KV-8000シリーズ
お客様導入事例京セラ株式会社
国分工場
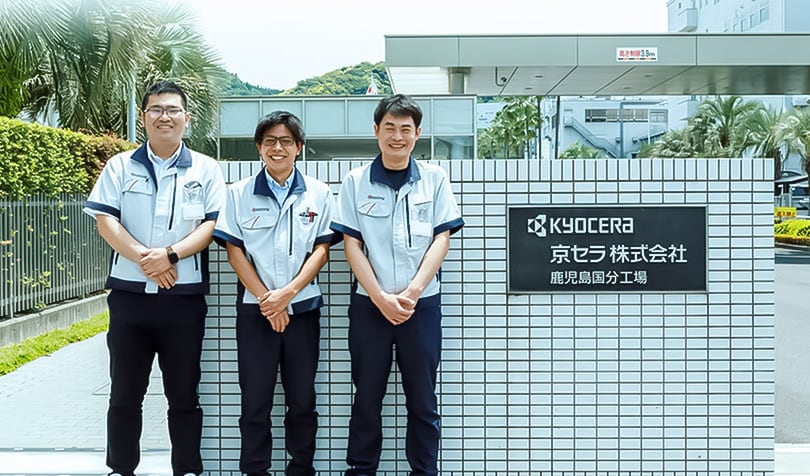
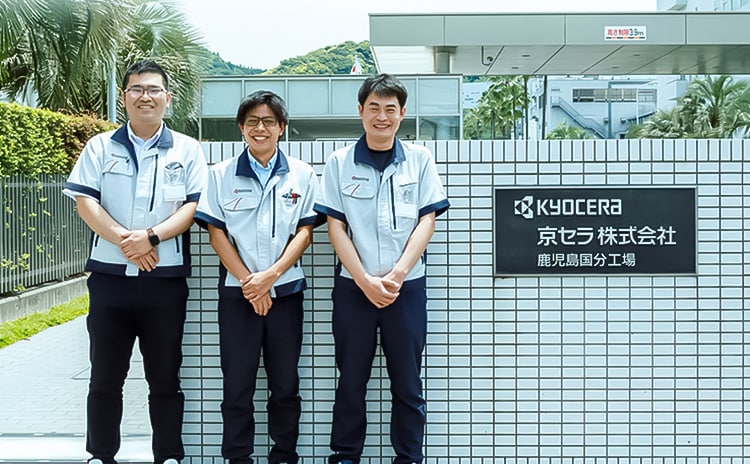


品質改善でも、トラブル解決でもKVシリーズが活躍。
長年苦慮していた不良項目の大幅改善を実現!
安定生産を実現させるためにKVシリーズを標準仕様へ。
KV-8000シリーズ ご採用理由
- さまざまなメーカのPLCと繋がる接続性
- トラブルを解決できるドライブレコーダ機能
- 設備の不調を捉えるデータ活用ユニットKV-XD02
お客様の声
「操作感が良く、期待以上に簡単にデータ収集の実現やドライブレコーダ機能の活用ができました。」
「遠隔デバッグや、予兆保全をKVシリーズの活用でこれから実現していきます。」
「高い提案力があるため、安心して相談ができます。」
― 京セラの国分工場では、どのような業務をおこなわれているのでしょうか?
国分工場では、インクジェットプリンタのヘッド部分を一括で生産している他、自動車部品、半導体部品、CMOSセンサ向けのセラミック製品、コンデンサなど、多種多様な製品の生産工程を担当しています。
我々が所属するインクジェット事業部で作っているプリンタヘッドは、京セラのセラミック技術を活かした製品となっていて、主に企業向けの産業用のプリンタに使われています。
― KVシリーズの活用概況を教えてください。
期待以上に簡単にデータが収集できました。
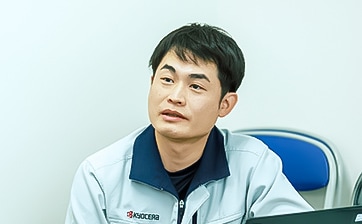
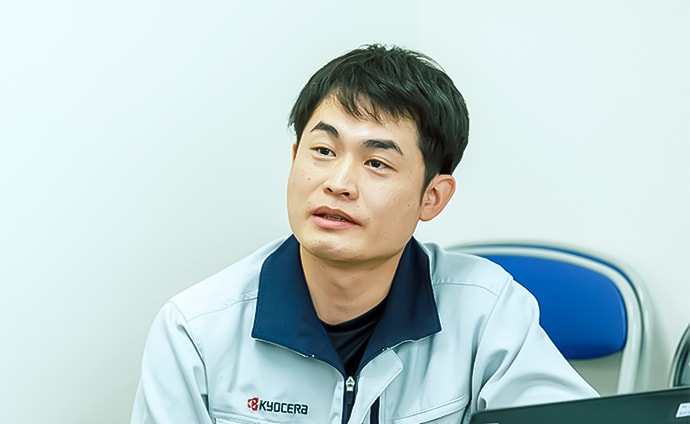
既存の設備に後付けするエッジPLCとして、また設備の制御PLCとしても活用しています。
エッジPLCでは、稼働中の生産設備からデータを収集・紐付けして社内サーバにcsvファイル形式でアップロードしています。
品質に影響が大きいところから優先的に取り付けていて、全設備の4~5割程度に設置が完了しています。
また、制御PLCとしては、新たに導入する際にはKV-8000を使用してもらうようにお願いしています。
― KVシリーズの導入はどのような経緯だったのでしょうか?
数年前より、京セラ全体の方針として、品質改善の取り組みに一層注力しています。
ワークのロットナンバーごとの工程通過時間や作業者情報との紐付けは手入力ですでにできていましたが、品質を改善していくためには、エア圧や製造条件など設備内のデータも紐付けていくことが必要と考えていました。
稼働中の設備から収集・紐付けする方法が課題になった際に、メーカや新旧の型式問わず、さまざまなPLCからデータ収集可能なPLCリンク機能が搭載されているKVシリーズが候補にあがりました。
本当にデータが簡単に取れるのか、また使い勝手や性能に問題がないかわからなかったので、まずは1台導入して、検証機として使ってみました。
具体的には、ちょっとした制御BOXを製作し、持ち運びながらいろいろな生産設備に繋げてみたのです。
― 実際に使ってみて、データ収集はスムーズに進みましたか?
かなりスムーズにテストが進み、本運用への採用が決まりました。
設備制御PLCのラダーを変更すると、問題なく稼働している設備に、不具合が生じる可能性があります。
KVシリーズは、相手PLCのラダー修正は不要で、KV側の簡単な設定のみでデータ収集ができます。
そのため、容易に設備から品質に関わるデータを収集でき、上位サーバにアップする仕組みまで簡単に構築できました。
結果として、データ収集した後の、“どの項目をどう解析し、どのように見せていくか”という活用手法の検討と実現に多く時間を割くことができました。
― データの活用効果を教えてください。
収集した次のステップとして、見える化に取り組みました。
収集したデータを、社内BIツールの「MotionBoard※」を使用して、ワークの位置合わせのズレ量などの品質データや、不良項目の推移を、現場の大型モニタからいつでも見えるようにしています。
その結果、作業員が良品率への影響を自身で考え、意見の発信や職務の工夫に取り組んでいます。
ある工程では、1年かからず歩留まりを88%から93%まで改善できました。
以前は、品質トラブル時には、膨大な量のExcelデータから該当ファイルを探して、そこから対象品種を絞ったり、グラフで可視化するなどの工数がかかっていました。
今はその場ですぐに確認できるようになり、その場で改善できるようになりました。
これからは「SPC管理(統計的工程管理)」の実現に向けて、どんどんバージョンアップしながら、現場が活用できる仕組みの構築を進めていきます。
※ウィングアーク1st 株式会社
― KVシリーズを実際触ってみてのソフト面の評価をお聞かせください。
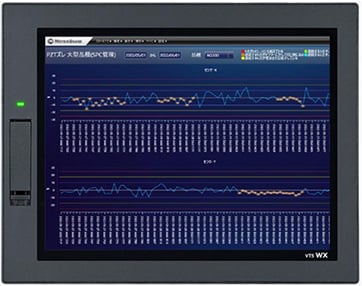
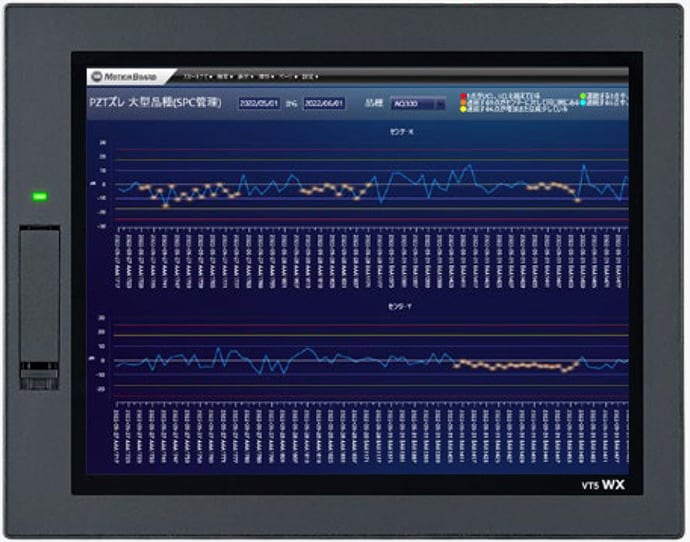
▲活用例
位置合わせのズレ量の傾向をリアルタイムで監視して傾向変化にすぐ気付ける。
それまでは他社製のPLCを使用していたため、最初は違和感がありました。
しかし、他社のデバイス表記に合わせる表示モードやマニュアルを見なくても、ある程度操作できる直感性ですぐに慣れました。
たとえばユニット設定をおこなう、ユニットエディタです。
KVシリーズでは、視覚的にわかりやすいため、各ユニットの設定がすぐに終わります。
他にも、使っているうちに他社にはない便利な機能が搭載されていることにも気づいて活用しています。
また、営業の方のサポートにも助けられました。
困ったことがあったらすぐに電話やメールで相談をさせていただいており、いつでもレスポンス良く対応してくれています。
本当に基礎的な質問も丁寧に教えてくれるので、新入社員や若手社員も安心してKVを触れるようです。
以前は設備制御のPLCは他社メーカで統一していましたが、前述した収集用での活躍や、使い勝手の良さ、営業サポート面から設備PLCとしても採用することを決めました。
― KVシリーズを設備採用するにあたって懸念はありましたでしょうか?
装置を製作する装置メーカ様の中には、最初はKVシリーズの採用に難色を示したところもありました。
しかし実際に使用いただいた際に、それまで使用していたPLCの時と変わらないリードタイムで装置を納入してくれました。
憶測ではありますが、プログラムを触ることが少ない私たちでも使いやすいと感じるため、本職の人たちであれば全く問題なく使用できたのではないでしょうか。
― KVシリーズの最新CPU KV-8000のドライブレコーダ機能の活用状況について教えてください。
KVシリーズのソフトはバージョンアップごとにどんどん便利な機能が増えていて、機能の活用が楽しみになっています。
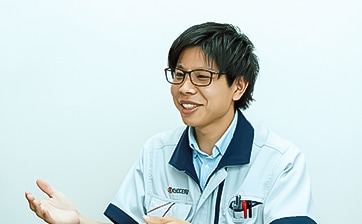
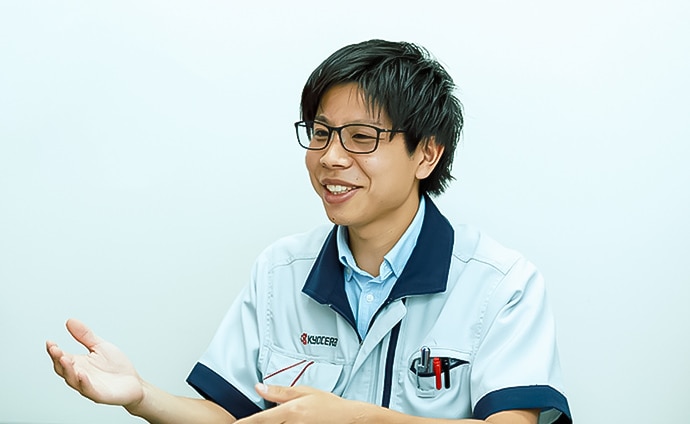
活用中の設備では、トリガ前後120秒のカメラ映像とラダーの記録を保存するように設定しています。
実際に、トレイ同士が衝突するという不具合が発生した時にドライブレコーダ機能を活用して解決した例があります。
記録したデータを使用して、自分たちで原因を突き止め、データを装置メーカ様に見せながら、「ここにインターロックを付けて欲しい」という形で依頼して修正対応しました。
通常だと1日はかかるようなトラブルを数時間で解決できました。
― 実際に活用している中で、ドライブレコーダ機能の利点はどこにあると感じましたか?
最終的には現地に行かずオンラインで解決できるのが理想ですね。
下記の3点があげられます。
再現待ちの必要がない
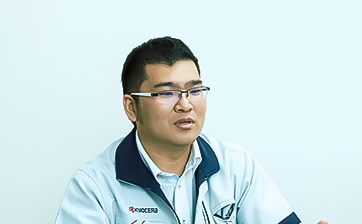
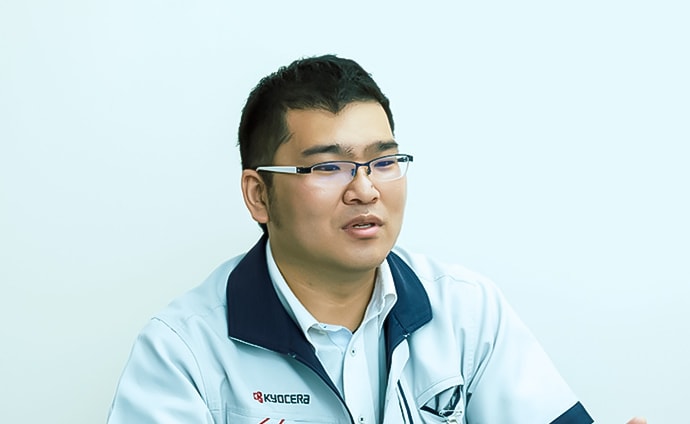
今まではトラブル発生後、発生条件の追究のために再現待ちする必要がありました。
再現性が低いものだと一旦様子見してまたそのうち再発...というイタチごっこがありました。
ドライブレコーダ機能は、トラブル前後のラダーと映像が残るので、再現待ちが不要です。
これだけでも、かなり工数が削減できます。
分析が容易
過去には、憶測でプログラム修正をしないといけないケースがありました。
直らない場合は、再現待ちと修正を繰り返す必要があります。
ドライブレコーダ機能は、記録した動画とラダーが連動して、何度でも繰り返し見れるため、トラブル要因発見までの時間が短くなります。
まだ経験やノウハウが少ない新人でも、原因に着実に近づいていくことができます。
トラブルが起きても、「ドライブレコーダ機能があれば、解決できる」という安心感を持って対応できます。
遠隔地との情報共有がスムーズ
トラブルが発生すると、装置メーカ様に連絡するのですが、口頭だとなかなか伝わりづらいケースがありました。
今は、ドライブレコーダ機能で保存したデータを送ることで、状況共有がスムーズになっています。
― 今後のドライブレコーダ機能の活用展開に関してはどう考えていますか?
これから導入していく設備のデバッグ・立ち上げ期間にも活用したいです。
「どういう現象で発生しているんだろう?」という不具合がデバッグ・立ち上げ期間は発生しがちです。
ドライブレコーダ機能を活用することで、不具合が1つ1つ着実に解決されて立ち上げ時間の短縮化に繋がると思います。
また、協力会社様のラインにもKV-8000を導入していきたいです。
協力会社様でトラブルが発生した時は、私たちが対応するのですが、今は往復の移動時間と解決を図る時間で丸1日ほどかかっています。
その点、ドライブレコーダ機能があれば、現地での作業時間を大幅に減らせるので、半日かからずに解決できると想定しています。
― データ活用ユニットKV-XD02の活用状況について教えてください。
まだ導入したばかりで、手始めにパラメータの上限、下限を超えたら異常判定してくれる「波形上下限監視機能」を使っています。
― KV-XD02に期待することは何でしょうか?
予兆保全による安定生産です。
後追い解析の仕組みは整ってきましたが、より高品質な商品を安定して生産するには、より早く設備の不調を捉えることが必要と考えています。
KV-XD02の生産条件の変化をリアルタイム監視する「兆候監視機能」や、「いつもと違う分析機能」の活用で、隠れている不調を発見し、未然に不具合を防ぐことができ、安定生産に繋がるのではないかと考えました。
私たちですべてのデータを常に監視し続けるというのは現実的に不可能なので、自動的に全部の信号を監視・解析してくれる「いつもと違う分析」機能には、とても期待しています。
「トレイ衝突トラブル」
通常時と異常時で本来下がっているはずのステージが上がってしまっていることが一目でわかり、さらに当時のラダーと映像を連動再生させることでインターロックミスの原因追究が早くできた。
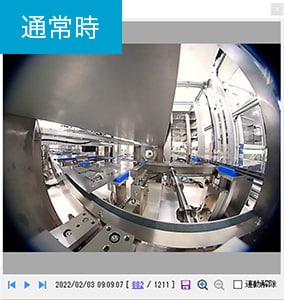
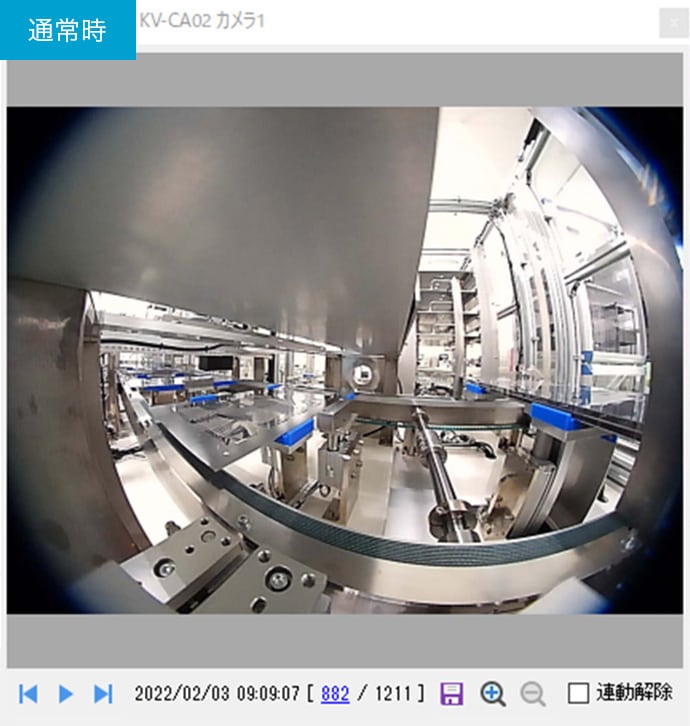
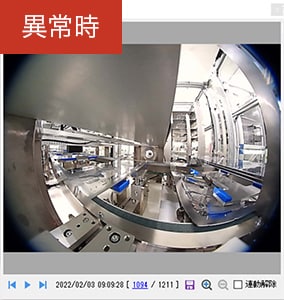
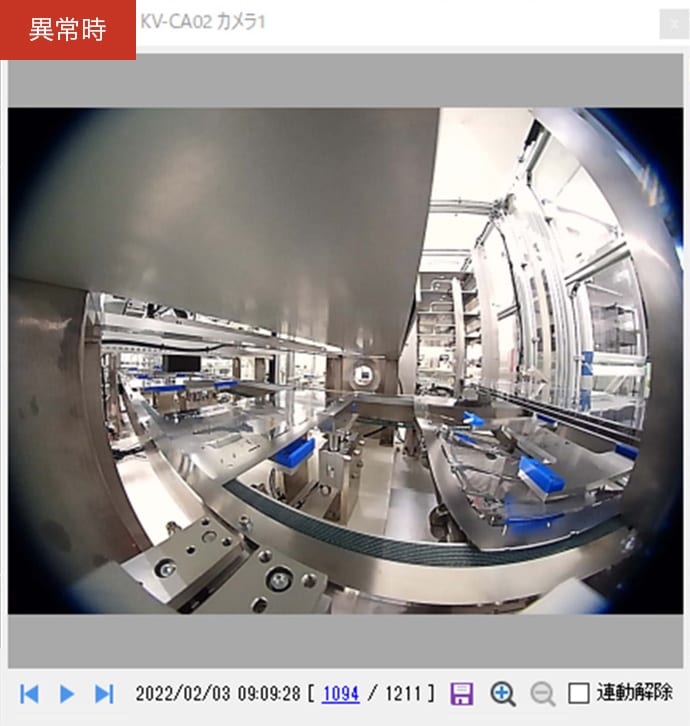
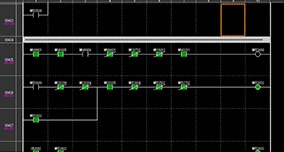
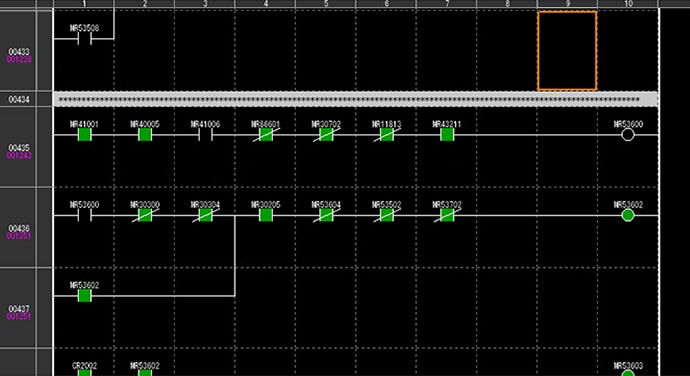
※お客様情報のため、デバイスコメントは修正処理しています。
― キーエンスの良かったところは他にありますか?
特に次の2点が良かった点です。
提案力が高い
相談した際に、できる、できないの回答だけではなく、できない場合には私たちのやりたいことを上手く聞き出して、「だったらこの方法があります」「このパッケージならできます」など、いろいろな提案をしてくれます。
私たちがやりたいことを先読みした提案をくださる点は、評価しています。
たとえば、ロットナンバーごとの工程通過時刻の入力を、自動化したいと検討し始めていた際に、相談する前に営業の方から自動化の提案をしてくださり驚きました。
意見・要望を製品に反映
私たちの意見や要望を受け入れて、製品に反映してくれる点も良かったです。
以前、温度の波形をバンド監視する機能がKV-XD02に欲しいと要望したところ、後にその機能が実装されたということがありました。
ユーザ側の意見も真摯に聞いて、時には取り入れてくださるメーカは安心できます。
― 今後の国分工場、インクジェット事業部での展望をお聞かせください。
KVと自社システムを組み合わせて活用して、品質改善とトラブル解決、安定生産への取り組みを継続的に注力していきます。
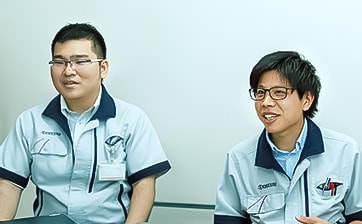
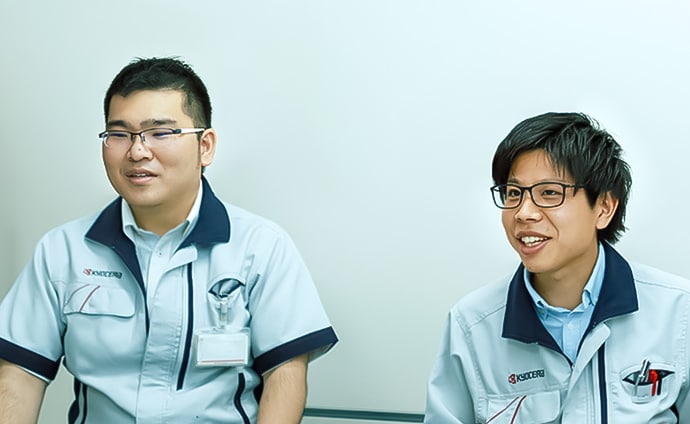
まずデータ収集に関しては、最終的にすべての設備からデータを取って管理していくことを最終目標としているので、引き続きKVシリーズの導入を進めていく予定です。
また工程の自動化も随時進めていて、今後導入する生産設備には、KV-8000とKV-XD02のセットを標準仕様として導入する構想を立てています。
製品の出来栄えについてはデータ収集したのちにMotionBoardで解析・監視、トラブル発生時はドライブレコーダ機能で解決、設備の変化はKV-XD02による予兆保全を実現という形で、上手く活用していきたいですね。
キーエンスにはその構築・運用においての手助けや、困り事に対する提案などを、引き続きお願いできればと思います。
関連商品
全国各地に工場や営業所を構える他、海外にも拠点を展開。
電子部品や半導体部品、セラミック製品、情報機器、通信機器など、多彩な部品や機器の製造・販売をグローバルな規模で展開しています。
- この事例に記述した数字・事実は、事例取材当時に発表されていた事実に基づきます。
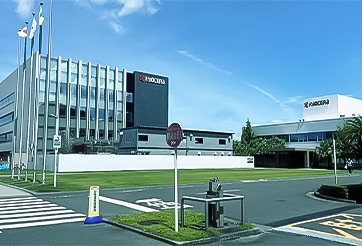
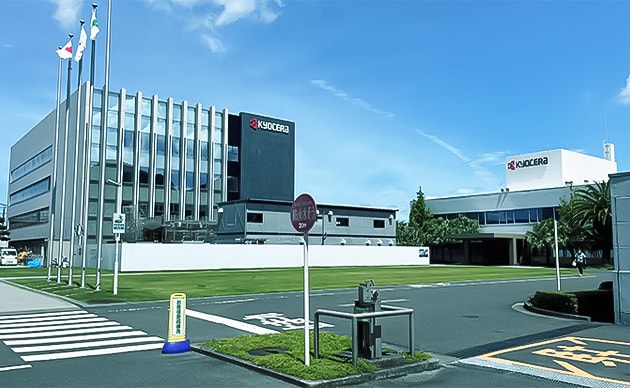
ほかのカスタマーボイスを見る