し、乾燥や硬化させることにより「固体薄膜化」させる技術です。液膜へのホコリや異物の付着を避ける場合は、ウェットのプロセスでクリーンルームを使用します。ドライコーティングと異なり真空環境が不要で、大気圧環境下での塗布(塗工)が可能です。装置の自由度が大きく、ワーク(基材)の供給を連続的に行うことができます。ウェットコーティングは、量産におけるメリットが大きいため、さまざまな塗布方式を用いて広く採用されています。
デジタルマイクロスコープによるコーティングの観察・測定事例
キーエンスの4Kデジタルマイクロスコープ「VHXシリーズ」を用いたコーティングの観察・測定の最新事例を紹介します。
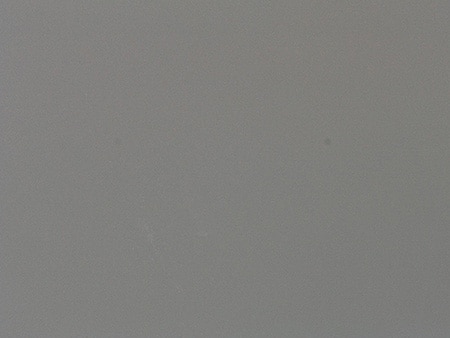
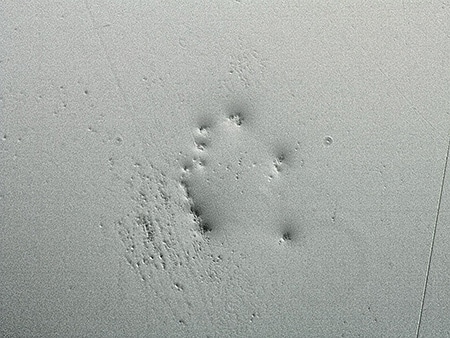
HDRで、欠点が可視化できます。

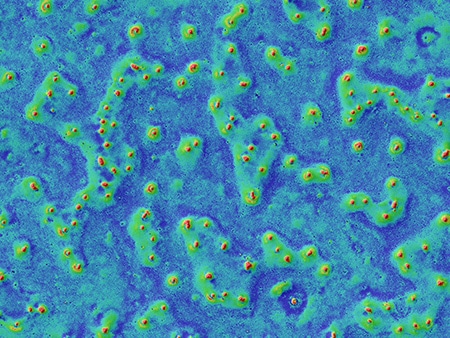
Opt-SEM(カラーマップ)画像
Opt-SEM機能(Optical Shadow Effect Mode)で
凹凸を可視化できます。

VH-Z20 200x 同軸落射照明
- A:通常画像
- B:微分干渉+HDR画像
微分干渉+HDRで、塗装ムラが可視化できます。
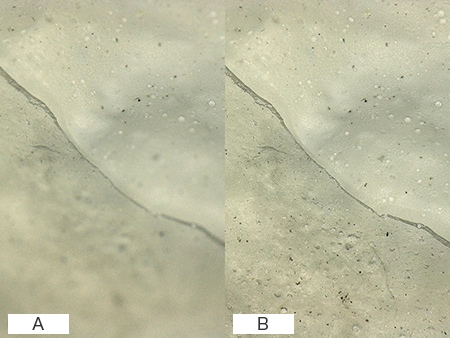
VH-Z20 100x リング照明
- A:通常画像
- B:深度合成画像
透明なコーティング膜の表面も観察できます。


自動面積計測で、コーティング粒子のばらつきが定量化できます。

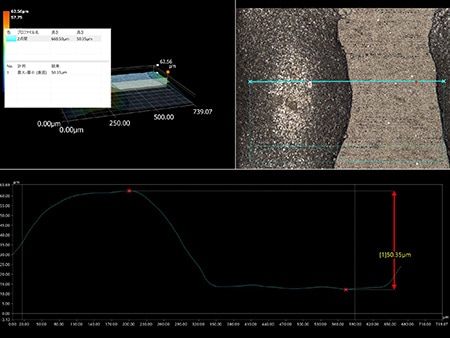
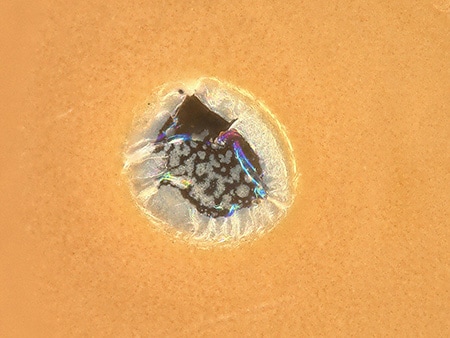
異物がコーティング膜の内部にあることが確認できました。