KV-8000シリーズ
お客様導入事例株式会社豊田自動織機
共和工場

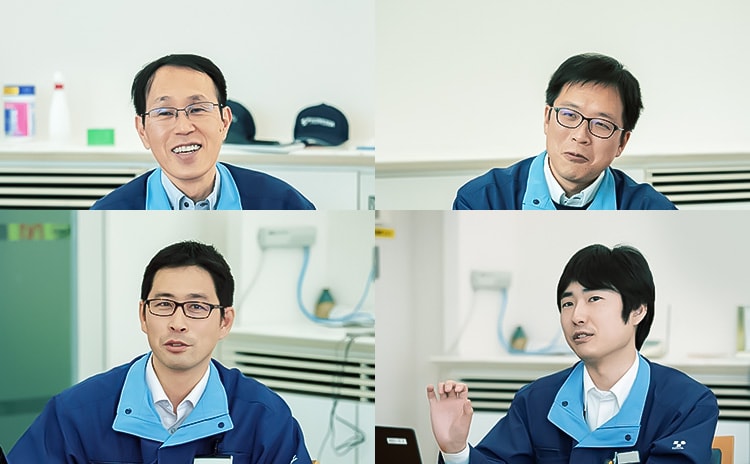


新規事業の電池生産ラインでKV初採用。
ライン稼働までに発生したさまざまな問題解決に大きく貢献!
KV-8000シリーズ ご採用理由
- ドライブレコーダ機能
- CPU処理速度の高速性
- 充実したサポート体制
お客様の声
「ソフトの使い勝手が使う側の目線に寄り添っている。」
「仕事の効率が従来と比べて大幅に向上し、制御設計者を中心に働き方が変わった。」
「キーエンスの営業は真摯なサポート対応で頼れる存在。」
- 豊田自動織機の共和工場では、どのような業務がおこなわれているのですか。

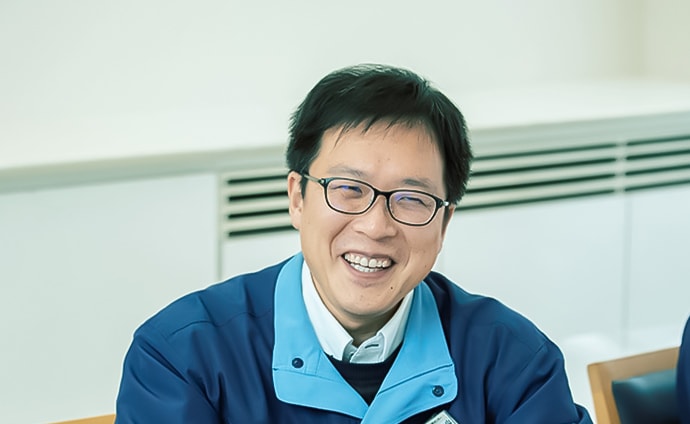
共和工場は大きく5つの部門で構成されています。
「生技開発センター」、「エレクトロニクス事業部」、「ダイエンジニアリンググループ」、「技術・開発本部」、そして近年新設されたハイブリッド車用の車載電池を生産する「電池事業室」です。
KV-8000シリーズの導入に関わっているのは、国内外の拠点向けに生産設備を作る「生技開発センター」です。
ここでは生産設備を作るほか、新たな生産技術の開発にも取り組んだり、さまざまな部署や業種の従業員たちと技術的な連携をおこなったりしています。
- KV-8000シリーズの稼働状況を教えてください。
「電池事業室」の生産ラインの制御PLCとして活用しています。
電池部品の組み付け設備に6つ、中間搬送の設備6つにそれぞれ1台ずつ、計12台が導入されています。
- KV-8000シリーズを導入するに至った経緯を教えてください。
電池の生産ラインを製作するにあたって、大規模な設備を高速に制御できるPLCが必要でした。
具体的には50軸以上のサーボモータを10ms以下のスキャンタイムで制御できることが条件でした。
また、今回はリードタイムがとても短く、短納期で確実に立ち上げることが使命でした。
要求を満たしてくれる製品を探した結果、既存設備に導入しているPLCと同じ会社のハイスペック機とキーエンスのKV-8000シリーズという2機種が最終候補に残りました。
さらにそこから、KV-8000シリーズを選んだ決め手になったのは、ドライブレコーダ機能の存在でした。
不具合や異常が起こった時の原因究明のほか、設備情報の収集にも役立ってくれる機能がKV-8000に搭載されていることは以前から知っていました。
この機能が今回の短納期での立ち上げで使える有効なツールではないかと思い採用しました。
- 初めて使用するメーカのPLCを採用することに不安はありましたか?
過去から使用しているPLCメーカをそのまま使い続けるのが当たり前だったのでKV採用は挑戦でした。
もちろん、ありました。
本当にスペックどおりの性能があるか、機能が使えるかなどは、実際に動かしてみないとわかりません。
過去から使用してきたPLCメーカをそのまま使い続けるということが当たり前だったのでKV-8000シリーズの導入は生技開発センターとしても挑戦してみる思いで始めました。
しかし、直感的でレスポンスの早い操作感や、期待していたドライブレコーダ機能の活用、何よりも不明点や問題があった際の営業の方と技術サポートのバックアップがあったため開発を進めることができたのです。
それどころか、本当に約半年で設備を立ち上げて生産まで持っていくことができました。
これは従来のPLCの使用では考えられないリードタイムですね。
- KV-8000シリーズを導入してみて良かった点を教えてください。
ラダーソフト設計の経験がある方なら、他社からKV-8000に変わっても大きな支障はないかもしれません。
実際に生産ラインを立ち上げてみて感じたKV-8000シリーズの魅力は、次の2つになります。
ユーザー目線に寄り添ったソフトの使い勝手
ラダーソフトKV STUDIOは細かい部分まで心配りされた、使い勝手の良さが魅力です。
例えばサーボコントロールの設定をするとなったら、通常だと領域やポジションをひとつひとつコメントを付けながら設定していくところから始めなければなりません。
その点、KVSTUDIOでは、あらかじめ汎用的な設定が準備されているので、細かな設定を飛ばして、座標やどう動かしたいかを決めるだけで完了してくれます。
もちろん自由にカスタマイズすることもできる懐の深さもちゃんとあります。
「リアルタイムチャートモニタ」を使う際も、アドレスをドラッグ&ドロップで設定できたり、コメントから文字列検索で探せるのが良かったです。
これらは一例で、ユーザー目線で作りこまれた機能や操作性の良さがあるソフトになっています。
またソフト自体の軽さとレスポンスの早さも高く評価しています。
そこまでスペックが高くない事務用PCでもきびきび動いてくれます。
そのためKV STUDIOを操作していて大きなストレスを感じたことはありません。
ユーザーへの細やかな配慮に対して、凄く熱い思いが込められているなと感じます。
圧倒的に短時間で問題解決を図れる

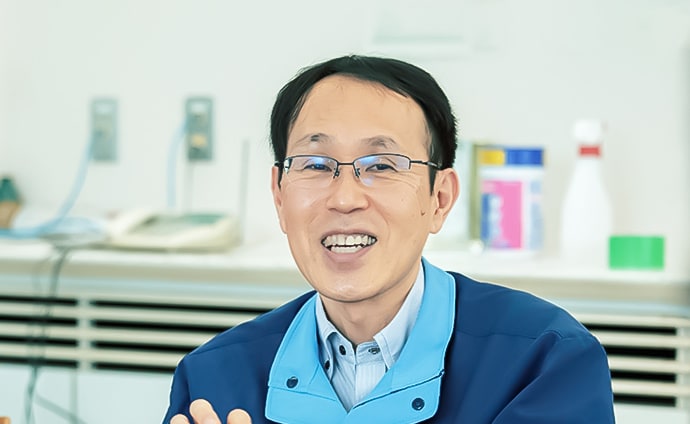
発生した問題を、短時間で解決できる点は良かったですね。
KV-8000の機能である、トラブル前後の設備データをすべて残せる「ドライブレコーダ」とデバイスの状況を波形で確認できるKV STUDIOの機能「リアルタイムチャートモニタ」を併せて使っています。
なにか不具合が起きた時には、そのタイミングの設備情報を見返すことで、どの信号が立っていなくて、どの数値データが異常だったかなど、原因を確実に把握できるのです。
操作性が簡単なため、メカ設計の人もPCにソフトをインストールして、タクト詰めの作業時などに使用しています。
同じ事業部内なら何人でも無償でソフトのインストールが可能なところも嬉しいですね。
今までは問題が発生した場合、勘や経験で問題箇所のアタリを付けて、その仮説に基づいてトライ&エラーを繰り返しながら対処していくしかありませんでした。
またカメラで録画して、不具合が再現されるまで待つようなこともしていました。
そうした作業がまったく必要なくなり、事務所でデータを見ながら問題解決を図れるのは大きいですね。
お陰で、これまで発生した設備トラブルは確実に解決できました。
- ドライブレコーダ機能はどのように使っていますか?


タッチパネル上に保存スイッチを配置。
だんまり停止時は必ず押してトラブル前後数分間のデータを記録している。
※一部ぼかし加工をいれております。
通常のトラブルは、アラーム信号をトリガとして前後のデータを保存していました。
トラブルが起きても設備はすぐに再稼働させ、事務所で並行して保存したデータを解析しています。
また、だんまり停止が発生したときもデータ保存できる運用にしています。
設備のタッチパネルのメイン画面には大きく「記録ボタン」を設定しており、なにかあった時は誰もがすぐにそのボタンを押せるようにしています。
現場の人は最初押すのを躊躇していましたが、ドライブレコーダ機能でトラブル解決できるとわかってからはだんまり停止が発生したら、まずスイッチを押してくれるようになりました。
- ドライブレコーダを活用することで、不具合解消に役立てられたというお話がありました。
その具体的な事例を教えてください。
以前はトラブルの再発待ちと原因追究で、夜中まで設備に張り付いて解析をしていました。
ドライブレコーダを使って不具合解消した事例を3つ紹介します。
事例1RS-485通信の遅れによる異常発生
これは、KV-8000シリーズとヒータの温調器のシリアル通信で起こった不具合です。
ヒータ温調器にオーバシュート対策で目標温度を書き込むようにしたら、設備が異常で止まるようになりました。
そこでドライブレコーダを使って止まっているタイミングを調べてみたところ、書き込みタイミングを増やしたことで、ステータス情報を抜くサイクリック通信が少し遅れてしまっていたのです。
そのため情報が更新されずに、異常ではないのに、異常と判別してしまっていました。
本来は問題ない事象でしたので、遅れても異常だと判別しないようにすることで解決できました。
ドライブレコーダ機能で異常発生前後の通信状態を記録し、リアルタイムチャートモニタで確認。
PLCと温調器はRS-485通信で更新していたが、ヒータ電源がONしてから、温調器からのステータス読出が遅れたことで、温度計異常(設定温度未達異常)が発生していることが判明。
詳細に見ていくと、目標温度を設定するイベント通信が実行された際に、サイクリック通信のステータス読出が遅れることが原因とわかった。


事例2センサのチャタリングによるだんまり停止
PLCの経験によるスキル差をドライブレコーダ機能は埋めてくれます。
私1人で12台の設備のトラブル対応をしています。
1. ドライブレコーダでだんまり停止前後のラダーの状態を確認


何度も繰り返し確認できる。
また、すべてのデバイス情報が記録されているため、あたかも当時にさかのぼってモニタをしている場合と同様の使い勝手で要因を追っていくことが可能。
2. 関連する信号をリアルタイムチャートモニタで確認


トラバーサツメ開閉のセンサ信号のチャタリングによりトラバーサの動作条件がOFF。
トラバーサの移動途中でOFFになったためだんまり停止が発生していることがわかった。
事例3サイクルタイム遅れ
制御トラブルは原因が目に見えにくく、難解なケースが少なくないのですが、ドラレコ機能のおかげで気持ちが楽になりました。
1. 自作のサイクル見える化画面で確認


“あるライン”の信号が目標タクトに入らないばらつきが発生していることがわかる。
2. サイクルオーバーが発生した前後の関連する信号を保存された運転記録で確認


前工程からの信号が入らず、ロボットサイクル2の開始条件が揃わなかったためロボットサイクル2に移行せずにサイクルタイムオーバーが発生。
Tips.豊田自動織機様で今後活用予定
データ活用ユニットKV-XD02は、プログラムレスでサイクルタイムや機器動作時間の見える化ができます。


WEBブラウザで設定


デバイスを設定するだけですぐに見える化
- ドライブレコーダがなかった頃は、問題解決にまで至らなかったこともあったのでしょうか?
もうドライブレコーダ機能がなかった時の働き方には戻れません。


ありますよ。
トラブル1つ1つに、通信異常や後工程の影響、センサのチャタリング、故障など、想定される原因が多くある中で、すべてを解決していくことは到底不可能でした。
影響がそこまで大きくない問題については、異常が出た時の復旧方法をマニュアルにしてもらうなど、製造部門に対処を任せたものもあります。
ただKV-8000シリーズを導入していくと、解決できない問題も少なくなっていく気がします。
なので、ドライブレコーダが付いていない設備はあまり触りたくないですね。
また、KV-8000は私たちの工夫次第でさまざまな使い方ができると思いますので、色々な設備やシチュエーションで活用できることを今後模索していきたいと思っています。
- KV-8000シリーズの導入効果について教えてください。
まず、制御設計者の働き方に大きな変化がありました。
従来なら解析まで数日~1週間近くかかっていたような設備トラブルを、ものの数十分~数時間で解析できるようになりました。
それまでは人の経験によるノウハウでの解析が当たり前でしたが、KV-8000シリーズを導入してからはベテランの人だけではなく、誰もがデータで判断できるようになっています。
圧倒的に解析の効率が上がっているため、その分の時間をどうしたら再発しなくなるか、類似トラブルが起きなくなるかを考える時間が増えました。
また、ドライブレコーダ機能のデータを使うと、人への説明がしやすく、理解もしてもらいやすいため業務が円滑化しています。
さらに社員の意識も変わってきました。
以前までは設備が停まると、製造部門からのプレッシャーもあってネガティブな思いに囚われていました。
しかし今は必ず問題の原因究明に至れるため、データを基に話をすることができますし、心強く前向きに問題解決に臨めるようになりました。
そして、費用削減にも繋がりました。
電池の生産ラインには12台の設備が導入されています。
この規模のラインであれば、3~4名の制御スタッフが付くのが普通ですが、KV-8000シリーズなら手間が掛からないので1~2名で済みます。
1ヶ月20日稼働で、その分2名のスタッフが差し引かれることを考えると、導入3ヶ月で約120人日以上の削減を実現したことになります。
- 先日、データ活用ユニット・KV-XD02のテスト運用も始められたと伺いました。
どんな事に期待してKV-XD02の導入を考えられたのですか?
より素早いトラブルの発見と情報収集のツールとして期待しています。
KV-XD02のキャッチコピーにある「“いつもと違う”がわかる」を実現できると嬉しいですね。
定期的に監視して変化を見ることができるので、先ほど「事例3」で上げたサイクルタイムの変化にすぐに気づけますし、原因追究のための労力もほぼなくなりますから。
WEBサーバ機能を使ってのIoT化が簡単にできる点も魅力ですね。
現在、新開発ラインへの導入のために動いていて、そのラインの一部にKV-8000シリーズとKV-XD02をセットで導入予定です。
- キーエンスの営業の対応に対する評価を教えてください。
いつも真摯に対応してくれて助かっています。
生産ラインの立ち上げは、トラブルが頻発するため、簡単なものではありませんでした。
しかし問題が発生した際に電話を掛ければ、いつでもすぐに対応してくれて、丁寧に教えてくださいます。
このサポートの力は我々にとって大きい存在でした。
ドライブレコーダ機能を活用でき、ラインが無事に立ち上がったのは、営業の方のサポートのおかげです。
- 今後の展望をお聞かせください。


KV-8000シリーズは、共和工場での導入を足掛かりとして、新開発のラインへの導入を検討しています。
またこれから高齢化が進み、労働人口が減っていくと、技術者の確保はどんどん難しくなっていきます。
PLCを扱う制御設計者の専門性という概念を切り崩し、誰でも比較的簡単にできることが、これからますます求められてきます。
KV-8000シリーズはその一端を担うツールとして発展していくことを期待しています。
関連商品
共和工場は、電池事業部室・生技開発センター・技術開発本部・エレクトロニクス事業部・ダイエンジニアリングの5つの主な部門で構成されています。
- この事例に記述した数字・事実は、事例取材当時に発表されていた事実に基づきます。


ほかのカスタマーボイスを見る