お客様導入事例シャボン玉石けん株式会社 様
シャボン玉石けん株式会社 製造部 部長 古市真氏にUVレーザプリンタを導入した経緯とその効果について詳しく聞きました。
シャボン玉石けんへのロット番号印字にUVレーザプリンタを採用

UVレーザプリンタ導入により「印字不良ゼロ→商品の品質アップ→働く人のやりがいアップ」に繋がっています

シャボン玉石けん株式会社について
シャボン玉石けんは、「健康な体ときれいな水を守る。」を経営理念に据え、化学物質や合成添加物を一切含まない無添加石けんの製造・販売をおこなっているメーカーです。持続可能な社会形成、地球環境への配慮に対して世界中の関心が高まっている中、天然素材だけを使った本物の無添加シャボン玉石けんは年々その需要が増しており、無添加化粧石けんジャンルにおいて大きなシェアを獲得しています。
UVレーザプリンタをご検討いただくことになったきっかけを教えてください
当社ではもともと、スタンドパウチの充填包装ラインの印字ではホットプリンタを使用していたのですが、「印字不良の発生リスク」に悩まされており課題を持っていました。ホットプリンタによる印字不良の原因には大きく2つありまして、それが「パウチのヒートシール部の厚み違い」と「ホットプリンタの版(刻印)の調整不備や摩耗」でした。
まず1つ目の「パウチのヒートシール部の厚み違い」についてですが、前提として弊社ではスタンドパウチのバリア性を担保するという観点から、パウチの胴体部分ではなくパウチ下部のヒートシール部への印字をおこなう運用をしています。ただし、このヒートシール部にはスタンドパウチ自体の製造過程の中で凹凸の厚み違いが発生するため、接触式のホットプリンタでの印字では、フィルムの厚い箇所と薄い箇所で接触圧が変わり印字不良に繋がるケースがありました。
また、2つ目の「ホットプリンタの版(刻印)の調整不備や摩耗」についてですが、ホットプリンタは印字内容が変わるたびにピンセットを使って人の手で版を入れ替えるのですが、7桁の印字をするなら7本全ての版の高さ・奥行きを揃える必要があり調整に苦労していました。仮に、7本のうち1本だけ高さが異なれば他の版と比べ接触圧が異なるため印字不良に繋がります。もちろんそういった調整不備以外にも版の摩耗が進むことで明瞭に印字できず「8」「3」「6」などの似た版の文字の区別がつきにくくなるといったケースも発生していました。そのような状況の中、当時長年使用していたホットプリンタが更新時期を迎えたタイミングで、ちょうどキーエンスの営業担当者からUVレーザプリンタなら「絶対に消えない印字ができる」ということで紹介を受け、検討することになりました。
UVレーザプリンタをご採用いただくことになった決め手を教えてください
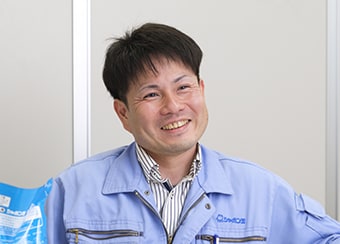
一番の決め手は、当社の「人にやさしいものは、自然にもやさしい」という考え方のもと進めているSDGsの取り組みにとってUVレーザプリンタが最適な機器である、と判断したからです。当社は人と環境にやさしい商品づくりを使命としておりますが、この考え方は生産ラインに対しても同様で、現場作業者の不要な負担を減らすことで、より意欲的に価値の高い仕事に取り組める環境を目指しています。
例えば、従来印字不良が発生した場合は、スタンドパウチをリパックして中身の石けんは再利用するのですが、石けんの品質を確実に担保するため、途中の充填工程からではなく、最初の上流工程まで戻して各フィルタ工程等を通し直す必要があり、この上流工程に戻す作業も人の手で重い液体を運ぶ負担が生じていました。UVレーザプリンタ導入により印字不良が根本的に解消することで、このような現場作業者の負担をなくすことができると判断し導入することに決めました。
UVレーザプリンタ導入後の効果を教えてください
実際に導入して、当初の期待通り印字不良はゼロとなり「絶対に消えない印字」のメリットを実感しております。当社では、毎日ロットごとに品質管理部門による印字チェックを行っているのですが、従来は印字不良の懸念が生じると一度ラインを止めて、印字不良に繋がる要因の特定と解消をおこない、品質管理部門への報告のうえ再度生産を開始するという流れを取っておりますので、生産ラインのダウンタイムが生じていました。UVレーザプリンタ導入後は、消えない印字に変わったことで従来のような突発的な印字不良対策に時間を割くことも、関連部署からの指摘も一切無くなりました。
加えて大きな効果として実感している点が、生産効率が飛躍的に向上した点になります。当社の生産ラインは1つの充填ラインで複数品種の生産を行っており、多い時では1日6種類程度のサイズが異なるパウチに切り替える段取り替えが発生します。従来の接触式のホットプリンタの場合は、パウチの種類が切り替わるたびに物理的にヘッドを動かして印字位置調整を行う必要があったため、1回の段取り替えで10分程度のダウンタイムが発生していました。UVレーザプリンタは、ヘッドを物理的に動かすことなくタッチパネル上で自由に印字位置の調整ができるため、段取り替えにかかる時間が圧倒的に短縮されました。
具体的には、従来は生産ラインを実際に稼働させて生産活動に充てられていた時間は1日の中で6時間だったのですが、UVレーザプリンタ導入後は段取り替え工数が減ったことで1日7時間まで増やすことができております。結果として、ラインの生産効率が約16~17%上がり、1日全体の稼働時間は全く変えていないにも関わらず年間で約250時間、60万個多く商品を生産できるラインに変わりました。既存ラインの生産能力が上がったことで、生産設備の増設などをおこなうことなくシーズンごとに異なる目標生産数量に対して柔軟に対応できるようになり、お客様の手元により早く確実に商品をお届けできるようになった点もメリットと感じております。
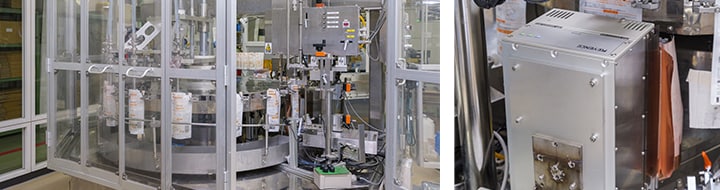
40回転/分の充填包装機にキーエンスのUVレーザプリンタを搭載
その他、UVレーザプリンタ導入後に分かったことなどあれば教えてください
従来発生していた不要な負担と時間が無くなったことが、商品自体の品質・働き手のやりがい双方に直結していると感じています。
当社の生産部門の使命は「お客様がリピートして買っていただける商品」を目指し高い品質を追求することです。商品の価値を決める要素は“品質の標準化”や“泡立ち”など多岐に渡り、現場作業者の方々にはこれらの付加価値を生み出す仕事のノウハウを磨いてほしいと考えており、こういった仕事にこそやりがいと楽しさがあります。プリンタのトラブルに時間が取られなくなった分、商品の付加価値を上げる仕事に注力できる時間が増え、結果として商品の品質向上にも、働き手のやりがい向上にも、どちらにも繋がっていると感じています。今後もUVレーザプリンタには期待しています。

シャボン玉石けんのパッケージにUVレーザプリンタで日付印字をおこなっている。スタンドパウチの凹凸があるヒートシール部にもしっかり印字ができている。