【製造業】電機・電子デバイス・半導体
製造業の中でも電機・電子デバイス・半導体に絞って実際の活用事例を紹介します。電機・電子デバイス・半導体の各工程における課題、ハンディターミナルを導入するメリットを事例を交えて解説します。
- 電機・電子デバイス・半導体の製造について
- 電機・電子デバイス・半導体の製造における課題
- ハンディターミナル導入による課題解決
- 代表的な工程と製造の流れ
- 工程別 ハンディターミナル導入によるメリット
- 文字認識ハンディターミナルで運用改善
- まとめ
電機・電子デバイス・半導体の製造について

スマートフォンやゲーム機、パソコン、そのほか家電製品の小型化・薄型化が進み、それに伴い電機・電子デバイス・半導体の製造および検査工程ではより精密さが求められるようになりました。電子デバイス・半導体は集積化が進み、ニーズの多様化によって多品種少量生産やセル生産が一般的になり、部品管理や検査の手間とコストは増大しています。
ICチップや抵抗、コンデンサ、トランジスタのような微細な部品は、個別に品番をマーキングすることが難しく、目視での判別も難しいため取り違えが発生しやすいものです。ニーズの多様化により類似品も増え、製品サイクルも短くなっているので製品管理の手間も増えています。そこで部品・製品の管理などでハンディターミナルが活用されています。
電機・電子デバイス・半導体の製造における課題
電機製品や電子機器、半導体の製造現場では、機械トラブルや部品材料の欠品、不良などさまざまな問題を抱えています。これらを原因とする生産遅延はどんなに気を付けていても発生する可能性をゼロにできないので、トラブル発生を察知して迅速にリカバリーする体制づくりが大切です。そのためには、現場の状況をリアルタイムに把握する必要があります。
また、製造原価を改善するには、製造や作業に要した時間を正確に知る必要があり、工程管理と実績収集が製造現場改善のカギと言えます。その解決策としてハンディターミナルが活用されています。
ハンディターミナル導入による課題解決
電子機器製造の現場で近年多く採用されている生産方式に「屋台方式」があります。この生産方式は、多品種の組み立てを1人または少人数で対応するため、細かい作業指示や部品供給に臨機応変に対応する必要があります。ハンディターミナルなら、バーコードをスキャンするだけで製品ごとの作業指示や必要な部品の在庫の有無まで確認できるので効率的です。このほかにも多くの工程でハンディターミナルは活用されています。
例えば製造現場全般に言えますが、正しい生産計画を立て、計画どおりに生産することが重要です。しかし、原材料や部品、仕掛品、完成品の在庫を正確に把握できていなければ、正確なスケジュールを立てることは不可能です。とくに欠品などが生じていると、生産現場だけでなく資材倉庫や出荷セクションが大きく混乱し、予定した工程や数量をこなせなくなります。
帳簿上で在庫の管理が正しく行われていれば問題ありませんが、伝票の記入ミスやポカミスなどその他の要因で必ずしも実在庫を反映しているとは限りません。その点、ハンディターミナルならバーコードと現品票をスキャンするだけでミスのない在庫管理が可能です。現品の正確な数量や保管場所をつねに把握でき、欠品があっても迅速な補充対応ができます。このようにハンディターミナルを導入することで各工程の効率化に加え、生産全体の健全化を図ることができます。
代表的な工程と製造の流れ
電機・電子デバイス・半導体の製造における具体的なハンディターミナルの導入事例を工程別に説明します。電機・電子デバイス・半導体の代表的な工程と製造の流れは以下のようになります。
仕入先
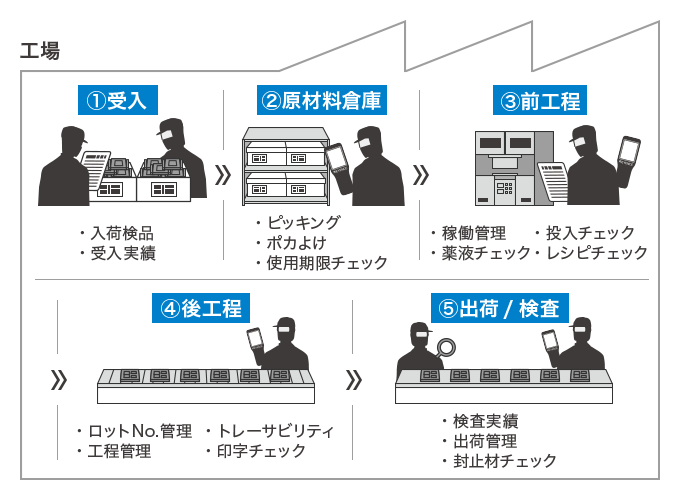
- 完成品倉庫
-
- 出荷検品
- 在庫管理
- 棚卸し
工程別 ハンディターミナル導入によるメリット
上述の代表的な工程別にハンディターミナルを導入するメリット、実際の活用事例を説明します。
受入
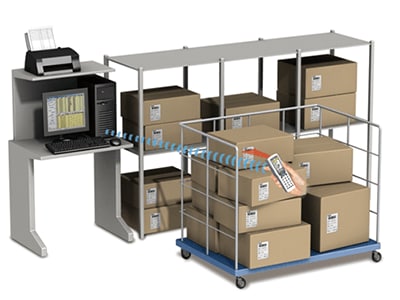
目視で伝票を確認する場合、どれだけ注意しても一定の割合で読み間違いが発生します。しかし、ハンディターミナルを使い、付与されているバーコードなどを読み取ることでミスをゼロに近づけることが可能です。すぐに受入実績データ化できるので、後から手入力する手間も省けます。
また、製造ラインで使用する際も自動的に在庫移動処理が行われるので、人による記録やデータ入力が省略でき、正しい在庫管理が可能になります。入荷検品/受入検査の精度が大きく向上します。
原材料倉庫
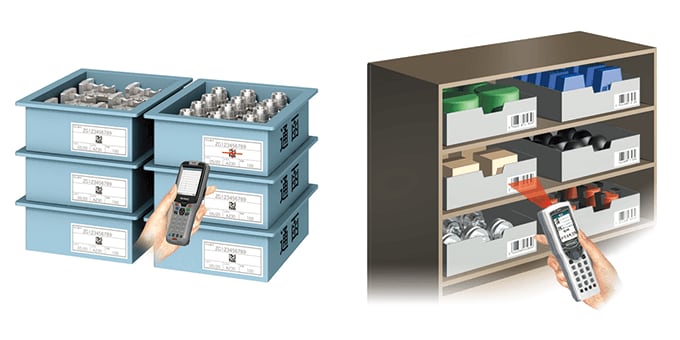
目視による検品で入荷時にミスがあると、ピッキングの際に混乱が生じ、その後の製造工程で大きなロスが生まれます。ハンディターミナルとバーコードを活用して商品情報、棚情報を関連付けておけば、確実なピッキング作業の実現と棚卸管理の効率化、照合作業のスピードアップなど、作業の迅速化・確実化が図れます。また、原材料が使用期限を過ぎている場合はハンディターミナルが警告を発し、誤って現場に供給するのを防ぎます。
前工程
原材料の調合や機械加工、表面処理、露光処理などの加工・製造工程を前工程とします。この前工程でトラブルが発生すると、後工程や納品に大きな影響が出ます。ハンディターミナルを導入すれば、全体の稼働管理や薬液チェック、投入チェック、レシピチェックがリアルタイムで行えるので、問題があればその場で対応することができて後工程の停滞を防ぐことができます。
また、ハンディターミナルは部材や製品のほか、消耗品・設備・工具の使用状況や消耗状況も知ることができ、設備管理における予防保全としても有効です。
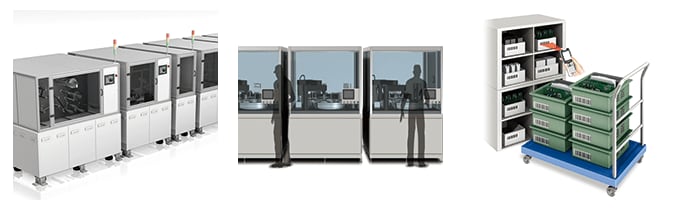
後工程
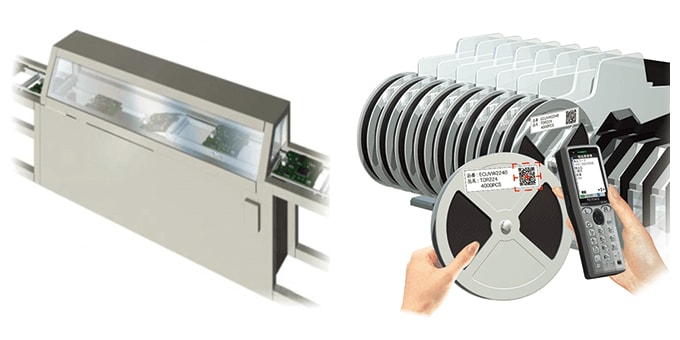
後工程は、組立工程のほかはんだ付けなどの実装・組立工程を指し、代表的なトラブルとしては「組み付けミス」「はんだ不備」などが挙げられます。屋台方式の生産の場合、複数の部品を取り扱うのでミスが発生しやすくなりますが、ハンディターミナルを導入すれば作業手順や部品の確認が簡単に行えます。製品・部品コードをスキャンするだけで、作業手順までディスプレイに表示してくれるので時間と労力の節約になり、ミスを防げます。またロットNo.の管理や工程管理、トレーサビリティも効率化できます。
出荷・検査

ハンディターミナルを導入すれば、システムと連携して製品シリアル登録を自動化できます。在庫管理も簡略化でき、出荷や検品のスピードもアップします。またハンディターミナル導入により製品トレーサビリティが格段に向上するので不良品発生など不測の事態でもすぐに原因となった工程を特定できます。しかも検査実績はその場でデータ化されるので、品質向上へどう取り組むべきかが明確になります。
完成品倉庫
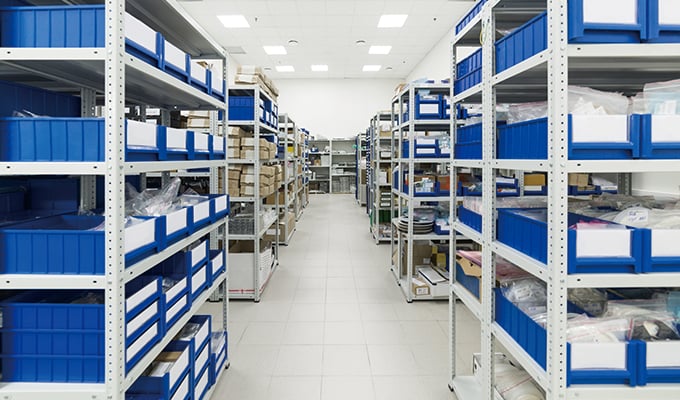
完成品は、自社の完成品倉庫で納品を待ちますが、目視に頼らない出荷検品により誤出荷が大幅に軽減されます。また、ハンディターミナルとシステムの連携で在庫管理や棚卸しの効率化が図られます。
文字認識ハンディターミナルで運用改善
電機・電子デバイス・半導体製造の現場では、シリアルNo.やロットNo.がバーコード化されていないこともあります。そのような場合、これまでは目視検査に頼っていました。シリアルNo.やロットNo.のほか、装置のデータなども目視検査を必要とする代表的な例です。これら目視検査を文字認識(OCR)対応のハンディターミナルに置き換えることで、確実かつスピーディに作業ができ、ミスの撲滅や作業効率改善に効果的です。キーエンスのハンディターミナル「BTシリーズ」は、文字認識(OCR)に対応しているので、以下のようなシーンで力を発揮します。
作業指示書と装置のデータ照合
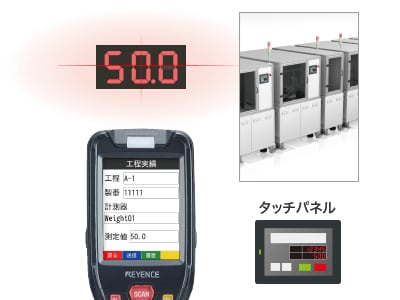
製造の現場では、様々なメーカーの装置を使用しています。文字認識(OCR)対応のハンディターミナルなら装置に表示されている7セグ文字も読み取り可能です。目視のように読み取りミスもなく、スキャンするだけで目視・手書き・パソコンへの手入力という工程を終えられるので作業の効率化で確実なデータ管理が実現します。
従来
- 目視チェック&手書き&
パソコン手入力
改善
- シリアルNo.をスキャンするだけ。
ラクラク入力
まとめ
このページでは、電機・電子デバイス・半導体の製造における課題と、ハンディターミナル活用による改善事例を紹介しました。まとめると以下の通りです。
- トラブル発生による生産遅延を迅速にリカバリーするには、現場の状況把握が重要
- リアルタイムな工程管理や実績収集には、ハンディターミナルの活用が有効
さらに、ハンディターミナルを活用することで、以下のようなメリットが得られます。
- モノと棚の情報を関連付け、迅速かつ確実な入庫/ピッキング/在庫管理が可能
- 出庫/投入する原材料の使用期限を警告してトラブルを防止
- 工程での作業手順の表示やチェックができ、ポカヨケと同時に工数などの実績管理が可能
- 受入から各工程、完成品出荷までの情報を一元管理でき、トレーサビリティを向上
キーエンスのハンディターミナルには、この他にも文字認識(OCR)機能が搭載されており、指示書やプロセス装置に表示された文字の読み取りなど、さまざまな場面で役立ちます。
その活用方法や導入手順をまとめた資料「ハンディターミナル活用ガイド」を下記よりダウンロードいただけます。商品カタログとあわせてご覧ください。