シートメタル(板金)の検査を最適化する方法
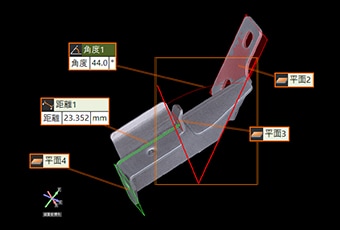
板状の薄鋼板を『シートメタル』や『板金』と呼び、鉄板やアルミ板、ステンレス板などの金属材料から部品や構造物を製作するプロセスを『シートメタル加工』もしくは『板金加工』と呼びます。シートメタル(板金)加工は、身近なところでは家電製品の筐体やクルマのボディ、そのほか建造物の外壁、航空機の外装など、さまざまな分野に用いられており、ものづくりにおいて欠かせない加工方法のひとつです。
また、シートメタル(板金)加工では、切断やパンチング、曲げ、溶接など、さまざまな加工方法が複合的に用いられ、最終的な部品や構造物になります。
そのため、複雑な形状の製品も多く、溶接などの加工も含まれるので歪みや反りなどが発生しやすく、形状や寸法の検査が難しいといった課題もありました。
このページでは、そんなシートメタル(板金)加工の基礎知識に加え、シートメタル(板金)の検査を最適化する方法などについて解説します。
- シートメタル(板金)加工について
- シートメタル(板金)加工の主なプロセス
- シートメタル(板金)加工とプレス加工の違い
- 精密板金加工とは
- 従来のシートメタル(板金)の検査における課題
- 従来のシートメタル(板金)の検査における課題
- シートメタル(板金)の検査を最適化、正確かつ比較も簡単にできるので大幅な効率化が可能
シートメタル(板金)加工について
シートメタル(板金)加工では、金属の板材を切断したり、曲げたり、溶接したり、表面加工などを行い、目的の形状に仕上げます。その加工方法は、目的の形状によって異なりますが、以下は一般的なシートメタル(板金)加工の流れです。まず、材料となる金属の板材をシャーリング加工機で必要な寸法に切り出し、その後にNCタレットパンチプレスで打ち抜き加工(タレパン加工)します。その後にブレーキプレスという加工機で任意の形状に曲げ、スポット溶接などで板を接合。必要に応じて穴開けや研磨、洗浄、塗装などを行い、製品となる筐体に仕上げます。
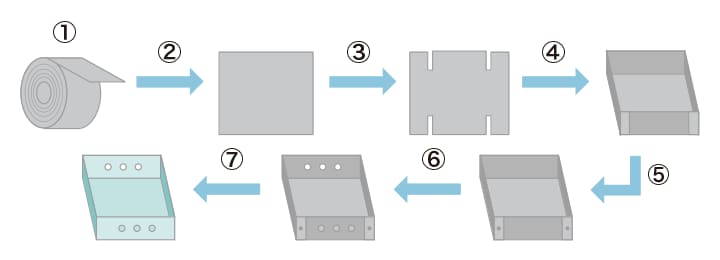
- ①
- 板材
- ②
- シャーリング加工
- ③
- タレパン加工
- ④
- ブレーキプレス
- ⑤
- スポット溶接
- ⑥
- 穴開け・研磨
- ⑦
- 洗浄・塗装
シートメタル(板金)加工の主なプロセス
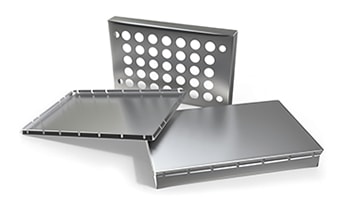
上記でも説明しましたが、シートメタル(板金)加工では、『切断加工/打ち抜き加工』『曲げ加工』『溶接』などの工程を経て、製品が完成します。こちらでは、それぞれの加工について解説します。
切断加工/打ち抜き加工
切断加工/打ち抜き加工は、展開した図面に合わせて金属の板材を切り出す/打ち抜く加工です。一般的にはシャーリング加工機やレーザー加工機などを用いて切り出したり、『タレパン』と呼ばれるタレットパンチプレスなどを用いて打ち抜いたりします。また、抜き打ち加工のことを英語で『Blanking(ブランキング)』、打ち抜き加工した金属の板材を『ブランク材』と呼ぶことから、この工程を『ブランク加工』とも言います。
曲げ加工
曲げ加工は、切断加工/打ち抜き加工を行った金属の板材を折り曲げて任意の形状に成形する加工方法です。シートメタル(板金)加工では、プレスブレーキと呼ばれるベンダーを用いて曲げ加工を行います。一般的にパンチ/ダイなどの金型を用いて成形するので、工程としてはプレス加工と同様になります。
板金溶接
曲げ加工を行った板材同士を接合する必要があるため、シートメタル(板金)加工では溶接も用いられます。また、シートメタル(板金)における溶接を『板金溶接』とも呼びます。以下は、板金溶接で用いられる手法です。
- YAGレーザー溶接
-
YAGレーザー溶接は、イットリウム(Yttrium)/アルミニウム(Aluminum)/ガーネット(Garnet)の頭文字をとった溶接方法です。被削材に与える熱影響が少なく、薄鋼板に対して歪みも少ないことから精密板金加工で用いられます。また、均一なビードで仕上がりが美しいといった特徴もあります。
- 半自動溶接
-
半自動溶接は、手作業で行う必要がありますが、ワイヤーが自動で供給される溶接方法です。ワイヤーの送りが自動になり、溶接速度が速いといった特徴があります。また、使用するシールドガスの種類によって『CO2溶接』『MAG溶接』『MIG溶接』のように分類されます。
- TIG溶接
-
TIG溶接は、タングステン(Tungsten)/イナート(Inert)/ガス(Gas)の頭文字をとった溶接方法です。シールドガスにアルゴンを用い、ステンレスやアルミなどの材料を問わず、接合できることが特徴です。また、溶接後の仕上がりが美しく、美観を求められる製品で多く用いられます。
- スポット溶接
-
スポット溶接は、電極で部材を挟み込み、点で接合する溶接方法です。上下の電極棒に電気を流すことで重ねた板に熱を発生させ、融解させて溶接するため、板材の接合に適しています。ただし、厚板の場合は適合しない場合もあります。
- スタッド溶接
-
スタッド溶接は、スタッドと呼ばれるボルトやナットを金属板に接合する溶接方法です。溶接に必要な時間が比較的短く、母材への影響が少ないことが特徴で、生産性に優れています。
シートメタル(板金)加工とプレス加工の違い
シートメタル(板金)加工とプレス加工の違いについて説明します。シートメタル(板金)加工とプレス加工は、どちらも塑性変形を利用した加工方法です。そのため、広義では、シートメタル(板金)加工は、プレス加工の一種、もしくはプレス加工を用いた成形と言えます。ただし、シートメタル(板金)加工では、主に汎用金型を使って曲げ加工のみを行います。一方のプレス加工は、専用金型を用い、複雑な形状の製品を成形するといった違いがあります。
ちなみにプレス加工には、多品種少量の部品に関してオペレーターが手作業で被加工材をセットして1工程ずつプレスする『単発プレス』と、コイル状の被加工材をセットして複数のプレス工程を順送りで行う『順送プレス』、そのほか単発プレスと順送プレスの利点を取り入れて自動で連続加工を行う『トランスファープレス』などがあります。
- 単発プレス
-
単発プレスは、被加工材を人の手でプレス機にセットし、加工が終わったら加工材を人の手でプレス機から取り出す、最も一般的な方法です。大型加工品の少量生産にい適していますが、1回のプレスで1つの加工を行うので連続加工/自動加工はできません。
- 順送プレス
-
順送プレスは、複数の工程分の凹凸が設けられた金型を使用し、コイル状に巻いた被加工材をプレス機にセットして、少しずつ流していくことで順次加工します。トランスファープレスに対して被加工材を搬送する装置が不要で、加工が早く、複雑な加工を1工程で仕上げられるので、生産効率が高いプレス加工です。また、『プログレッシブプレス』とも呼ばれ、『プログレ』『PRG』とも略されます。
- トランスファープレス
-
トランスファープレスは、単発プレスを組み合わせたプレス方式で、『TRFプレス』とも呼ばれます。1つの加工が終わったら次の工程に被加工材を搬送するので、順送プレスに比べて生産性は劣りますが、歩留まりがよく、比較的大きな加工材を扱えることがメリットです。
精密板金加工とは
シートメタル(板金)加工では、主に1~4mm程度の金属板を使用しますが、その中でもとくに0.1~3mm程度の薄い金属板を使った加工を『精密板金加工』と呼びます。主に高い寸法精度が求められる電子機器や通信機器、半導体製造機器の部品などに用いられ、曲げの多い複雑な部品、また高精度な穴開けが必要な部品で採用されます。また、加工だけではなく、検査においても高い精度が求められます。
従来のシートメタル(板金)の検査における課題
シートメタル(板金)加工では、『切断加工/打ち抜き加工』『曲げ加工』『溶接』などの複数の工程を経て製品を成形するため、複雑な形状が多く、各工程で歪みや反りなどの変形が発生することもあり、寸法検査などがシビアになります。また、精密板金加工では、高い寸法精度が要求されるので、さらに検査が難しくなるという課題がありました。
ノギスによる測定の課題

寸法測定で多く使われるノギスですが、複雑なシートメタル(板金)加工品の場合、全体形状の把握が難しく、具体的にどのような形状差異があるのか特定が困難といった課題がありました。また、測定者による誤差なども生じるため、精密板金加工品には不向きです。
溶接による歪みなどの評価

シートメタル(板金)加工では、溶接による接合も行われますが、溶接時の熱で歪みや反り、うねりなどが発生します。とくに薄鋼板の場合は、歪みや反り、うねりが発生しやすくなります。しかし、このような溶接によって生じる全体的な歪み量の定量的な評価は、ノギスやダイヤルゲージなどの一般的な測定方法では困難です。ノギスでは、あるポイントの歪みや反り、うねりは判断できても面全体、また製品全体の測定が難しく、実施する場合には測定箇所を増やすなど手間と時間がかかりました。
従来のシートメタル(板金)の検査における課題
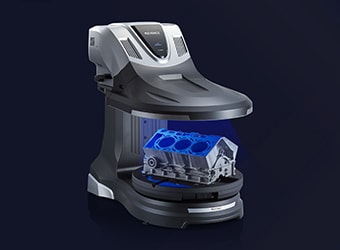
シートメタル(板金)加工品の検査における課題を解決するには、全体の形状や寸法を正確に把握する必要があります。それらの改題を解決し、検査を最適化する手法がキーエンスの3Dスキャナ型 三次元測定機『VLシリーズ』です。『VLシリーズ』は、ステージ上に置いた対象物をワンショット最速8秒で360°スキャンを実現し、高精度に3次元形状を測定可能。シートメタル(板金)加工品の全体像を把握でき、検査の最適化を実現します。
さらに設計した3D-CADデータとの比較ができ、差分をカラー表示することで解析時間を大幅に短縮。そのほかにも同じ製品のデータ同士を比較する現物比較測定、ワークの厚み測定、幾何公差測定などもできるので、これまでは発見できなかった違いも一目瞭然。さらに2種類のレンズを標準搭載し、高倍率レンズを選択することで大きなワークをまるごと3D計測、精密板金加工品の微細形状も高精細に3D測定可能です。
こちらでは、『VLシリーズ』を使い、シートメタル(板金)加工品の検査を最適化するメリットについて、ごく一部ですが紹介します。
メリット1:溶接による歪み量の定量評価ができる
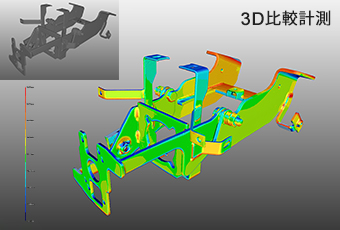
従来の検査方法では、ノギスやダイヤルゲージなどで測定を行っていましたが、部分的にしか測定できず、製品全体の溶接による歪み量などの測定が困難でした。キーエンスの3Dスキャナ型 三次元測定機『VLシリーズ』を使えば、ワーク全体をスキャンでき、3D-CADデータとの比較で溶接による歪みを定量的に評価可能です。
メリット2:座標測定で寸法測定も簡単にできる
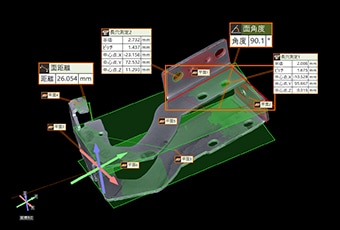
複雑な形状のシートメタル(板金)加工品の場合、3次元形状かつ穴開け箇所などもあり、寸法測定に手間がかかっていました。キーエンスの3Dスキャナ型 三次元測定機『VLシリーズ』なら取得したデータから従来の測定機では困難だった任意の箇所の測定ができます。さらにXYZ座標情報からの座標測定にも対応。そのほか、幾何公差測定もできるので、短時間で正確な検査を実現します。
メリット3:曲げ部分などの小さなRも正確に測定可能です

従来の測定方法では、小さなRなどの測定が困難でした。しかし、キーエンスの3Dスキャナ型 三次元測定機『VLシリーズ』なら、曲げ部分などの小さなRも正確に測定でき、さらに3D-CADデータや測定した現物との比較も可能。たとえば、ヒンジ用板金部品の耐久試験後の変形評価なども簡単に行えます。
シートメタル(板金)の検査を最適化、正確かつ比較も簡単にできるので大幅な効率化が可能
従来は測定方法では困難だった、また時間がかかっていたシートメタル(板金)加工品もキーエンスの3Dスキャナ型 三次元測定機『VLシリーズ』を使えば、簡単に測定が可能で、検査の最適化を実現します。3D-CADデータとの比較も容易になり、検査の精度も高くなり、工数削減にも貢献します。
- ワンショット最速8秒で360°スキャンが可能なので、測定にかかる時間を大幅に短縮できます。
- スキャンデータを自動でCADデータに変換し、寸法を測定できるので効率的です。
- 大型の成形品もワンショットで測定できるので、ワークの大きさを選ばずに検査可能です。
- ノギスなどが入りにくい入り組んだ形状でも3Dスキャナなら各部の寸法測定ができます。
- 小さなRの曲げも正確に測定できるので、精密板金加工品の検査にも適しています。
- 全体を一括でスキャンし、測定できるので溶接による歪み量などの定量的な評価に最適です。
キーエンスの3Dスキャナ型 三次元測定機『VLシリーズ』ならワンショット最速8秒のスキャンで完了し、そのデータをもとにシートメタル(板金)加工品の検査も手軽に行えます。複雑な形状や大型の加工品にも対応しているので1台でさまざまな検査に対応し、さらに3D-CADデータとの比較も簡単なので、検査の最適化を実現します。