なぜ外観検査をするのか
外観検査は、不良品の流出防止に加え、製品品質向上にとって重要な役割があります。こちらでは外観検査の目的、外観検査を実施する際の流れなどをご説明します。
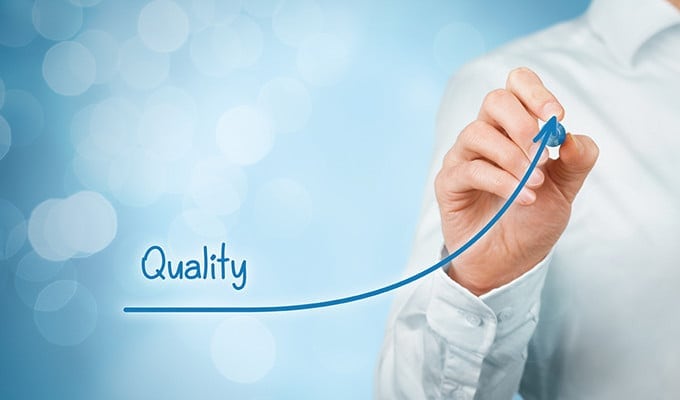
外観検査の目的
外観検査は、部品・製品の品質が規定値に適合しているか評価する工程です。そのため部品・製品の良否を判断し、不良品流出を防止することが目的になりがちです。しかし、外観検査の本来の目的は、不良が発生している原因を突き止め、不良発生を予防することです。検査工程で発見された不良とその発生原因などのデータを設計や製造などの関連部署にフィードバックし、不良品が発生しないように工程改善を図る一連の流れが外観検査の本質です。極端な話になりますが不良品の発生原因を特定し、対策することで「検査のいらないものづくり」を実現することが外観検査の真の目的と言えるでしょう。
外観検査で品質を保証する
部品・製品の品質トラブルが多く、検査工程を強化するという話をよく聞きます。「品質が安定しないから外観検査の人員を増員する」「検査員1人あたりの検査項目を増やす」というケースです。しかし、増員は人件費を圧迫しますし、検査項目の増加は検査漏れ・不良品の見逃しなどにつながる恐れもあります。結果的に品質を守るために強化した外観検査が生産効率低下・コスト高を生み出すこともあります。
外観検査は、品質保証のために行う工程であり、品質は設計・製造工程の改善によって向上します。そこで外観検査の情報を速やかにフィードバックし、設計・製造工程に活かすことが大切です。設計や各工程での作り込みを徹底し、不良品発生をゼロに近づけることができれば検査を簡易化でき、生産効率向上・コストダウンといった効果を生み出します。
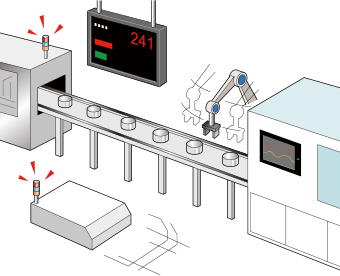
外観検査で品質を維持・向上させる
品質が向上すれば、限りなく不良品の発生をゼロに近づけることができます。こう聞くと「品質が向上すれば外観検査は不要になるの?」と感じる方もいらっしゃると思いますが、外観検査は品質保証のために実施するものなので別の話です。「品質が安定しているので検査していません」と納品先に伝えても納得してもらえないでしょう。また、品質を維持・向上させるために外観検査を継続することが重要です。次の項目では、外観検査の流れと継続する重要性をご紹介します。
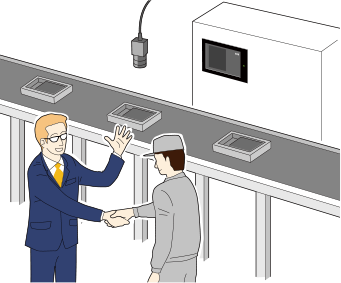
外観検査の流れ
外観検査は、目視による検査が基本となり、人間の五感のうち視覚によって行われます。その際に重要なのが「見る」「観る」「視る」「診る」「看る」という5つの「みる」です。部品・製品の良否を見極め、不良の原因を探り、設計・製造工程の問題点を探り、問題点の改善を図ることで不良品をゼロにするためにサイクルをまわしていくことが大切です。こちらでは5つの「みる」から外観検査の基本的な流れをご紹介します。
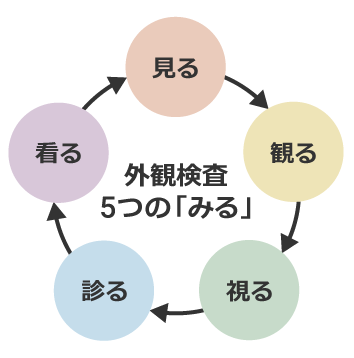
部品・製品の合否判定を行う「見る」
外観検査のファーストステップ「見る」では、部品・製品の外観形状や構造、寸法、色などを目視で確認し、限度見本と比較して合否を判断します。ただし、判断するだけでは選別なので、不良情報を収集・蓄積して設計や製造へフィードバックすることが重要です。
製造工程を確認する「観る」
「観る」では、「見る」から得た不良情報をもとに製造工程を確認し、不良品が発生する要因となる5M1Eの変化点と不良の因果関係を探ります。
- 【MEMO】 5M1Eから6M1Eへ移り変わるものづくりの現場
- 5M1Eとは、人(Man)・方法(Method)・測定(Measurement)・材料(Material)・機械(Machine)および環境(Environment)の頭文字を取ったもので、品質マネージメントを行ううえで欠かせない要素であり、不良発生の根本原因仮説を設定するときに重要です。また最近では、品質・価格・納期(QCD:Quality/Cost/Delivery)の目標を達成するために工場全体をコントロールする「マネジメント(Management)」を加えて6M1Eによる全体プロセスのコントロールが品質管理に求められるようになっています。
不良の発生・流出要因を調査する「視る」
「視る」では、収集・集計した不良品情報と製造現場の状況から不良発生の原因を調査します。
製造工程や組織の問題点を診断する「診る」
「診る」では、不良の発生・流出要因になっている製造工程の問題点、組織の課題などを総合的に調査し、不良が発生する根本的な原因を改善するために実施すべき方法を選択します。
製造工程・設計の改善を行う「看る」
「看る」では、「診る」で選択した改善策を実施します。まずは問題拡大を抑えるために応急処置を行い、次に根本原因の対策を実施。不良の根本原因が設計に起因する場合は、設計から見直して次の機種に改善を反映します。
外観検査の実施方針
外観検査では、5つの「みる」を行い、改善対策を実施し、その有効性を判断するサイクルをまわします。この5つのサイクルの中で製品品質の維持・向上を図り、最終的には不良品ゼロを目指します。
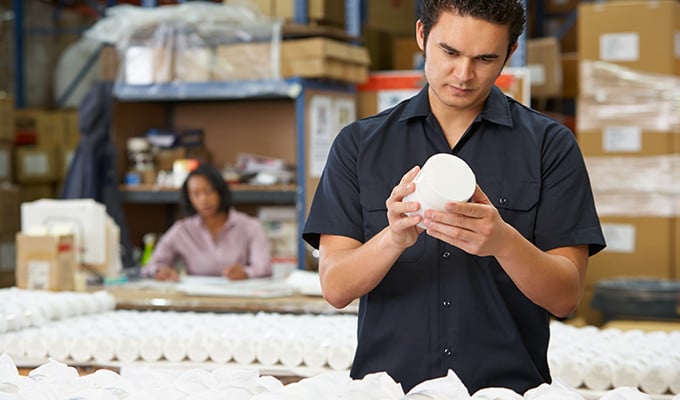
不良品がゼロになれば、外観検査にかかるコスト・手間の大幅削減につながります。品質は設計・製造工程で作り込むものとして捉え、実現するために手段のひとつとして外観検査を実施するとよいでしょう。
5つのサイクルをまわしながら品質が向上すれば、自然と外観検査の負担は軽減されてコストダウンにもつながります。その際に画像処理システムなどを導入して検査工程を自動化すれば、さらなる生産効率化・コスト削減につながり、外観検査の負担を削減できるでしょう。