オイルシールの輪郭
エンジンやギヤのオイル漏れを防いだり、外部からのホコリの侵入を防止したりするために使用されるオイルシールの輪郭検査(測定)について説明します。こちらでは、オイルシールの輪郭を検査するうえで覚えておくべき基本的な知識、よく起こる不良の種類や発生原因、従来の検査方法と最新画像処理システムを活用した検査事例を紹介します。
製造の概要・基本
オイルシールについて
オイルシールは、オイル(油)をシール(封じる)するための部品です。同様に密封する部品としてOリングやリップパッキン、グランドパッキン、メカニカルシール、ガスケットなどもあります。基本的には、すべて気体や液体の漏れや侵入を防ぐために使われてます。オイルシールについては、ゴム素材が一般的ですが一部には金属や樹脂などもあります。今回は、最も一般的なゴム製オイルシールについて説明します。
オイルシールの製造方法
オイルシールは、ほかのゴム製品と同様にさまざまな成形方法によって製造されます。最も一般的な方法が「金型成形・プレス成形」、そのほかに大口径のOリング製造に用いられる「送り焼き成形、継ぎ成形」、ゴム紐を接着してOリング状にする「押出丸紐接着加工、押出丸紐加硫接着加工」、ゴムシートやゴムブロックを削ってOリング状にする「機械加工」などがあります。
金型成形による製造工程
最も一般的な「金型成形」を題材にオイルシールの製造工程を紹介します。金型成形では、高温に加熱した金型で原材料のゴムを挟み込み、加圧してリング状に成形します。整形後は金型から取り出し、バリを取り除いて完成です。オイルシールの金型成形では、多品種少量生産に適したプレス成形(圧縮成形)と、大量生産に適した射出成形(インジェクション成形)の大きく2つに分けられます。
-
-
断面図 -
-
よく起こる不良の種類と発生要因
オイルシールの製造でよく起こる不良の種類とその発生原因について説明します。こちらでは、プレス成形(圧縮成形)・射出成形(インジェクション成形)で発生する不良をまとめています。
充填不足(ショートショット)
射出成形(インジェクション成形)で、原材料の充填不足が起こり、製品が不完全な状態で冷却固化する現象を「充填不足(ショートショット)」と言います。原因は、原材料の充填量不足や充填圧力が低い、射出速度が遅い、金型内にガスが発生して充填不良が起こる、金型形状に問題があり樹脂が行き渡らないなどが考えられます。

バリ
プレス成形(圧縮成形)の場合は、必ずバリが発生するので除去する作業が必須です。射出成形(インジェクション成形)でも金型の合わせ面に隙間やキズがあったり、射出速度が速かったりすると発生します。

剥離
成形時に薄い膜状の層ができ、それが剥がれてしまう現象です。樹脂温度や金型温度が低かったり、射出速度が遅かったり、保圧が低かったり、異物が混入していると剥離が発生することがあります。対策としては、樹脂温度・金型温度・射出速度の設定変更や金型の清掃などが有効です。

糸引き
金型を開けたときに発生する細い樹脂の糸を「糸引き」と呼び、この樹脂の細い糸が金型内に残ったまま次の製品を成形すると筋状の凹凸が製品に残ります。糸引きを防止するには、射出成形(インジェクション成形)のノズル温度を調整したり、成形ごとに金型を清掃したりするなどの対策が有効です。

フクレ・ヒケ
成形品の表面に出る膨らみを「フクレ」、へこみを「ヒケ」と呼びます。フクレ・ヒケは、冷却の不均一や圧縮不足により発生します。ヒケは、充填不足(ショートショット)や射出圧力不足、射出速度が速い場合にも発生します。そのほか樹脂温度が金型温度が高い場合、製品の肉厚があり冷却に問題がある場合などにも発生します。

変形(反り・ねじれ)


成形品の各部で収縮量に差が生まれると反りやねじれといった変形が発生します。主な原因としては、金型温度分布の差にともなう面収縮差、成形品の厚みの差による収縮差などです。冷却不足や樹脂温度が低い、射出圧力が高い場合にも発生します。
割れ・欠け(クラック)
金型から製品を取り出すときに力がかかったり、成形時に内部に歪みなどが発生したりすると割れや欠け(クラック)が発生します。
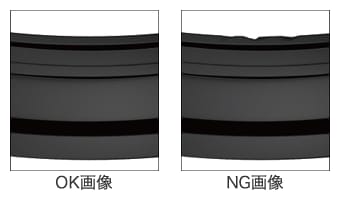
従来の検査方法
オイルシールは、ゴム製で形状が不均一なので輪郭検査の自動化が難しく、目視検査に頼らざるを得ませんでした。目視検査でも変形しやすく形状が不安定なので判断が難しく、反り・ねじれのような変形の判断は困難です。また、ノギスやマイクロメータで計測するときに誤差が発生しやすいという課題もありました。さらに目視検査では、小さな割れ・欠け(クラック)などの発見も難しく、検査員によってばらつきが発生しやすいという課題もあります。
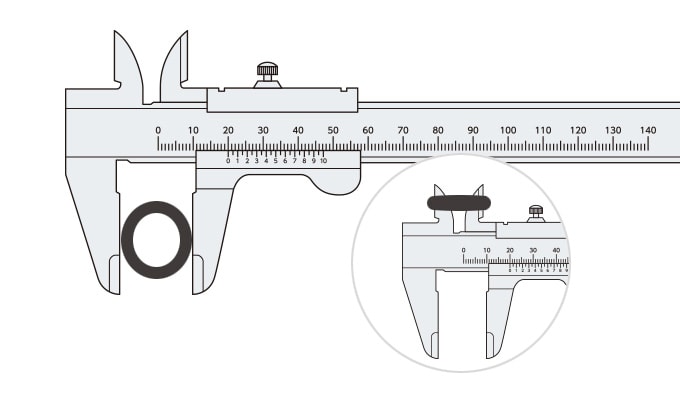
最新画像処理システム検査事例
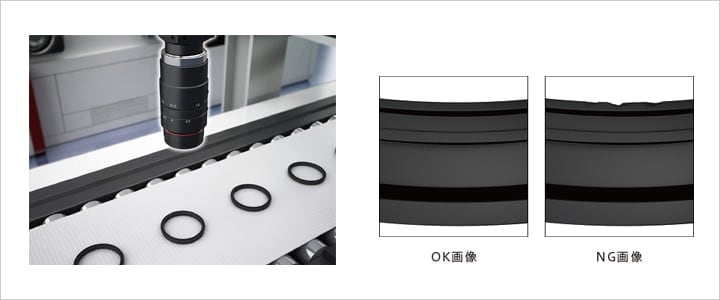
キーエンスの画像処理システム「CV-Xシリーズ」「XG-Xシリーズ」に搭載されている「トレンドエッジ欠陥モード(ワークのエッジ情報から輪郭を抽出し、その輪郭線からの乖離が大きい部分を不良として認識する処理)」を使えば、オイルシールのような変形しやすく不安定なワークでも正確に輪郭検査できます。これによりバリや割れ・欠け(クラック)のような検知が難しかった不良も正確に判別可能です。各種パラメータ設定により、検出したい欠陥のレベルも自由に指定できます。
また、画像処理システムは、輪郭計測と同時に表面のキズや汚れなどのチェックもでき、生産を止めることなくインラインで外観検査が完了するので生産効率向上に効果的です。目視検査のように作業員によるばらつき・見落としも排除でき、品質向上にも効果を発揮します。

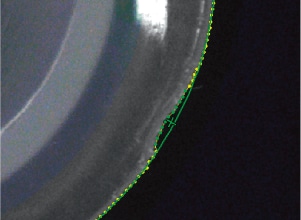
まとめ
このページでは、オイルシールの輪郭の外観検査に必要な基礎知識や、トラブルと外観検査の方法についても紹介しました。それらをまとめると、以下の通りです。
- オイルシールは、オイル(油)をシール(封じる)するための部品で、ゴム製が一般的だが金属や樹脂などもある。
- ゴム製のオイルシールは形状が不均一なので輪郭検査の自動化が困難。
- キーエンスの画像処理システムなら、変形しやすく不安定なワークでも、インラインで正確に自動判別可能。
ワークによって、外観検査の方法もさまざまです。最適な外観検査を行うには、それらの特徴を知り、正しく検査することが大切です。
このページで紹介した内容や、他のページに記載している外観検査の知識を1冊にまとめた資料「外観検査のすべて」は、下記からダウンロードできます。画像処理システムの導入事例集とあわせてご覧ください。