ロボットと人が一緒に働く「協働ロボット」とは?

従来の産業用ロボットは、人の代わりに単純作業を行うことが主な用途でした。しかし近年では、より高度で柔軟さが求められる作業を人と共に行う「協働ロボット」に注目が集まっています。その要因として規制緩和に加え、安全技術やアプリケーションの進化が挙げられます。今回のコラムでは、協働ロボットの基礎知識や安全対策、導入方法、導入後のメリットなどをわかりやすく紹介します。
協働ロボットの基礎知識
- 従来の産業用ロボット
- 従来は危険エリアに入れないように、周囲に柵が必要でした。
- 協働ロボット
- 柵無しで作業者と産業用ロボットの協働作業が可能になりました。
“人”と協力しながら働く人間協調型の産業用ロボットを「協働ロボット」と呼びます。従来の産業用ロボットは、安全を確保するために柵で囲い、隔離された条件下での作業に限定され、協調作業ができませんでした。この“人”と“ロボット”の間にある“柵”を取り払い、同じ空間で作業できるように工夫したものが「協働ロボット」です。
従来の産業用ロボットは、設備が大掛かりになるので大規模かつ大量生産のラインを中心に用いられてきました。一方で協働ロボットは、より柔軟な作業に対応するために生まれ、同じ産業用ロボットではありますがコンセプトが異なります。以下に従来の産業用ロボットと協働ロボットの一般的な違いについてまとめてみました。
従来の産業用ロボット | 協働ロボット | |
---|---|---|
作業内容 | 単純作業が中心(産業用ロボット単体で完結する作業) | 柔軟な作業に対応可能(人と一緒に作業を行うことが可能) |
設置場所 | 柵の設置が可能な大型ラインが中心 | 柵が不要なので設置場所を選ばない |
制御 | 位置制御 | 位置制御+力制御 |
対象物 | 同品種・大量生産が中心 | 変種変量に柔軟に対応可能 |
協働ロボットの実用例
自動車組立ラインでのウインドウ搭載作業
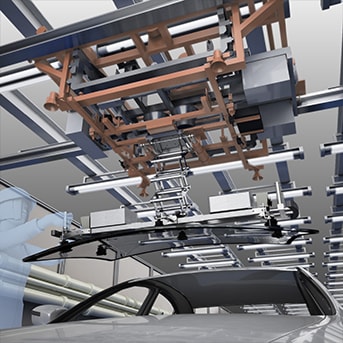
協働ロボットの実用例として自動車組立時のアシストロボットを紹介します。「最終的な品質確認は人、力作業はロボットが行う、人と共存する『協働』化」を目指して、これまで作業者2名で行っていたウインドウ搭載作業を作業者1名で対応できることがメリットです。従来のウインドウ搭載作業は、車体を停止して人の手によって行っていましたが、ロボットのサポートによってラインを止めることなく作業でき、作業効率が飛躍的に向上します。ウインドウを持ちあげる力と高い精度が要求される工程でしたが、ロボットのアシストがあれば女性でも軽々と作業可能です。負担の大きかった「力」をロボットに、精度が求められる「技能」を人に振り分けた好例と言えます。あくまで一例ですが、人とロボットで作業を分担することで、それぞれの得意分野を活かすことができます。
協働ロボットが注目を集める理由
80W以上の産業用ロボットを利用する場合、以前は柵を設け、人の作業スペースと隔離する「80W規制」がありました。しかし、2013年12月の規制緩和により、「ロボットメーカーやユーザーが国際標準化機構(ISO)の定める産業用ロボットの規格に準じた措置を講じる」等の条件を満たせば、80W以上の産業用ロボットと人が同じ空間で働くことが可能になりました。この規制緩和により、国内で協働ロボットの開発が加速しています。
規制緩和と同時に安全技術の進化やリスク評価手法も整備され、安全性が確保できるようになったことも注目を集めている要因です。また、協働ロボットを活用するアプリケーション開発が進み、プログラミングやインテグレーションの手間が軽減。実装期間の短縮や効率化、導入コスト削減が進み、大企業のみならず中小企業でも導入できる環境が整いました。「80W規制の緩和」「安全技術の進化」「アプリケーション活用の容易さ」という3つのポイントに加え、「ロボット導入実証事業」や「ものづくり補助金」など、ロボット関連の補助金制度も導入を後押しする要因になっています。
協働の効果を最大限に発揮するには?
産業用ロボットは、ハンドやセンサ類を取り付け、プログラムを設計し、生産システムに組み込まれて初めて価値を発揮する「半完結製品」です。そこでハンドやセンサ類などのハードウェアを組み合わせ、それらが機能するようにソフトウェアをプログラムするインテグレーションの作業が必要です。協働ロボットの導入までには以下のようなステップがあり、システムインテグレーターが重要になります。
協働ロボット導入の流れ
- 課題やニーズの明確化
- 現在の作業工程を見直し、課題やニーズを明確化し、解決方法を検討します。
- プロジェクト・マネジメント
- 導入から運用まで含めた計画をまとめます。
- ロボット選定
- 作業固定・衛生環境などを考慮して最適なロボットを選定します。
- ロボット設計
- ロボット本体に加え、ハンドやフィーダーなどの周辺機器、生産ライン全体の設計を行います。
- 安全設計
- ロボット導入のリスクを検討し、規格に沿った安全策を講じます。
- 周辺設計
- 前後の工程、協働する人との関係を考慮し、ロボット導入の効果を最大化できるように周辺環境を整えます。
- 制御・センシング設計
- ロボットの動作を制御するプログラムやセンサの追加などを行い、実際の生産ラインに組み込みます。
- 保守・運用
- 生産ラインで保守・運用を行う中で調整を行い最適化します。日々のティーチングなども含まれます。
協働ロボットの導入ハードルを下げる最新アプリケーション
従来の産業用ロボットは、生産ラインの組み替えや品種変更、業務前のティーチングなどに手間がかかり、導入・運用の障壁になっていました。近年では、より簡単にプログラミングできるアプリケーションが開発され、導入・運用のハードルも低くなっています。特に協働ロボットの場合は、従来の産業用ロボットに比べて柔軟な工程・作業への対応が求められるので「アプリケーション活用の容易さ」は、導入はもちろん運用においても非常に重要な項目です。
例えば、導入の手間だったプログラミングが不要になるアプリケーションなども登場し、協働ロボットに限らず、産業用ロボットの導入は簡単になりました。また、画像センサ&画像処理を活用したロボットビジョンシステムを導入すれば、手間のかかるティーチング作業からも開放され、大幅に手間が削減できるほか、多品種への対応も容易になります。
ロボットビジョンシステムで
人とロボットの「協働」がより簡単に!

ロボットビジョンシステムは、画像センサおよび画像処理システムを活用して対象物を認識するシステムです。協働ロボットにおいてもロボットビジョンシステムの活用は非常に有効で、作業の効率化や多品種・他工程への対応、コスト削減などに効果を発揮します。以下では、代表的なロボットビジョンシステムの活用例を紹介します。キーエンスでは、 2Dロボットビジョンシステム/3Dロボットビジョンシステムを用意し、協働ロボット導入のサポートをしています。
ロボットビジョンシステムの活用例01
対象物の認識
対象物を認識し、位置補正を行うことで多品種かつ柔軟な作業に対応します。専用の搬送用パレットやパーツフィーダーが不要になるのでコスト削減につながり、省スペースかつ汎用性の高い生産ラインにロボットを組み込めることがメリットです。キーエンスでは、2D/3Dのロボットビジョンシステムをラインナップしています。3Dロボットビジョンシステムであれば、バラ積みのワークも正確に検出可能です。
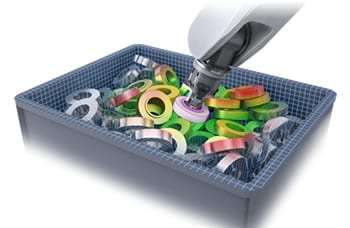
ロボットビジョンシステムの活用例02
オートキャリブレーション
従来の産業用ロボットは、オペレーターが手動でティーチングを行っていました。キーエンスの2Dロボットビジョンシステム/3Dロボットビジョンシステムは、ワンクリックで簡単にキャリブレーションが完了する「オートキャリブレーション機能」を搭載しているので生産性アップにつながります。

ロボットビジョンシステムの活用例03
既存の産業用ロボットの活用
キーエンスの2Dロボットビジョンシステム/3Dロボットビジョンシステムは、産業用ロボットメーカー各社の標準コントローラに接続可能で、メーカー名を設定するだけで簡単にセットアップできます。あらかじめサンプルプログラムも用意し、動作フローを指定するだけで自動的にメーカーに応じたプログラム作成が可能なので導入・運用の手間も最小限に抑えられます。
