3M(ムリ・ムダ・ムラ)を取り除く

生産管理や業務フローの改善を進めるに当たり排除すべき要素として挙げられるムリ・ムダ・ムラ(3M)ですが、物流の現場でも同様にムリ・ムダ・ムラが存在しています。 こちらでは、3Mの基礎知識と、物流の現場に潜む3Mの正体、それを排除する方法を説明します。
3M(ムリ・ムダ・ムラ)とは
- ムリ
- 能力以上に負荷がかかっている状態
- ムダ
- 能力に対して負荷が下回っている状態
- ムラ
- ムリとムダの両方が混在し、さまざまなタイミングが発生している状態
理想的な作業環境は、「負荷(作業量)」と「能力(キャパシティ)」が均衡している状態です。例えば、ある量の作業を一定時間内に終える目標を設定した場合、それを実現できなければそこには「ムリ」が生じていると言えます。逆に、その目標をクリアして時間が大幅に余ってしまうようなら「ムダ」だと言えます。一方、ムリとムダの両方が混在し、作業が不安定な状態を「ムラ」と言います。
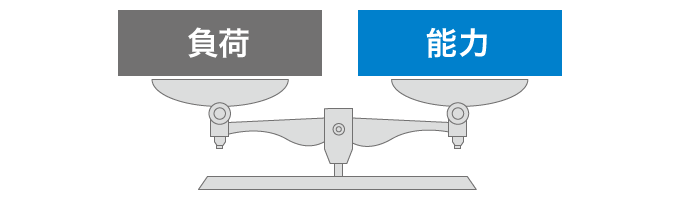
3M(ムリ・ムダ・ムラ)の発生原因
「負荷(作業量)」と「能力(キャパシティ)」が均衡している状態が理想的な作業環境であり、負荷と能力のバランスが崩れると3M(ムリ・ムダ・ムラ)が発生します。その原因として人員配置や生産計画が不適切だと考えられます。負荷が増えれば作業が滞り、能力が増えれば人員が余る状態になります。このバランスをどのように均衡させるかが非常に重要です。
- 負荷が能力を上回る場合
-
- 作業が溜まり、滞ってしまう
- 作業能力を超える負荷がかかると、作業は停滞し、3M(ムリ・ムダ・ムラ)が発生します。
- 能力が負荷を上回る場合
-
- 人員が余り、作業待ちになる
- 作業能力に余裕があるのに負荷が少ないと、人員が余り、3M(ムリ・ムダ・ムラ)が発生します。
物流現場における3Mの問題点
人員不足 | 人員過剰 |
---|---|
|
|
3M(ムリ・ムダ・ムラ)を取り除く方法
物流現場でムリ・ムダ・ムラが発生する最大の要因は、適切に人員が配置できていないことです。人手不足でもダメ、人手が余っていてもダメです。さらに忙しい工程と暇な工程が時間帯や日によって混在していることも問題です。
しかし、物流の現場では日によって入荷や出荷の数量に大きな変動があるので、どのセクションに何人配置しておけばよいという見通しがつきにくいものです。そのため明確な生産計画に対して人員配置する製造業のようにはいかず、3M(ムリ・ムダ・ムラ)が発生しやすくなります。
そこで物流業界で3Mを取り除くには、最適な人材配置以上に人への依存度を減らすことが求められます。そのひとつの方法が、ハンディターミナルによる正確な管理です。
3M(ムリ・ムダ・ムラ)対策でのハンディターミナル・コードリーダ・RFIDの活用
工場の生産ラインに比べると自動化・機械化の余地が少ない物流の現場において、3M(ムリ・ムダ・ムラ)の要因となる人間への依存度を減らすことは容易ではありません。しかし、機器やシステムの導入は、比較的手軽かつ効果的な対策といえます。
物流現場では、目視による検品作業や送り状・納品書と現品の確認が行われています。これらの作業は負荷が大きく、見間違いや見落としなどのポカミスも発生しやすい作業です。そこで、目視検査を行っていた工程に、素早く読み取れるハンディターミナルやコンベアライン上で自動読み取り可能なコードリーダ、コードの一括読み取りを可能とするRFID(Radio Frequency Identification)など、機器や装置を導入することで、各工程での照合作業の自動化または半自動化が可能となります。これにより、大幅な省人化を図ることができると同時に、誤出荷などのミスも防げます。さらに、人員を削減しながら負荷(作業量)に対する能力(キャパシティ)の均衡化を図ることが可能です。
こうした機器や装置を使った照合作業は、目視とは比較にならないほど正確で迅速です。そして、これらは取り扱いが容易または不要(自動)であるため、使用者の技術や経験を問いません。そのため、人員配置の自由度も大幅に向上します。
「ムリ」の解消 | 物流工程の省人化に貢献しながら、負荷と能力の均衡化が図れる。 |
「ムダ」の解消 | 検品作業・送り状と現品の確認作業の非効率を解消。ミスも防ぐ。 |
「ムラ」の解消 | 経験の浅いスタッフでも照合作業ができるから人員配置の適正化が図れる。 |
在庫管理でのハンディターミナル・コードリーダ・RFIDを使った改善
在庫管理にハンディターミナルや固定式のコードリーダ、RFIDを導入することで、注文時にすぐ在庫状況を照会でき、在庫管理の精度が格段にアップします。これらの機器やシステムを使えば各種データの管理が容易になるほか、手書き伝票なども不要になるので入力・記載の工数が不要になり、記載ミスも防止できます。ハンディターミナルやコードリーダ、RFIDを導入することで在庫管理の工数が削減でき、空いたリソースを他工程にまわせるので人員配置の最適化にも効果的です。
- 機器で管理できる在庫データ(ハンディターミナルの例)
-
- 入力するデータ
- 担当者コード(誰が)
- 入庫 or 出庫
- 向け先(どこへ)
- 商品コード(何を)
- 数量(どれくらい)
- 得られるデータ
- 処理日時
- 入出庫データ
- 数量不足品の抽出
- データの展開用途
- 棚卸し
- ロケーション管理
- ピッキング作業
下記のページでは、各機器の導入による改善事例などを紹介しています。
出荷検品でのハンディターミナル・コードリーダ・RFIDを使った改善
従来は、目視検査によって出荷検品を行っていたため、出荷ミスとその回収作業が生じるリスクを避けることができませんでした。しかし、荷物をバーコード/2次元コードで管理し、ハンディターミナルやコードリーダ、RFIDといった機器で読み取ることで、目視検査にかかっていた工数を削減でき、出荷ミスの発生も抑えられます。作業員への負荷が減りリソースに余裕ができるため、人員配置の自由度が向上し能力を最大限に発揮できます。
- 機器を使った出荷検品(ハンディターミナルの例)
-
- 入力するデータ
- 担当者コード(誰が)
- 入庫 or 出庫
- 向け先(どこへ)
- 商品コード(何を)
- 数量(どれくらい)
検品データはパソコンに出荷履歴管理される - 得られるデータ
- 商品数量のチェック
- 出荷先の照合
- 梱包不足品の確認
- データの主な用途
- 在庫管理
- 出荷ラベルの打ち出し
- 入庫検品
下記のページでは、各機器の導入による出荷検品の改善事例などを紹介しています。