テーラードブランク溶接のビード形状
板厚・材質・強度・表面処理などが異なる鋼板を溶接でつなぎ合わせたプレス材料を「テーラードブランク(Tailored Blanks)」と呼びます。テーラードブランクは、異種鋼板をつなぎ合わせる溶接工程が非常に重要です。こちらでは、テーラードブランクを製造するうえで欠かせない溶接の基礎知識、テーラードブランク溶接のビート形状において発生しやすい不良の種類や発生原因、外観検査の方法、最新画像処理システムを活用した検査事例をご紹介します。
製造の概要・基本
テーラードブランクとは
「テーラードブランク(Tailored Blanks)」は、異種鋼板をつなぎ合わせたプレス材料です。複数の鋼板を目的に合わせて溶接し、仕立てる(Tailored)プレス材料のためテーラードブランクと呼ばれています。また、同様の工法をテーラードブランクと呼ぶ場合もあります。特徴は、異種鋼板をつなぎ合わせることで、1枚の鋼板の中で部分的に特性を変えられることです。主に自動車ボディの製造で活用されています。
-
溶接 -
打ち抜き -
成形
テーラードブランクの利点
テーラードブランクは、その特徴から強度や耐久性、防錆、衝突安全性、軽量化、精度などの要求が多く、3次元的なデザイン性が求められ、パネルの部品点数を減らす必要がある自動車用ボディで広く利用されています。テーラードブランクの利点は以下のようになります。
- 目的に合わせて板厚や材質などを最適配置できる
- 連続的な線溶接で仕上げるので結合強度が高い
- スポット溶接のように重ね合わせ代が少なくて済む
- 素材や形状の自由度が高い
- パネルの部品点数を減らせるので作業効率が良い
テーラードブランクの溶接
テーラードブランクの溶接では、レーザ溶接、マッシュシーム溶接、プラズマ溶接などが用いられます。
レーザ溶接
レーザ溶接は、レーザ光を直系0.5mm程度に集光して鋼板に照射し、融解溶接を行う方法です。見た目が美しく、溶接熱による材質劣化範囲が極めて狭いことが特徴です。一般的な溶接ビード幅は1mmほどです。
マッシュシーム溶接
2枚の鋼板を平均板厚の1.5~2倍程度重ね合わせて、加圧しながら通電・溶解する溶接方法です。高速で溶接が可能ですが、条件管理が難しい、高強度鋼板の溶接が難しい、溶接部の板厚が厚くなる、見栄えがあまりよくないなどの問題があります。一般的な溶接ビード幅は5mmほどです。
プラズマ溶接
プラズマ溶接は、高温のプラズマ気流を接合部に吹き付ける熱伝導型の溶接方法です。タングステン電極が露出していないので電極の交換頻度が低く、自動化に適しています。また溶接コストを抑えられることも利点です。一般的な溶接ビード幅は3~4mmです。
よく起こる不良の種類と発生要因
テーラードブランクの溶接は、鋼材融解量が少ないため、突き合わせの隙間が大きかったり、突き合わせ線の倣い不良があったりすると溶接ができなくなります。こちらでは、最も一般的なレーザ溶接時における注意点、よく起こる不良の種類、不良の発生要因について説明します。
アンダーフィル
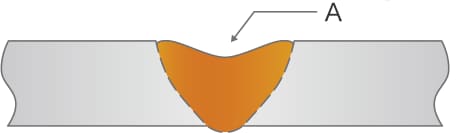
- A:アンダーフィル
突き合わせの隙間が大きいと、溶解不足で溶接ビードの厚みが鋼板板厚に比べて薄くなる「アンダーフィル」になります。アンダーフィルで溶接ビードが凹んだ状態になると、応力集中が起こり破断・クラックなどの原因になります。
アンダーカット

- A:アンダーカット
溶接ビード両端に陥没部分がある欠陥を「アンダーカット」と呼びます。溶接電流や溶接速度が高すぎることが主な原因で、アンダーカットが発生すると陥没部分からクラックが発生することがあります。アンダーカットを防ぐには、溶接電流・溶接速度を低く設定するなどの対策があります。
溶接割れ(クラック)

- A:縦割れ
- B:上端割れ
- C:横割れ
- D:クレーター割れ
レーザ溶接は、金属を急熱急冷するため、溶解部の熱ひずみで溶解割れが発生することがあります。溶解割れが発生する要因はさまざまですが、鋼板選びや溶接条件の変更などで防ぐことができます。また、溶接中および直後に発生する溶接割れを「高温割れ」、冷却後から2~3日以内に発生する溶接割れを「低温割れ」と言います。
ボロシティ(巣・気泡・ピット)

- A:ピット(開口欠陥)
- B:ブローホール
レーザ溶接で発生しやすい溶接不良として、溶接金属部に空孔が発生する「ボロシティ」が挙げられます。キーホールから発生した気泡が凝固した大型のボロシティ、材料内から気体成分が拡散してできた小型のボロシティなどがあります。ボロシティの発生を予防するには、溶接条件の最適化に加え、溶接箇所の油分やサビの除去など前処理が重要です。
溶接金属内部に発生したガス孔がビード表面に放出されたときに穴となって固まった表面欠陥を「ピット(開口欠陥)」、ビード内部のガス孔が残った内部欠陥を「ブローホール」とも呼びます。
従来の検査方法
溶接後の測定・検査は、「溶接の表面測定・検査」と「溶接の内部測定・検査」に大別されます。溶接表面の測定・検査は、目視検査のほか、磁粉を使う「磁粉探傷試験(MT)」や特殊な液体を使う「浸透探傷試験(PT)」などで行います。溶接内部は、超音波や放射線による検査が一般的です。
また、溶接内部の状態を知るために破壊検査も一般的です。しかし、全数破壊検査することは不可能なので、通常は初品・中間品・終品の抜き取り検査を実施します。また、画像センサを用いて溶接ビードのズレなどを検査することもあります。しかし、通常の画像センサでは高さを認識できず、アンダーフィルやアンダーカットなどを検知できないという問題点がありました。そこで近年では、インラインでも高速かつ高精度な自動検査が実現する「レーザ変位計」を使った非接触検査が増加傾向にあります。

最新画像処理システム検査事例

3次元形状検査に対応したキーエンスの超高精細インラインプロファイル測定器「LJ-X8000シリーズ」は、2次元断面形状データだけでは検出できなかったアンダーフィル・アンダーカットの検査が可能です。
テーラードブランクの溶接を行うロボットのトーチに「LJ-X8000シリーズ」を取り付けることで、溶接直後のビード形状を測定可能。従来のカメラ(写真A)では測定が困難でしたが、レーザ変位計「LJ-X8000シリーズ」を用いた3次元画像処理なら安定してビード形状を測定できます。
ビード表面の蛇行(ビード曲がりやビードズレなど)に加え、レーザ変位計「LJ-X8000シリーズ」は3次元計測に対応しているのでアンダーフィル・アンダーカット、割れ、スパッタの付着などの溶接欠陥を即座に検出し、不良の発生を最小限に抑えることができます。
「LJ-X8000シリーズ」は、最速64kHzサンプリングにより、自動溶接の素早いトーチ移動に追随してヘッドを並走させても安定検出を実現します。多彩な測定モードを活用することで、さまざまなワークの溶接部、溶接継手の形状検査に対応することができます。テーラードブランクの溶接ビード形状検査でお困りなら、お気軽にキーエンスまでご相談ください。

まとめ
このページでは、テーラードブランクの溶接工程や利点、溶接法について説明しました。また、溶接工程で発生するトラブルと外観検査の方法についても紹介しました。それらをまとめると、以下の通りです。
- テーラードブランクとは、異種鋼板を溶接してつなぎ合わせたプレス材料である。
- 溶接後の検査には、目視などで行う「表面測定・検査」と磁粉や特殊な液体を使用する「内部測定・検査」がある。
- キーエンスのレーザ変位計や画像処理システムを使えば、インラインで開先やビードの形状を3次元測定できる。
ワークによって、外観検査の方法もさまざまです。最適な外観検査を行うには、それらの特徴を知り、正しく検査することが大切です。
このページで紹介した内容や、他のページに記載している外観検査の知識を1冊にまとめた資料「外観検査のすべて」は、下記からダウンロードできます。画像処理システムの導入事例集とあわせてご覧ください。