シート/フィルムの穴あき、傷
シート/フィルムの穴あき・傷の検査について説明します。こちらでは、シート/フィルムの外観検査するうえで覚えておくべき基本的な知識、よく起こる不良の種類や発生原因、従来の検査方法と最新画像処理システムを活用した検査事例を紹介します。
製造の概要・基本
シート/フィルムについて
薄い膜状の素材を総称して「フィルム/シート」と呼びます。日本国内においては厚さ200μm以下のものを「フィルム」、それ以上のものを「シート」と呼ぶことが多いですが、明確に定義されているわけではなく、呼称はメーカーなどに委ねられています。材料も合成樹脂を使用したものから金属箔、紙や布など幅広く、食品の包装で目にする樹脂シート/フィルムにアルミなどを蒸着させたものなども多く流通しています。こちらでは、樹脂を原材料にしたシート/フィルムを中心に取り扱います。
シート/フィルムの製造方法
シート/フィルムの製造では、熱可塑性樹脂を薄く成形していく方法が一般的です。樹脂成形と同様に「溶かす」「成形する」「冷やす」という流れが基本になります。成形方法としては、「インフレーション法」「キャスティング法」「溶液流延法」「カレンダー法」などが一般的です。シート/フィルムは、上記製造方法に加え、圧延・印刷・ラミネート・裁断(スリッター)などの工程を行いますが、こちらでは基本的な製造方法を説明します。
- インフレーション法
-
押出機で溶かした樹脂を円形ダイで円筒状に成形し、チューブ状に連続で押し出します。その際に円形ダイ中央から空気を送り込み、膨張させながら徐々に所定の幅までフィルムの幅を広げます。冷却後、巻き取ってロールにします。最終的には円筒状のシート/フィルムが成形されます。
- A:原料
- B:押出機
- C:円形ダイ
- D:ニップロール
- E:巻き取り
- キャスティング法(Tダイ法、フラットダイ法)
-
溶解した樹脂をフラットなダイ(Tダイ)で平らに押し出して成形する方法です。溶解膜は、ローラーで急冷・圧延しながらロールにします。圧延などの別工程を行わない場合は、フィルム最大幅がTダイリップの長さまでとなりますが、生産性が高いことが特徴です。フラットなシート/フィルムに仕上がります。
- A:原料
- B:押出機
- C:Tダイ
- D:冷却ロール
- E:トリミング
- F:巻き取り
- 溶液流延法
-
溶媒に溶解させた原材料を加熱し、溶媒を蒸発させてシート/フィルムを成形する方法です。溶媒に溶解させた原材料を溶液(ドープ)と呼び、溶液をドラム(キャスティングドラム)や平滑ベルトの上に流し込んで付着させ、加熱することで溶媒を蒸発させてシート/フィルムを成形します。
- A:原料
- B:エアー排出口
- C:巻き取り
- D:エアー供給口
- カレンダー法
-
溶融状態に加熱した熱可塑性樹脂を複数のローラー(カレンダーローラー)で圧延しながらシート/フィルムを成形する方法です。複数のローラーで加熱または冷却しながら成形を行い、最終的に冷却して巻き取ります。主に塩化ビニル樹脂シート/フィルムの製造に用いられます。大型の設備が必要ですが製造能力が高いという特徴があります。
- A:原料
- B:カレンダーローラー
- C:巻き取り
よく起こる不良の種類と発生要因
シート/フィルムの製造でよく起こる不良の種類とその発生原因について説明します。
ピンホール
針で空けたような小さな穴をピンホールと呼びます。シート/フィルムは非常に薄いので突起物との接触、輸送中の振動による摩擦、折れ曲がりによるストレス、落下や衝撃などでピンホールが発生します。
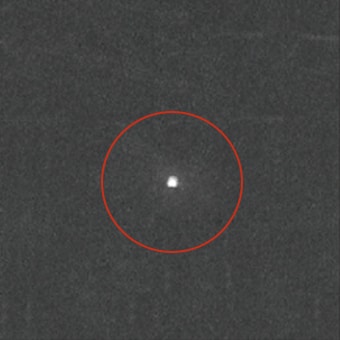
フィッシュアイ、ゲル、気泡(ボイド)
フィッシュアイは、樹脂の一部が周囲の材料と完全に混合せずにできた球状の塊です。ゲルは、熱硬化性樹脂が溶解する途中段階でゼリー状になる現象です。気泡(ボイド)は、内部に泡(空気)が残った状態で成形された不良です。フィッシュアイ、ゲル、気泡(ボイド)の発生要因は、ゴミ・チリの混入や成形不良などが考えられますが、微小なものは不良として判断しないケースもあります。

異物、汚れ
異物・汚れは、成形時にホコリ・チリが混入したり、搬送時にゴミ・油分が付着したり、さまざまな要因が考えられます。異物の混入・付着の原因はさまざまですが、静電気により付着してしまうこともあります。まずは侵入経路の特定が大切です。

ムラ、スジ、シワ、傷
ゴミの侵入、搬送時の接触や衝撃などにより、ワークにムラ・スジ・シワ・傷などが発生することがあります。まずは外観検査でゴミやホコリの侵入経路を特定し、静電気の影響でホコリ・チリなどが付着している場合は静電気除去装置の導入も有効です。

従来の検査方法
シート/フィルムは、検査範囲が広く、ピンホールのような微小な不良が多いため検査に手間がかかります。従来は、目視検査・汎用センサなどでの検査が中心でした。しかし、目視検査では高速化するラインへの対応が難しく、汎用センサでは微小な欠陥の検出が難しいという問題がありました。また、フィルムは透明なもの、光沢のあるもの、凹凸のあるものも多く、外部環境の影響を受けやすいので画像センサでの不良検出も困難でした。

最新画像処理システム検査事例
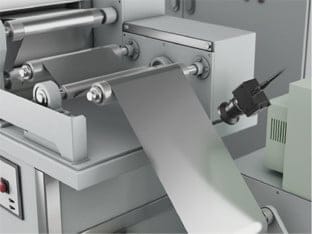

キーエンスの画像処理システム「CV-Xシリーズ」「XG-Xシリーズ」は、有効画素6700万画素(8192×8192)の大容量画像を高速伝送できるラインスキャンカメラをラインナップしているので、シート/フィルムのような検査範囲が広いワークの外観検査に最適です。従来、複数台のエリアカメラが必要だった検査を1台のカメラで対応できるようになりました。
また、ワーク表面の陰影や光沢の影響をキャンセルし、最適な画像に補正する「リアルタイム濃淡補正」を利用すれば、ワークの状態や外部環境の影響を受けずに、ピンホールのような微細な変化も確実に検出可能です。1台の画像処理システムで各種外観検査、寸法検査が実現でき、高速ラインに対応しているのでインラインで検査が可能です。最大限にラインの生産能力を引き出し、なおかつ検査工程にかかっていた手間・人件費削減につながります。
- リアルタイム濃淡補正
-
まとめ
このページでは、シート/フィルムの外観検査に必要な基礎知識や、トラブルと外観検査の方法についても紹介しました。それらをまとめると、以下の通りです。
- シート/フィルムは、検査範囲が広く、微小な不良が多いため検査に手間がかかる。
- ラインスピードが速く、反射光の影響もあり、目視や汎用センサでは検出が困難。
- キーエンスの画像処理システムなら、ワーク表面の陰影や光沢に影響されず、微小な不良も1台のカメラで自動検出できる。
ワークによって、外観検査の方法もさまざまです。最適な外観検査を行うには、それらの特徴を知り、正しく検査することが大切です。
このページで紹介した内容や、他のページに記載している外観検査の知識を1冊にまとめた資料「外観検査のすべて」は、下記からダウンロードできます。画像処理システムの導入事例集とあわせてご覧ください。