ギヤ(歯車)/シャフトなどの円柱状ワークの側面
動力伝達装置である「ギヤ(歯車)」「シャフト」は、エンジンやモーターなどの回転運動を伝えるために必要不可欠な機械要素です。ギヤボックスやデファレンシャルギヤ、ドライブシャフトなどの自動車向けをはじめ、駆動する場所には必ずと言っていいほど使用されているギヤ(歯車)/シャフト。こちらでは、ギヤ(歯車)/シャフトなどの円柱状ワークの外観検査を行ううえで覚えておくべき基礎知識と製造方法、よく起こる不良の種類や発生原因、一般的な検査方法に加え、最新画像処理システムを活用した検査事例をご紹介します。
製造の概要・基本
ギヤ(歯車)/シャフトとは
ギヤ(歯車)とは、周囲に歯型がついた動力伝達部品です。動力を伝えるほか、減速や増速、回転軸の向きを変えたり、動力を分割したりするために用いられます。ギヤ(歯車)には、一般的な「平歯車」のほか、「かさ歯車」「はすば歯車」「ラックとピニオン」「ウォームとウォームホイール」のようにさまざまな種類があります。
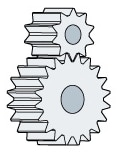
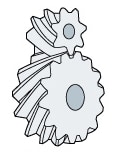
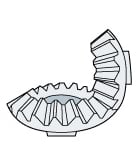
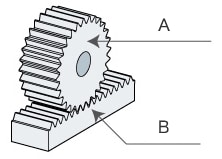
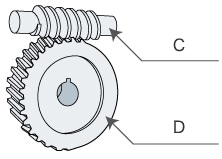
シャフトも同様に動力を伝える部品で、日本語では「軸」とも呼ばれる棒状の機械要素です。直線状のものほか、クランクシャフトのようなクランク状に折れ曲がったもの、カムシャフトのような偏心させたものなど多種多様な形状があります。
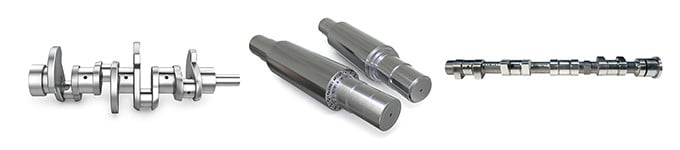
ギヤ(歯車)/シャフトの共通点は、動力伝達部品であり、主に円柱状の形状をしていることです。また、動力を伝えるためにギヤ(歯車)とシャフトを組み合わせて使用することも多くあります。
ギヤ(歯車)/シャフトの製造工程
ギヤ(歯車)/シャフトともに円柱状の材料を切削加工し、歯型をつけるために歯切を行い、熱処理・表面処理などを加えて仕上げます。ギヤ(歯車)/シャフトなどの円柱状ワークの場合、通常は旋盤などを用いて切削加工を行います。以下は一般的なギヤ(歯車)/シャフトの製造工程です。実際は、形状や使用目的により製造工程が異なりますが、一般的には以下のような工程で製造します。
一般的なギヤ(歯車)の製造工程
製品の用途・要求を満たす素材を旋盤で切削加工し、歯車加工前形状(歯車ブランク)にします。その後にホブやポニオンカッターといった特殊工具を使い、歯部を加工してギヤ(歯車)に仕上げます。最終的には、強度や粘り強さを与える「焼入れ」、歯車の仕上がり寸法を調整する「研削」、歯の精度を調整する「歯研」等の工程を経て検査・出荷となります。
-
材料 -
切削加工 -
歯切 -
焼入れ -
研削 -
歯研
シャフトの製造工程
棒状の素材を所定の長さに切断し、切削加工やプレス加工などで指定の形状にします。その後に歯・スプライン(溝)等をつくるために切削加工を加えたり、熱処理・表面処理を行ったり、仕上がり寸法を調整するために研削等で仕上げます。
-
材料・切断 -
表面処理 -
プレス加工 -
切削加工 -
歯切 -
面取 -
熱処理 -
研削・歯研
よく起こる不良の種類と発生要因
ギヤ(歯車)/シャフトなどの円柱状ワークにおいてよく起こる不良の種類と発生原因をまとめました。発生要因は、水・薬品の影響、切削時の金属の飛び散り、ホコリ・ゴミの侵入、運搬時や加工時の衝撃などさまざまです。ここでは外観検査時の参考に一般的な例として説明します。
バリ
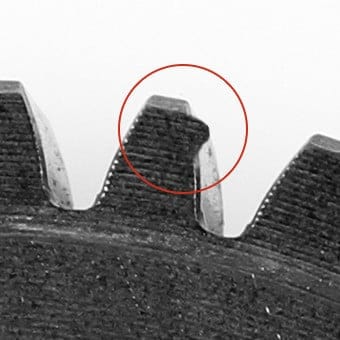
旋盤などで切削加工を行う際、素材の性質やバイト(刃)の種類、送り速度などによってはバリが発生することがあります。また、ギヤの歯やシャフトのスプラインを加工する際も同様です。バリは歯の噛み合わせに影響を及ぼすので、通常はバリ取り(面取り)を行い除去します。
割れ・欠け(クラック)
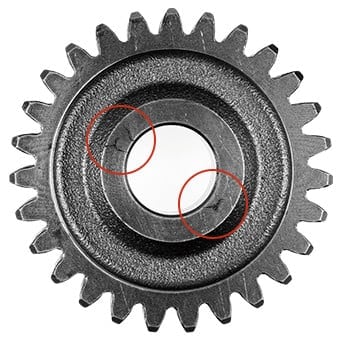
切削加工や研磨加工時にワークに割れ・欠け(クラック)が発生することがあります。また、研磨時に発生するものを「研磨割れ」と呼びます。このような割れ・欠け(クラック)の原因は、ワークに無理な力がかかっている、加工時の熱による膨張、残留応力などが考えられます。割れ・欠け(クラック)が発生する場合は、切削条件を見直す、冷却液でワークの温度を下げるなどの工夫が必要です。また熱処理時にヘアクラックが発生することもあります。ギヤ(歯車)/シャフトは力のかかる部品なので、割れ・欠け(クラック)による強度低下は致命的な欠陥となります。
変形・寸法ズレ
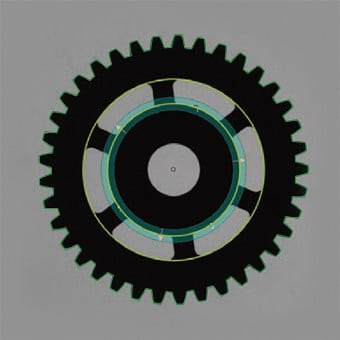
切削加工では、ワークに熱が加わるので変形・寸法ズレが発生することがあります。ギヤ(歯車)/シャフトなどは、歯の噛み合わせ精度が非常に重要なので、研削を実施して仕上がり寸法に仕上げます。
傷(線傷)
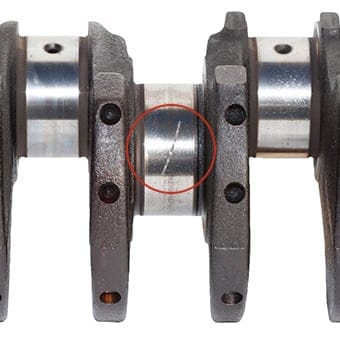
切削時に発生した金属粉や砥粒などが接触して起こる傷、旋盤のチャック爪による傷などが考えられます。傷(線傷)は強度に影響し、割れ・欠け(クラック)を引き起こす原因にもなるので、目視検査等で流出を防止することが大切です。
異物・汚れ
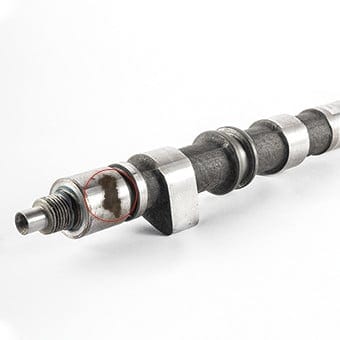
加工時や搬送時に異物が混入したり、汚れが付着したりすることがあります。異物や汚れの侵入経路・発生原因の特定は難しく、各工程での目視検査に加え、最終製品の外観検査を徹底することが大切です。
巣(空気孔)
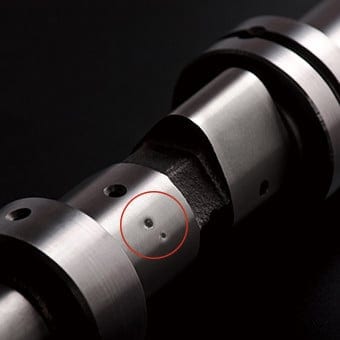
熱加工や表面処理により巣(空気孔)が発生することがあります。巣(空気孔)は、強度や粘り強さに影響を及ぼす可能性があります。
従来の検査方法
ギヤ(歯車)/シャフトなどの円柱状ワークの検査は、側面や断面、内径などの外観検査が必要です。さらにギヤの歯型・歯すじ・ピッチなどの寸法検査を行う必要もあり、手作業では非常に時間・手間がかかっていました。
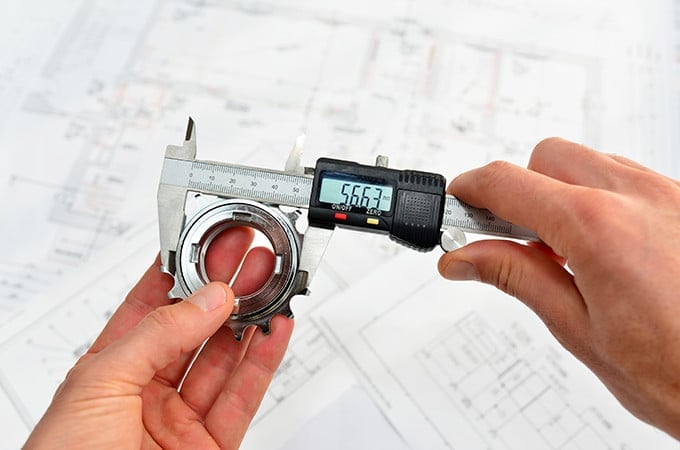
最新画像処理システム検査事例
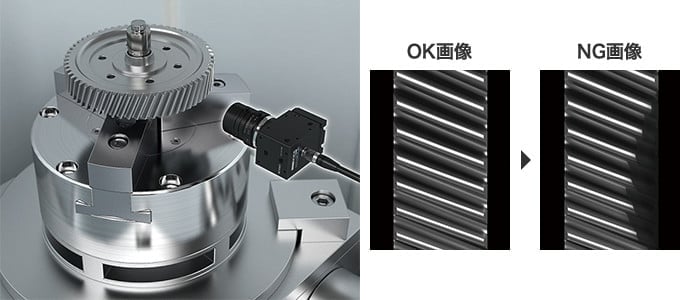
従来の画像処理システムによる外観検査では、ギヤ(歯車)/シャフトのような円柱状ワーク側面に照明を均一に当てることが困難で、黒皮残り、汚れ、傷、打痕等の検査が困難でした。しかし、ラインスキャンカメラを使用することで照明ムラのない1枚に展開した画像を生成可能です。
キーエンスでは、最速142,800ライン/秒撮像に対応したラインスキャンカメラや微細欠陥まで抽出できる高速縞パターン発光を採用したLED照明、ラインスキャンカメラに対応した画像処理システム「XG-Xシリーズ」を用意。これまで難しかったギヤ(歯車)/シャフトなどの円柱状ワーク側面の外観検査の自動化を実現しました。
また、複雑な輪郭形状を抽出する「マルチトレンドエッジ欠陥」機能を使えば、ギヤ(歯車)の歯に残った小さなバリまたは欠けのような目視検査では見逃してしまう小さな変化も検出可能。ラインスキャンカメラ対応の画像処理システム「XG-Xシリーズ」は、さまざまな外観検査を自動化できるので生産性向上・タクト短縮に効果的です。外観検査でお困りならお気軽にキーエンスまでご相談ください。
-
検査したい検査面の端面をクリック
-
選択した輪郭に囲まれた面を抽出
-
指定した検査面で欠陥を検出可能
まとめ
このページでは、ギヤ(歯車)/シャフトの種類と製造工程について説明しました。また、それぞれに発生するトラブルと外観検査の方法についても紹介しました。それらをまとめると、以下の通りです。
- ギヤ/シャフトの製造方法は異なるが、いずれも製造工程で発生する外観不良、異物混入などが不良となる。
- ギヤやシャフトのような円柱状ワークの検査では、側面に照明を均一に当てるのが困難。
- キーエンスの画像処理システムなら、円柱状ワークでも照明ムラのない画像を生成できる。
ワークによって、外観検査の方法もさまざまです。最適な外観検査を行うには、それらの特徴を知り、正しく検査することが大切です。
このページで紹介した内容や、他のページに記載している外観検査の知識を1冊にまとめた資料「外観検査のすべて」は、下記からダウンロードできます。画像処理システムの導入事例集とあわせてご覧ください。