基板実装・はんだ付けの検査
プリント基板に電子部品を接合する工程を「基板実装」と言い、基板実装には「はんだ付け」が用いられます。こちらでは、基板実装・はんだ付けの外観検査について説明します。基板実装・はんだ付けの基本的な知識、よく起こる不良の種類や発生原因、従来の検査方法と最新画像処理システムを活用した検査事例を紹介します。
製造の概要・基本
基板実装について
基板実装(プリント基板実装)とは、プリント基板に電子部品を接合し、電子回路として機能するようにする工程です。電子部品を接合する方法として「はんだ付け」が用いられます。また、電子部品の接合には、「挿入実装(IMT:Insertion Mount Technology)」「表面実装(SMT:Surface Mount Technology)」という2つの方法があります。そのほかむき出しの半導体に電極を設けてプリント基板に実装する「ベアチップ実装」などもありますが、今回は基本的な「挿入実装(IMT:Insertion Mount Technology)」「表面実装(SMT:Surface Mount Technology)」について説明します。
挿入実装(IMT:Insertion Mount Technology)
挿入実装(IMT:Insertion Mount Technology)は、プリント基板のスルーホール(穴)にリード(電極)を差し込み、はんだ付けで接合する実装方法です。部品を基板上に配置するために基板が大きくなり、小型化が難しいという問題点があります。
表面実装(SMT:Surface Mount Technology)
現在の基板実装の主流が「表面実装(SMT:Surface Mount Technology)」です。表面実装(SMT:Surface Mount Technology)では、スルーホール(穴)を使わず、基板表面にあるパッド(ランド)に電子部品の電極をはんだ付けします。挿入実装(IMT:Insertion Mount Technology)のようにリード(電極)が貫通しないので、基板の両面を利用して多くの電子部品を配置でき、小型化できることがメリットです。また、表面実装用のリードがない小型・高密度な電子部品を「表面実装部品(SMD:Surface Mount Device)」と呼びます。


表面実装の方法について
表面実装の工程は、大きく「手はんだ工程」「リフロー工程」の2つに分けることができます。手はんだ工程は、その名のとおり人間が手作業で行うはんだ付けです。一方、リフロー工程は、基板のパッド(ランド)にソルダペースト(ペースト状のはんだ)を塗布(印刷)し、その上に表面実装部品(SMD:Surface Mount Device)を搭載し、リフロー炉と呼ばれる装置で基板全体を熱してはんだを溶かして接合します。
表面実装の一般的な流れ
現在、量産品の製造では「表面実装+リフロー工程」が主流なので、一般的な作業工程を紹介します。
- 1.印刷工程
-
表面実装(SMT:Surface Mount Technology)における印刷工程は、ソルダペースト(ペースト状のはんだ)を基板上のパッドに転写することを指します。印刷というとプリント基板の印刷を想像するかもしれませんが混同しないように注意してください。印刷は、一般的にメタルマスクと呼ばれるステンレスの薄い板に穴をあけた印刷版を使用します。
- 2.マウント工程
-
マウントは、表面実装部品(SMD:Surface Mount Device)をソルダペースト(ペースト状のはんだ)を印刷した基板に載せていく工程です。マウント工程では、プリント基板に電子部品が載っているだけで、固定されていないので衝撃で簡単に位置がずれるので注意してください。
- 3.リフロー工程
-
リフローは、ソルダペースト(ペースト状のはんだ)と表面実装部品(SMD:Surface Mount Device)が載ったプリント基板を炉に入れて加熱する工程です。リフロー炉と呼ばれる設備で加熱することでソルダペースト(ペースト状のはんだ)を溶かし、表面実装部品(SMD:Surface Mount Device)を接合します。最終的に冷却すれば基板実装完了です。
よく起こる不良の種類と発生要因
基板実装でよく起こる不良の種類とその発生原因について説明します。こちらでは、リフロー後の接合部をチェックする「はんだ付け外観検査」で発生しやすい不良を紹介します。
未実装(実装確認)
未実装(実装確認)は、基板実装の外観検査の基本です。正しい位置に正しい電子部品が実装されているか、また実装漏れがないか検査します。マウント工程での載せ忘れ、ソルダペーストの転写漏れによる未接合、部品供給不備、マウント工程後の脱落などの発生要因が考えられます。
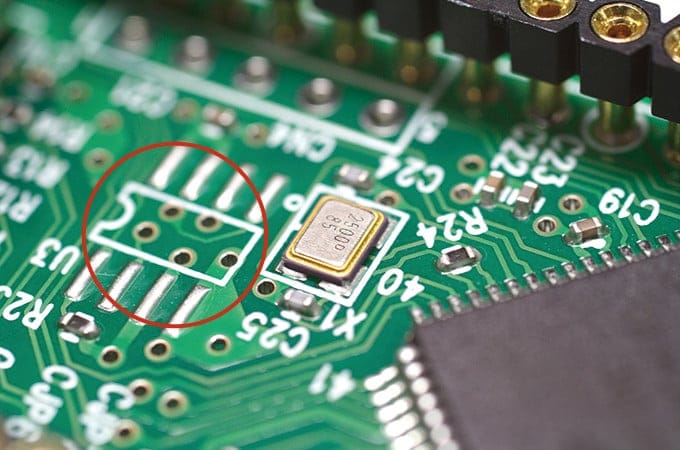
断線・ショート
はんだ不備による断線、不要なはんだによるショートなどが発生し、パターン設計通りに再現されていない状態です。そのほかにも断線・ショートの要因が複数ありますので、製造後に導通検査を行うことが最も有効な対策です。また、製造時にかろうじて導通しているというケースもあるので注意が必要です。

クレイジング・ミーズリング


機械的なストレスによりガラス繊維が樹脂から剥離する現象を「クレイジング」と言います。また、主に熱ストレスでガラス繊維が剥離する現象を「ミーズリング」と言います。
層間剥離(デラミネーション)

熱衝撃や基板の水分、積層工程での不備などにより、ガラス繊維の樹脂から剥離している状態です。層間剥離とも呼び、この状態になった基板は使用できません。
ボイド・ブローホール・ピンホール
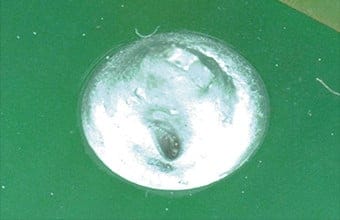
ブローホールとは、ソルダフィレットにできる孔のことです。はんだ内で発生したガスが表面まで浮き上がった状態で、スルーホール内部にボイドが発生して外観上は見えないこともあります。ピンホールは、はんだ下に空洞ができ、表面に小さな穴が貫通している状態です。どちらもガスの放出が原因で、プリント基板に水分や汚れ、ガスなどが付着していると発生しやすくなります。
濡れ不良

はんだ付けは、毛細血管現象と濡れ現象を利用して接合しています。「濡れ」とは、はんだの馴染みやすさで、この性質を「濡れ性」と表現します。使用するはんだの性質にもよりますが、はんだ付けを行う場所の油脂汚れ、はんだ付けの温度不足、フラックス量不足などでも濡れ不良が発生します。
ソルダボール(はんだボール)
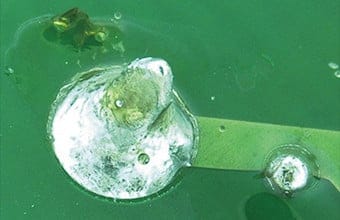
コテ先についたはんだが飛び散り、冷え固まったものをソルダボール(はんだボール)と呼びます。名前のとおりボール状になり、通常は基板から剥がれるので不良になりません。しかし、ICなどのリードの隙間にはさまるとショートの原因になるので注意が必要です。発生原因は、コテを引き抜くスピードが早すぎる、フラックスやガスの問題などが考えられます。
ブリッジ(ブリッジはんだ)・つらら(ツノ)
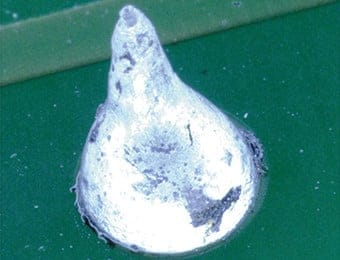
ICなどのピンの間ではんだが橋のようにつながる状態を「ブリッジ(ブリッジはんだ)」と呼び、ブリッジのように完全にはつながらずにはんだが角状に飛び出した状態を「つらら(ツノ)」と呼びます。原因は、はんだ付けの温度が低い、時間が短い、濡れ不足、フラックスの問題などが考えられます。いずれもショートの原因になります。
部品立ち・チップ立ち(ツームストーン・マンハッタン現象)

ICなどを接合する際に片側のはんだ付けに不良があり、剥がれて部品が立ち上がってしまうことを「部品立ち・チップ立ち」と言います。要因は、印刷ズレや実装ズレ、パッド設計の問題、はんだ過多などが考えられます。部品立ち・チップ立ちを防ぐには、ランド寸法を小さくする、予熱をする、ソルダペースト塗布量を少なくするなどが考えられます。
イモはんだ(コールドジョイント)

コテの温度が低すぎたり、当てる時間が短すぎたりすると発生する不良が「イモはんだ」です。イモはんだは、濡れ不良が原因で、フィレットが丸みを帯びた形状になります。また、イモはんだは、ボイドを引き起こす原因にもなり、導通不良にもつながります。
はんだ不足

送るはんだの量がすくない場合に起こる不良が「はんだ不足」です。ランドやリードが汚れているときにも発生します。
従来の検査方法
基板実装・はんだ付けの外観検査は、接合信頼性を保証するうえで重要な検査のひとつです。検査方法は、目視検査が一般的です。専用検査装置もありますが高価なため導入できないケースもあります。また、近年は電子部品の小型化・集積化により、目視検査では判別が困難で顕微鏡検査などの実施が必要なケースも増えています。
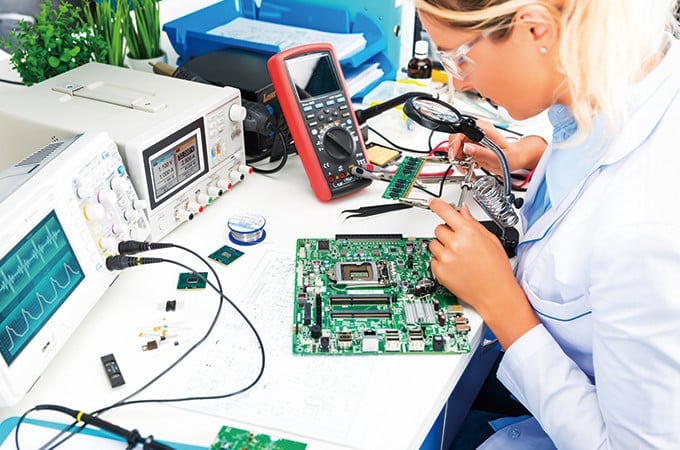
最新画像処理システム検査事例
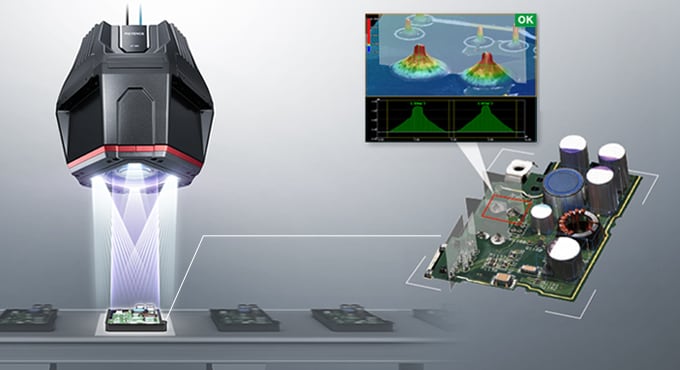
キーエンスの画像処理システム「XG-Xシリーズ」は、通常の画像センサに加えて3次元検査にも対応しています。「XG-Xシリーズ」に3次元画像処理「XTカメラ」を接続することで、高さ・面積・体積などの計測が可能なので、はんだの量や大きさ、フィレット形状を正確に判別できます。
「XTカメラ」は方向依存性の無い4 投光RGBプロジェクターを使用しストライプパターンを投影、ワークからの反射光を944 万画素CMOS 撮像素子と専用プロセッサがリアルタイムに解析することで3D画像を生成します。高精度なテレセントリックレンズを搭載することで画角の影響を抑え、“ 実寸” で正確に捉えるための死角の無い画像を撮像することが可能です。画像処理システム「XG-Xシリーズ」と3次元画像処理「XTカメラ」の組み合わせなら、インラインで3次元形状の見える化・数値化ができるので、生産の効率化と接合信頼性の保証を同時に実現できます。
両軸投光(アルゴリズム)
方向が90°異なる斜めプロジェクションパターンを投影、解析することで光沢による多重反射の影響を軽減します。さらに突出ノイズ除去、片投光部除去といった光沢の強いワークで生じやすいノイズ計測点を除外するアルゴリズムを追加し、はんだのような光沢のあるワークでも精度の高い計測が可能です。
- 両軸投光
- ノイズデータのもととなる反射光を効果的に選別します。

- 突出ノイズ除去
- 周囲の計測データから不連続なデータを正確に除去します。

3次元計測ならX・Y・Z方向の検査が1台で可能
従来の2次元検査では、濃淡情報だけで検査が安定しませんでした。3次元検査ならXY情報に高さ(Z)情報を加えることで堆積や断面積を用いた検査ができます。
- 2次元検査の場合
- 濃淡情報だけでは検査が安定しませんでした。

- 3次元検査で解決
- XY情報に、高さ(Z)情報を加えることで体積や断面積を用いた検査ができます。

3D寸法幾何連続プロファイル計測
3D寸法幾何連続プロファイル計測を活用すれば、フィレットの角度や基板面からトップまでの距離、幅や断面積など、はんだ形状を3次元的に捉えて検査が行えます。従来の画像処理システムで同様の検査を行う場合、複雑なプログラムを作成する必要がありました。しかし、画像処理システム「XG-Xシリーズ」は、多種多様な検査項目も直感操作で誰でも簡単に設定でき、導入直後からハイレベルな検査を実現できます。

まとめ
このページでは、基板実装やはんだ付けの外観検査に必要な基礎知識を説明しました。また、不良の種類や発生原因、外観検査の方法についても説明しました。それらをまとめると、以下の通りです。
- 基板実装・はんだ付けの外観検査や寸法検査は、接合信頼性を保証するうえで重要。
- 顕微鏡や専用検査装置による抜取検査では、手間がかかる上目視検査のばらつきによって品質の保証が困難。
- キーエンスの画像処理システムなら、1台で全数インライン検査でき、効率化と品質向上の両立が可能。
ワークによって、外観検査の方法もさまざまです。最適な外観検査を行うには、それらの特徴を知り、正しく検査することが大切です。
このページで紹介した内容や、他のページに記載している外観検査の知識を1冊にまとめた資料「外観検査のすべて」は、下記からダウンロードできます。画像処理システムの導入事例集とあわせてご覧ください。