お客様導入事例カンロ株式会社 様
カンロ株式会社研究・技術本部エンジニアリング部 朝日工場設備管理チームリーダー兼田 義一氏、小林 良成氏にUVレーザーを導入した経緯とその効果について詳しく聞きました。
「ピュレグミ」への賞味期限印字にUVレーザーを採用

印字が消えない、ラインが止まらない、消耗品がない、
UVレーザーのすべてに満足しています。

カンロ株式会社について
カンロは、1955年発売した「カンロ飴」を皮切りに「健康のど飴」「ピュレグミ」「金のミルク」など数々のヒット商品を世に送り続けているキャンディ専業メーカーです。
「糖から未来をつくる。」をコーポレートメッセージとして常に世の中に求められる糖の在り方・役割とは何かを追求し、お客様のニーズに合った商品を展開しています。
UVレーザーを検討することになった背景について教えてください
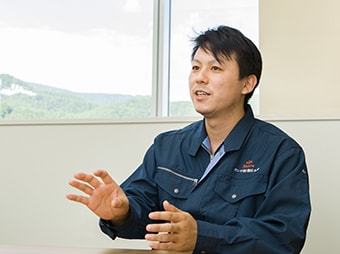
大きく2つありまして、1つが印字品質の改善、もう1つがランニングコストの低減です。当時、弊社ではサーマルプリンタを使用していたのですが、慢性的に発生する印字不良の対策が継続的な課題となっていました。製品特性上仕方のないことなのですが、製造過程で発生する粉が包装フィルムの表面に付着するため、サーマルプリンタで日付を印字した後の工程において、フィルムの巻き取りや挟み込みなど印字部分が接触すると印字欠けが発生するリスクがありました。また、サーマルヘッドの素子に溜まる堆積物や、温度調整部品の劣化により、部分的にうまくインクが転写されず、印字に筋が入ってしまうといった不良も発生していました。ランニングコストについても、日々のインクリボン交換だけでなく、サーマルヘッドの交換スパンが当初想定していたより短かったり、安定稼働のために毎年メーカー保守点検をしたりと、費用面の負担も発生していました。「もっと弊社のラインに最適な印字方式はないのか」という思いから情報収集をおこなっていく中で、UVレーザマーカ(MD-Uシリーズ)を紹介していただき、導入に向けたテストを実施することになりました。
導入時には、UVレーザーの他にも色々な印字方式と比較しながら検討していたのですが、正直UVレーザーの第一印象は、「お値段が高い」でした(笑)。ただ、テストを進めていくうちに、「絶対に印字が消えない」というメリットだけでなく、検証の結果「包材にもダメージがない」ことがわかり、もちろんレーザーなので消耗品コストもかからないことから、当時弊社が抱えていた課題を解決する手法として最適であると判断しました。もちろんこれまでとはまったく違う新しい印字手法なので、当時はインク方式に比べて「印字が黒ではなくグレーに見える」といった声もありました。そこで、そもそもの印字の仕組みが違うことを説明できる比較資料を用意したり、できるだけ視認性のあるUVレーザーでの印字サンプルを用意したりと、キーエンス営業担当の方からの協力も得ながら、懸念点を1つずつクリアして、最終的には導入に至りました。
UVレーザー導入後の効果を教えてください

絶対に消えない印字ができる、ランニングコストがかからない、といった当初想定していた効果は期待通りに発揮できているのですが、実はもう1つ驚いたことがありまして、それが「生産ラインのダウンタイムが無くなった」という効果です。従来の印字方式でトラブルが発生すると、製造ラインを停止してメンテナンスをおこなう必要があり、メンテナンス内容によって現場担当者で対応できるものとそうでないものがありました。例えば、サーマルヘッドの反対側に設置する当て板の調整は熟練度が要求され、社内の限られた人間か、メーカーの技術者を呼んでの調整が必要でした。メンテナンス作業が長引くと、決められた時間内で1日に目標とする生産量に届かなくなるので、製造時間を延長して生産する、もしくは翌日に持ち越すといった対応が必要でした。UVレーザーを導入してからは、その1日の製造遵守率を約3.5%向上させることができました。これは同じ稼働時間のままで、1ラインで約7万個/月多く生産できるようになったことを意味しておりまして、弊社としては大変インパクトの大きな改善となっております。我々設備管理チームの使命は「いかに生産設備の故障停止時間をなくせるか」なのですが、今回のUVレーザーの導入によって、製造現場の皆さんの作業効率化にお役立ちできていると実感しています。
その他、UVレーザー導入後にわかったことなどあれば教えてください
あとは、包材フィルムやサーマルインクリボンの廃棄物がなくなったことも効果の1つとして感じています。従来では印字不良が発生した場合、フィルムの再利用ができないため、その分廃棄に回っていました。さらには、インクリボンの交換を1日に1回はおこなっていたので、その交換タイミングでラインを停止させるたびに、品質リスク回避のため、フィルムを一定量廃棄する必要がありました。こういったフィルム廃棄が不要になったことで、弊社のフィルムロスを3%弱削減することができています。もちろん、使い終わったインクリボンも廃棄物になりますし、従来では使用する前のインクリボンだけでなく、使用後のインクリボンについても、商品の賞味期限を迎えるまではトレーサビリティのために保管をしていたので、その管理の手間もなくなりましたね。今では、キーエンスのビジョンデータベースというソフトを活用して、印字検査画像を全数保存する方法に変えることでトレーサビリティを担保できています。
今後の、UVレーザーの活用方針について教えてください
導入から約10カ月が経過し、当初想定した以上の効果を確認できましたので、来期は他の包装工程にも追加でUVレーザーを採用する予定にしています。導入当初は、まったく新しい印字方法に変わったことによる不安の声もあったのですが、印字トラブルがまったく起こらなくなった今となっては「なんでもっと早く導入しなかったのか」といった声も聞こえてきてUVレーザーを認めていただけていると感じています。食品への日付印字は市場に不良を流出させてはならない重要度合いの高いものですから、そこに気を揉まなくてよくなった、という意味でも本当に良い印字機と考えているので、今後も各工程で活用していこうと思っています。

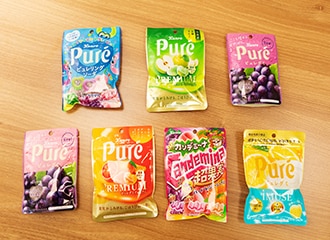

ピュレグミをはじめ、各種パッケージにUVレーザマーカMD-Uシリーズで日付印字をおこなっている