ネジ/ボルトの輪郭
部品を留める・連結する「ファスニングパーツ(Fastening Parts:締結部品)」として欠かせない「ネジ・ボルト」。自動車や家電、産業機械など広く利用され、ものづくりの現場はもちろん生活の中にも欠かせない部品です。こちらでは、ネジ・ボルトでよく発生する不良の種類、発生要因と検査方法、輪郭計測の一般的な検査方法と最新の画像処理システムを使った外観検査事例をご紹介します。
製造の概要・基本
ネジとボルトの違い
一般的にネジ山を切っている雄ネジ・雌ネジの総称を「ネジ」と呼び、その中でも頭部が四角形や六角形などの雄ネジを「ボルト」と呼びます。また、ドライバーで締め付ける小径(一般的には8 mm以下)の雄ネジを「ビス(小ネジ)」と呼ぶこともあります。これらに共通することは部品を留める・連結することに使用されることです。また、ネジ・ボルトは、ナット・ワッシャとセットでの使用が一般的です。
ネジ/ボルトの製造工程
ネジ・ボルトの製造には、頭部を成形する「頭部鍛造」、ネジ山部分を成形する「転造」、ネジ・ボルトに強度や粘り強さを与える「熱処理」、サビの発生防止や装飾として行う「表面処理」などの工程があります。
-
コイル材 -
頭部鍛造 -
転造 -
熱処理 -
表面処理
よく起こる不良の種類と発生要因
ネジ・ボルトは、塑性加工・鍛造加工・転造加工などによって大量生産が可能になり、コストダウンと精度向上を実現しました。しかし、完全に不良の発生を防ぐことは困難です。バリや割れ、欠け(クラック)、変形、寸法ズレなどの不良が発生すれば、締結部品としての機能を果たせないばかりか、そのネジ・ボルトを使用した製品の破損といったトラブルにつながります。こちらでは、ネジ・ボルトの製造工程における一般的な不良と発生要因をご紹介します。
バリ
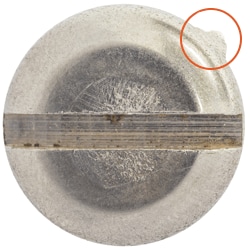
切削や転造などでネジ山を加工するときにバリが発生することがあります。特に切削加工でネジを切っていくときにバリが発生しやすく、通常は仕上刃(さらい刃)でバリを除去します。しかし、ネジ先端部などは仕上刃がかからず、バリが残ってしまうこともあります。バリは締め付けトラブルや振れの発生原因となります。
割れ・欠け(クラック)
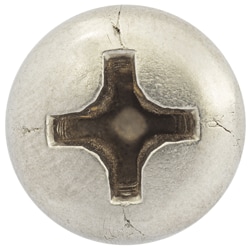
ネジ・ボルトの製造では、線材に塑性・鍛造・転造などの加工を行いますが、その際に割れや欠け(クラック)が発生することがあります。例えば頭部鍛造による材料割れなどが挙げられます。ネジ・ボルトは、形状やサイズ、材質や熱処理の有無により引張強さ・剪断応力などが規定されていますが割れや欠け(クラック)が発生すると強度低下・破断につながります。
変形・寸法ズレ
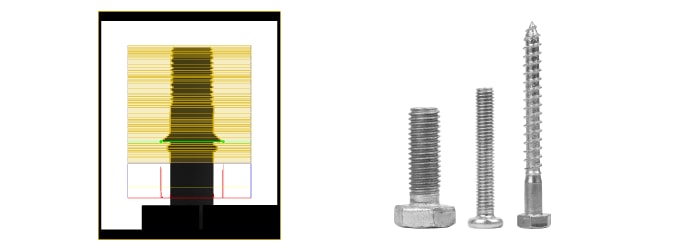
ネジ・ボルトは、JISやISOで寸法や形状、寸法公差が細かく規定されています。変形・寸法ズレは、各工程の加工精度や熱処理・表面処理の方法など、さまざまな要因が考えられますが寸法検査を実施することで流出を防げます。
異品種・未加工品の混入
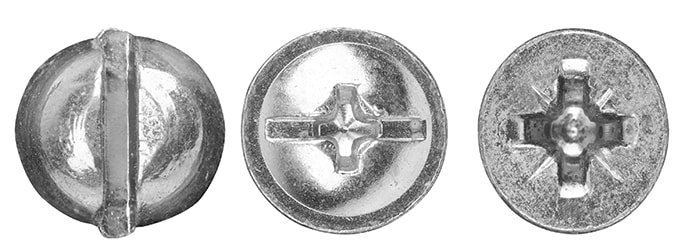
数種類のネジ・ボルトを同一ラインで製造する場合は、異品種や未加工品の混入にも注意が必要です。段取り替えでのチェック体制を整えることで異品種・未加工品の混入を防ぐことはできますが、微妙なピッチの違いなどは目視検査だけでは難しいのでピッチゲージや寸法測定機などによる検査が必要です。
従来の検査方法
ネジ・ボルトは、規格品であればISOやJISにより寸法や公差が細かく規定されています。ネジ・ボルトの検査では、外観のほかに機械的性質を測定する「引張試験」、熱処理や表面処理の検査なども行いますが、こちらでは外観検査に絞って一般的な検査項目を紹介します。
寸法検査
寸法検査で最も簡単な方法がノギスやマイクロメータによる測定です。ノギスやマイクロメータによる寸法検査は、特別な装置が必要ないので手軽な反面、測定者によって誤差が生じやすく、手作業なので手間・時間がかかるというデメリットがあります。キーエンスの画像センサ「CV-Xシリーズ」/画像処理システム「XG-Xシリーズ」なら最大5000点の多点計測で、ネジ・ボルトの寸法をインライン上で素早く・正確に検出可能です。
ピッチゲージ検査
ネジ・ボルトのピッチ形状を検査する代表的な測定器がピッチゲージです。対応した寸法のゲージをネジ山に当てて隙間がないかチェックすることでピッチ形状を検査します。ピッチゲージもノギス・マイクロメータ同様に手軽に導入できる反面、手間・時間がかかり、測定者による誤差が生じやすいというデメリットがあります。キーエンスの画像センサ「CV-Xシリーズ」/画像処理システム「XG-Xシリーズ」なら複数のエッジ情報を一括処理し、最大・最小・平均のデータを算出可能なのでピッチも正確に検出可能です。
限界ゲージ検査
ネジ・ボルトの寸法は、寸法公差が規定されています。この寸法公差内にピッチ形状が収まっているかを検査する測定器が「限界ゲージ」です。寸法公差に沿った形状のネジ山を持ち、通り側と止まり側がセットになっています。
顕微鏡検査
より精密な検査を行う場合は、光学顕微鏡と精密可動テーブルを組み合わせた測定顕微鏡を使用します。測定顕微鏡による検査は、拡大してネジの外径や内径、有効径、ピッチやネジ山の角度などを非接触で高精度な検査が可能です。ランダムで抜き取り検査をする場合とパーツフィーダなどに組み込んで全数検査する場合があります。
ネジ・ボルト専用検査装置による検査
寸法検査や外観検査、寸法検査、ピッチ検査、ねじ込み試験、ネジトルク試験などを行う専用検査装置もあります。検査装置によって対応可能な検査内容などは異なります。専用検査装置は、製品の仕様や生産ラインの変更などが発生した場合に手間・費用がかかることもあります。
最新画像処理システム検査事例
近年では画像センサ・画像処理システムによる外観検査の需要が増えています。画像センサは、インライン上でネジ・ボルトの寸法測定・外観検査が同時に実施でき、全数検査による漏れ・不良流出の防止に有効です。バリや割れ・欠け(クラック)・変形・寸法ズレ・異品種・未加工品の混入などを一度の検査で判別できるので生産性アップにも効果を発揮。さらに全数の品質情報をデジタルデータで保存・管理できるのでトレーサビリティの確保や工程改善にも有効です。
従来の画像センサ・画像処理システムは、バリや欠けなどの微妙な不具合の判別が困難でした。また、導入や設定に手間がかかるという問題もありました。しかし、キーエンスの画像センサ「CV-Xシリーズ」/画像処理システム「XG-Xシリーズ」は、ネジ・ボルトの寸法測定や外観検査を手軽に行うことができます。
高精細な2100万画素のカメラや3次元形状測定が可能なレーザプロファイル測定器「LJ-V7000シリーズ」に加え、安定検出を実現する「LumiTraxTM」、わずかな色の違いも検出可能な「マルチスペクトル撮像」などの技術で正確かつ素早い検査を実現します。
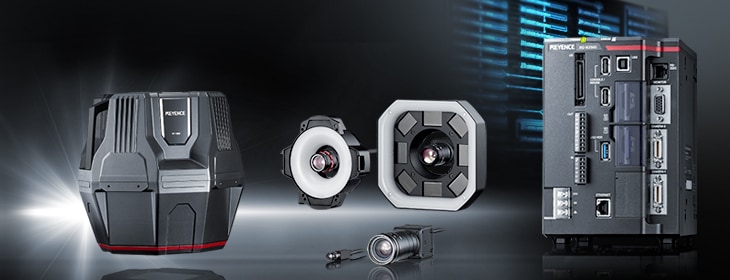
輪郭欠陥検査ツールを利用すれば、バリ・欠けなども簡単・確実に検出可能です。最大5000点のエッジ情報をもとに輪郭を検出するので、ネジ・ボルトの最大径やピッチなどの寸法測定でも力を発揮します。そのほかマルチスペクトル撮像を利用すれば、わずかな色の違いも判別可能なので異品種混入も防げます。
1台で複数の検査ができ、インライン上で完結するので生産性向上にも効果的です。汎用性が高く、さまざまな工程に対応できることも魅力の画像センサ「CV-Xシリーズ」/画像処理システム「XG-Xシリーズ」。外観検査でお困りならお気軽にキーエンスまでご相談ください。
ネジ頭の小さな割れ
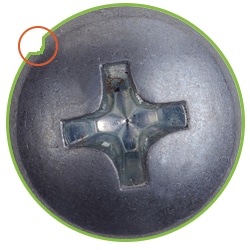
ネジ山の寸法
ボルトの寸法計測
ボルトの最大径やねじの山谷寸法を測定することができます。
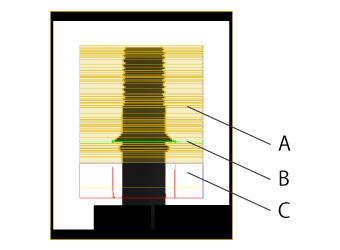
- セグメントごとの検出エッジを表示。個別に結果出力
- 最大径を検出
- セグメントごとのエッジ強度波形を確認可能。確実な設定ができます。
検出原理
検査領域内で指定した幅のセグメントが、重なりあいながら指定ピッチで移動し、それぞれの場所でエッジ検出を行ないます。1/100 画素単位での移動量が指定できるためエッジは測定部に対して抜けなく検出できます。
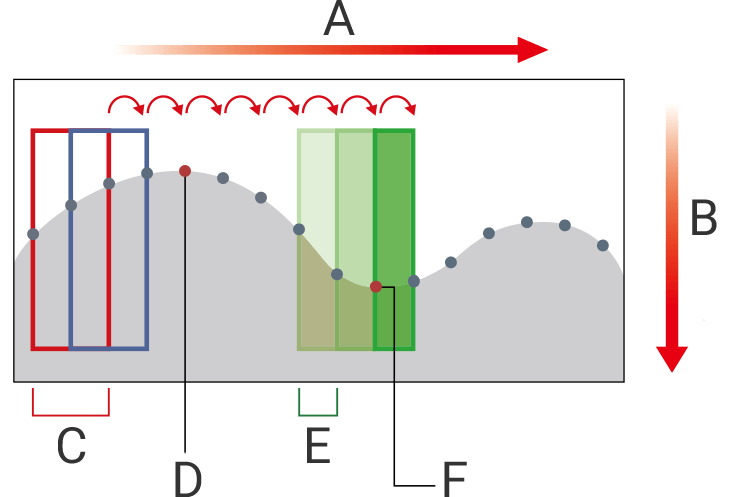
- セグメントの移動方向
- エッジ検出方向
- セグメント幅
- 検出されたピーク
- 移動量
- 検出されたボトム
まとめ
このページでは、ネジ/ボルトの種類と製造工程について説明しました。また、それぞれに発生するトラブルと外観検査の方法についても紹介しました。それらをまとめると、以下の通りです。
- ネジ/ボルトは製造工程の発展により大量生産が可能になったが、製造工程で発生する不良を完全に防ぐことは困難。
- 外観検査だけではなく、寸法検査やねじ山のピッチ検査などを行う必要がある。
- キーエンスの画像処理システムなら、呼び径・谷径・ピッチも、同時にインライン検査が可能。
ワークによって、外観検査の方法もさまざまです。最適な外観検査を行うには、それらの特徴を知り、正しく検査することが大切です。
このページで紹介した内容や、他のページに記載している外観検査の知識を1冊にまとめた資料「外観検査のすべて」は、下記からダウンロードできます。画像処理システムの導入事例集とあわせてご覧ください。