手間をかけずに穴位置を測定する方法
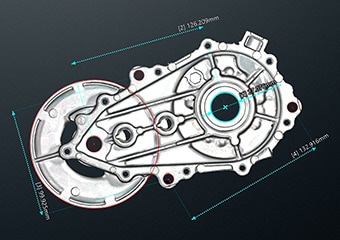
機械加工における『穴』とは、その名前のとおり、機械部品や金型などのワークに対してあけられた円筒上の空洞で、『孔』と書かれることもあります。また、穴をあける加工を『穴あけ加工』『穴加工』と呼び、さまざまな加工方法があります。
機械加工における穴の寸法測定では、穴の直径や深さ、ネジ穴の場合は内径やピッチ、そのほかにもワークに複数の穴をあける場合はネジの中心間距離(穴ピッチ寸法)など、さまざまな情報が必要になり、意外と厄介なものです。
今回は、そんな穴あけ加工の種類や測定方法などの基礎知識に加え、穴位置測定における課題、その解決策について解説します。また、キーエンスの3Dスキャナ型 三次元測定機『VL-700シリーズ』を活用し、穴位置の測定における手間を削減する方法についても紹介します。
- 機械加工における『穴あけ加工』とは?
- 穴あけ加工の種類
- 穴の向きや角度について
- 穴ピッチ寸法の表記とピッチ間距離測定
- 従来の穴位置測定における課題
- 手間をかけずに穴位置測定を実現する課題解決方法
- 穴位置測定が手軽にできる、3Dスキャナの活用で時短&効率化を実現
機械加工における『穴あけ加工』とは?
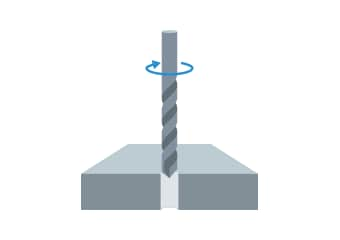
穴あけ加工とは、切削工具を使い、円筒穴をあける加工方法です。ボール盤や旋盤、マシニングセンタなどの工作機器を用い、切削工具にはドリルやタップ、リーマなどが使用されます。一般的にドリルを使用して加工することが多いため、穴あけ加工を『ドリリング』と呼ぶこともあります。
穴あけ加工には、浅穴加工と深穴加工や、すでにあいている穴を拡大するカウンターボウリングなどがあります。さらに下穴をあけるドリル加工や、用途に応じてリーマ加工やネジ切り加工、ザグリ加工などの特定の加工を施す場合もあります。
穴あけ加工の種類
一般的に切削加工で穴あけ加工を行う場合、まず『センター穴あけ加工』を行い、その後に下穴を開ける『ドリル加工』、その後に用途に合わせて『リーマ加工』『タップ加工』『ザクリ加工』などを行います。こちらでは、穴あけ加工の基本について解説します。
- センター穴あけ加工
- センター穴あけ加工とは、下穴位置の精度を高めるため、下穴のガイドになる『センター穴』をあける加工です。センター穴あけ加工を行うことで、下穴を切削する際にドリルの刃がズレてしまうことを防ぎます。板金加工などでは、穴あけ加工する際にポンチ(センターポンチ)でくぼみを作りますが、それと同様です。
- ドリル加工
- 穴あけ加工では、最初にドリルで下穴を空けます。空気穴など、精度を必要としない場合は、ドリル加工のみで完結する場合もあり、後処理を行っていない荒い状態を『キリ穴』と呼びます。また、大きな穴をあける場合は、下穴を中ぐり加工またはエンドミル加工することもあります。
- リーマ加工
- リーマ加工は、あけた穴の内径の精度を高める加工です。内側のドリル跡を滑らかに仕上げ、寸法精度を高めます。また、直径が大きい場合は、ボーリング工具を使って仕上げることもあります。一般的にピンの圧入などを行う場合に実施します。
- タップ加工
- タップ加工は、ボルトやネジを通すため、穴あけ加工後に内側にネジ山を作る加工です。一般的に『タップ』と呼ばれる、ネジ山を作る専用工具を使用するため、タップ加工と呼ばれています。ネジ穴加工では、タップのほかに『プラネットカッター』と呼ばれる専用工具を使用する場合もあります。
- ザグリ加工
- ザグリ(座ぐり/座繰り)加工は、ボルトなどを穴に通す際に、ボルトの頭が表面から出ないように、くぼみを作る加工です。ボルト穴が飛び出さないようにするほか、表面の粗い加工品や傾斜面の穴に対して、ボルトなどの締め付けを均一にするために平坦に仕上げるという目的もあります。
穴の向きや角度について
穴をあける場所や角度などにも違いがあります。ワークに対して真上から穴あけ加工する場合もあれば、ワークに対して斜めの角度に穴をあける『斜め穴』、ワークに対して横の面に穴をあける『横穴』、そのほか傾斜面に対して穴をあけるなどの場合もあります。このように斜めや横から穴をあける場合は、ワークからドリルが受ける切削抵抗の影響で正確な角度での穴あけ加工が難しくなります。
その対策として、エンドミルやフラットドリルで大きめのザグリを設けてドリルと加工面を垂直にしたり、センタードリルで位置決め加工を行ったりといった対策を行います。
穴ピッチ寸法の表記とピッチ間距離測定
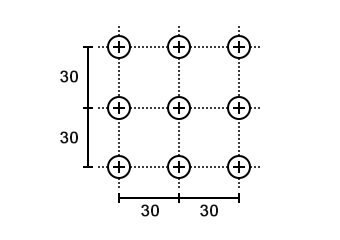
複数の穴あけ加工を行う場合、図面上に『ピッチ間距離(穴中心間距離)』が指定されている場合があります。たとえば、図のように『30』と記載されていれば、「30mmのピッチ間隔で穴をあけてください」という意味になります。
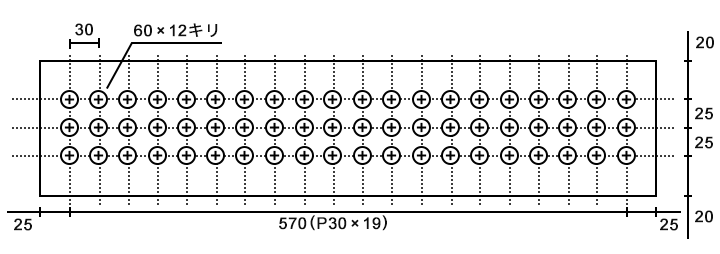
- 19
- ピッチ間隔の数 ※穴の数ではないので注意が必要
- 30
- 穴ピッチの距離(mm)
- 570
- 合計の距離
また、たとえば上記図面のように『570(P30✕19)』や『19✕30(=570)』といった表記があれば、「30mmのピッチ間隔で穴をあけてください。ピッチ間隔の数は19個です。ピッチ間隔を合計した長さは570mmになります」という意味になります。ここで間違えやすいのが、『19』という数字は穴の数ではなく、ピッチ間隔の数だということです。ピッチ間隔の数は、穴の個数-1になるので、この場合にあける穴の数は20個になります。
従来の穴位置測定における課題
部品・製品や金型には、ネジ穴や位置決め穴、軸受穴、水路用の穴など、さまざまな穴あけ加工が施されています。また、それぞれの用途によって求められる精度も異なり、公差が図面上で定められています。さらに穴の大きさや深さ、斜め穴や横穴であれば角度、またザグリ加工している場合であれば段付きの形状、タップ加工しているのであればネジ山の形状など、非常に多くの測定項目が存在します。今回は、その中でも穴ピッチ寸法に代表される、穴位置測定の課題を中心に紹介します。
ピッチノギスによる穴位置測定の課題
ピッチノギスとは、穴ピッチ寸法の測定に用いられる専用のノギスです。その特徴は、ノギスのジョウ(被測定物をはさむ部分)が円錐状になっており、適切に穴ピッチ寸法を測定できるようになっていることです。また、ピッチノギスのほか、『穴ピッチ用ノギス』『丸穴ピッチノギス』と呼ばれることもあります。このピッチノギスは、同一平面上の穴であれば、正確に穴ピッチ寸法を測定可能ですが、高さの異なる穴ピッチに関しては原理上、測定が困難です。また、手作業で測定を行うので、測定方法や測定者によって誤差が生じることもあり、時間がかかることも課題でした。また、深穴の場合は奥まで入らないので測定が困難です。
三次元測定機による穴位置測定の課題
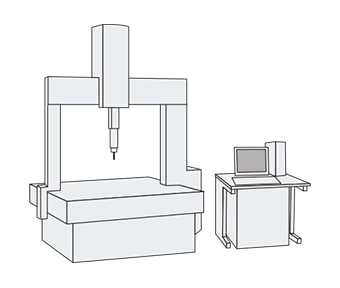
穴位置測定の方法として、三次元測定機を用いる方法もあります。三次元測定機とは、一般的にステージ上の対象物に接触子をあて、縦、横、高さから三次元座標を取得し、対象物の寸法・位置関係・輪郭形状・幾何公差などを高精度で測定できる機器です。三次元測定機であれば、同一平面上になく、高さの異なる穴でも測定可能です。一方で基準面に対して平面上にない斜め穴・横穴を測定する場合は、サンプルの固定方法を変えないといけないという課題がありました。また、深穴であったり、穴の大きさであったり、測定内容にあわせてスタイラス/ブローブを変更する手間もかかります。
手間をかけずに穴位置測定を実現する課題解決方法
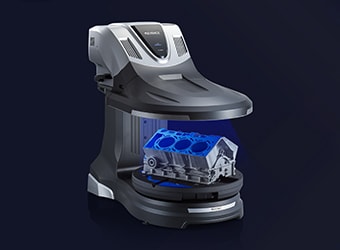
穴位置測定では、測定する穴があいている場所、また大きさや深さによって、測定が非常に難しかったり、物理的に不可能だったり、手間がかかったりしていました。それらの課題を解決する手法がキーエンスの3Dスキャナ型 三次元測定機『VL-700シリーズ』です。『VL-700シリーズ』は、ステージ上に置いた対象物をワンショット最速8秒で360°スキャンを実現し、高精度に三次元形状を測定可能。ワークの穴位置も手軽かつ正確に測定できます。
また、ピッチノギスのように手作業による測定ではないため、早く、正確な測定が可能で、三次元でワークの形状を捉えるので、穴位置の高低差による影響も受けません。また、三次元測定機のようにワークの向きによる影響もなく、ワンショットですべての穴位置を把握できます。
メリット1:従来は困難だった場所・形状でも3Dスキャナなら測定できる
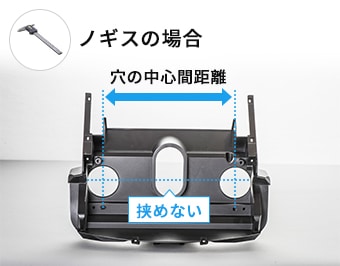
一般的なノギスでは、仮想点になる穴の中心を挟むことができず、穴ピッチ寸法の測定が困難でした。そこでピッチノギスを使用しますが、それでも穴位置に高低差があると測定ができませんでした。また、測定機を使用する場合でも深穴の場合は、スタイラスが届かず、測定できない場合もありました。キーエンスの3Dスキャナ型 三次元測定機『VL-700シリーズ』であれば、全周の3Dデータを取り込むので、データが取得できる箇所であれば、どんな穴位置・穴形状でも正確に測定可能です。さらに複雑な操作は必要なく、クリックするだけで穴位置測定を実現。非接触という特徴を生かし、ハンドツールなどが届かない穴の奥までしっかりと測定できます。
メリット2:スキャンデータを自動でCADデータに変換して穴位置を図面と比較できる
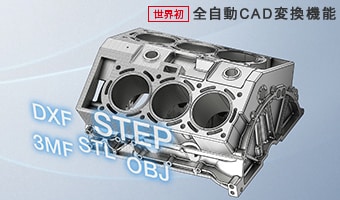
キーエンスの3Dスキャナ型 三次元測定機『VL-700シリーズ』は、スキャンしたデータを自動でCADデータに変換可能です。さらに3D-CADデータをインポートすれば、測定データと比較して差分を視覚的に表示し、異常箇所の特定に役立ちます。穴位置を含めた形状などを手軽に図面と比較・検証することができ、穴位置測定にかかる手間を大幅に削減可能です。さらに豊富な2D・3D解析機能があり、クリックのみの直感的な操作で穴位置の測定を実現します。また、大きなサンプルでも一発で測定でき、大幅な測定時間短縮につながります。
メリット3:サンプルを切らずに断面の測定ができる
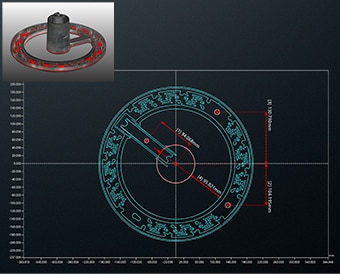
従来の測定方法では、サンプルの表面しか測定できませんでした。しかし、キーエンスの3Dスキャナ型 三次元測定機『VL-700シリーズ』は、測定データから非破壊で断面を作成し、詳細に測定・解析が可能です。3D形状データから自由に基準面が設定でき、あらゆる方向から断面測定ができます。そのため、高さの異なる穴のピッチも手軽に知ることができます。また、360°の全周でスキャンするので、三次元測定機のように置き方によって測定できない場所が発生する心配もありません。
メリット4:深穴などの奥まった場所の穴位置測定もできる
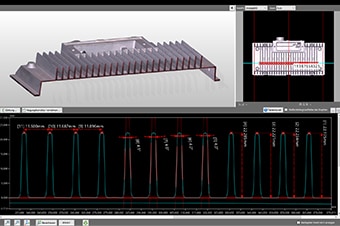
キーエンスの3Dスキャナ型 三次元測定機『VL-700シリーズ』は、仮想的にカットした断面の測定が可能です。そのため、たとえば穴あけ加工の断面を仮想的に切断することで、従来では難しかった深穴、またザグリ加工した断面形状やタップ加工したネジ形状など、細部まで正確に形状を測定可能。また、従来の三次元測定機では、縦穴や斜め穴、横穴などが混ざっている場合、測定する穴に合わせてサンプルの置き方を変える必要がありましたが、『VL-700シリーズ』であれば、そんな手間も不要です。
穴位置測定が手軽にできる、3Dスキャナの活用で時短&効率化を実現
従来のハンドツールによる測定、また接触式の三次元測定機による測定では、さまざまな課題があった穴位置測定ですが、キーエンスの3Dスキャナ型 三次元測定機『VL-700シリーズ』を活用すれば一発で解決!非接触かつ360°の全周スキャンにより、穴位置測定の手間を大幅に削減でき、時短&効率化を実現します。
- ワンショット最速8秒で360°スキャンが可能なので、測定にかかる時間を大幅に短縮。
- 3Dデータをもとに穴位置測定するので、穴の場所や角度、形状などを気にせず測定。
- 測定箇所にあわせて何度も置き方を変える必要がなく、測定の手間を大幅に削減。
- スキャンデータを自動でCADデータに変換し、インポートした3D-CADと簡単に比較が可能に。
- 500mm以上あるサンプルでもワンクリックでスキャンでき、サイズを問わずに穴位置測定が実現。
- 従来は正確な測定が困難だった深穴なども仮想的にカットした断面から穴位置測定が可能。
従来の測定方法では、非常に手間のかかっていた穴ピッチ距離などの穴位置測定。それがキーエンスの3Dスキャナ型 三次元測定機『VL-700シリーズ』なら、ワンショット最速8秒のスキャンで完了し、全体を3Dデータとして取得でき、さらに断面形状も把握できるので、手間をかけずに穴位置を測定できます。さらに図面との比較もワンクリックなので、穴位置測定にかかっていた時間と手間を大幅に削減でき、検査の大幅な効率化を実現します。